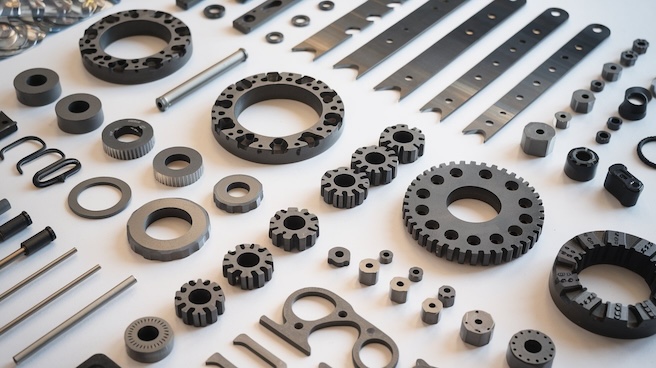
Tungsten Carbide Preforms
Tungsten carbide preforms play a crucial role in various industrial applications, serving as the foundational material for producing high-performance components. Known for their exceptional hardness, durability, and precision, these preforms are essential in industries ranging from mining and manufacturing to automotive and electronics.
Quick and easy: Enter your specifications and get a quote in one business day
Table of Contents
Types of Tungsten Carbide Preforms Components
Retop offers tungsten carbide preforms as products or custom manufactures complete, custom-made tools, wear parts and specialty components.
Types of Tungsten Carbide Preforms
- Seal Rings
- Saw Blades
- Drill Blanks
- Milling Tool Blanks
- Roto Knives
- Wear Parts
- Can Tooling
- Forming Rolls
- Powder Compacting
- Stamping
- Dies
- Cutters
- Bushings
- Rods
- Oil Field
- Slitter Knives
- Bed Knives
- Punches
- Automotive
- Balls
- Seats
- Nozzles
- Plates
What Are Tungsten Carbide Preforms & Tungsten Carbide Blanks?
Tungsten carbide preforms & Tungsten carbide blanks are shaped blanks made from a composite material consisting primarily of tungsten carbide grains bonded with a metal, typically cobalt.
These preforms serve as the starting point for manufacturing a wide range of high-precision tools and components.
They are produced through processes like pressing, sintering, and machining, ensuring that they possess the necessary strength and structural integrity required for various applications. Preforms are designed to be further processed into final products, offering manufacturers flexibility in creating customized solutions tailored to specific industry needs.
These industries include, but are not limited to: Oil & Gas, Automotive, Mining, Manufacturing, Beverage & Aerosol, Housing, Medical and Recycling.
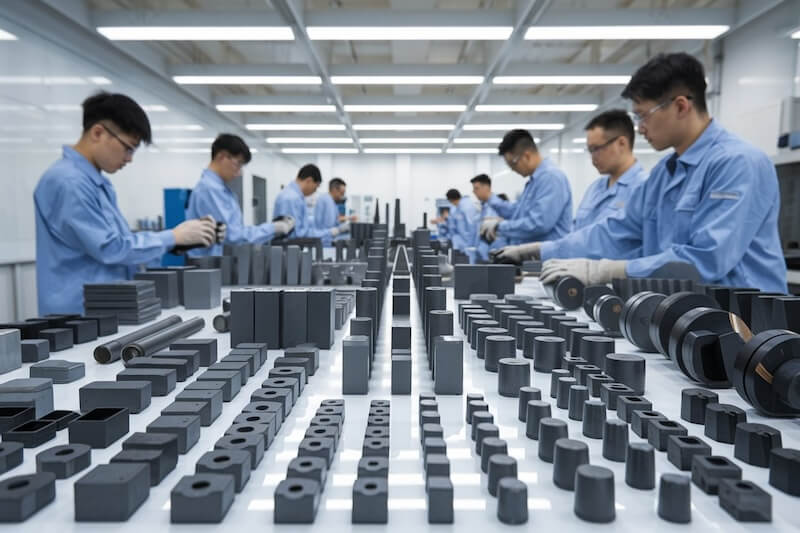
Composition of Tungsten Carbide Preforms
Tungsten carbide preforms are primarily composed of tungsten carbide (WC) particles and a metal binder, usually cobalt (Co). The typical composition includes:
- Tungsten Carbide (WC): Provides exceptional hardness and wear resistance, making the preforms suitable for high-stress applications.
- Cobalt (Co): Acts as a binder, enhancing the toughness and overall structural integrity of the preform.
Additional elements such as nickel or titanium may be added to improve specific properties like corrosion resistance or thermal stability. The precise ratio of tungsten carbide to the binder metal can be adjusted to achieve desired characteristics, allowing for customization based on application requirements.
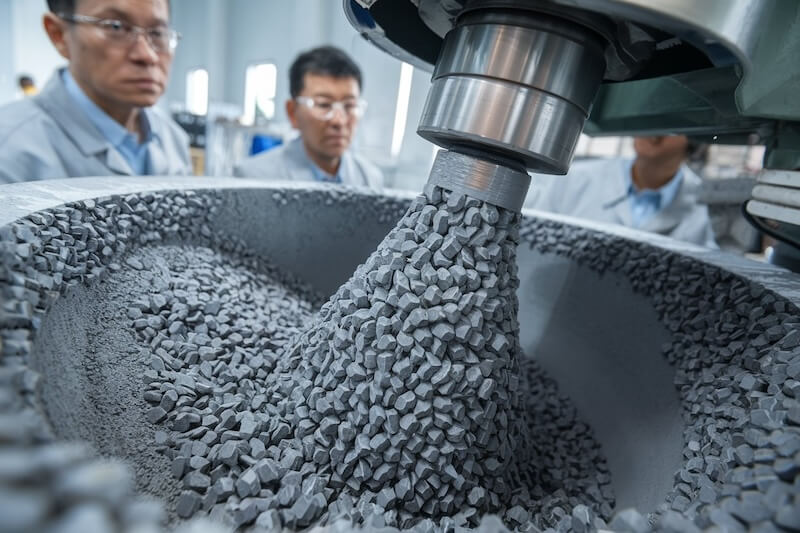
Differences Between Tungsten Carbide Preforms and Finished Tungsten Carbide Products
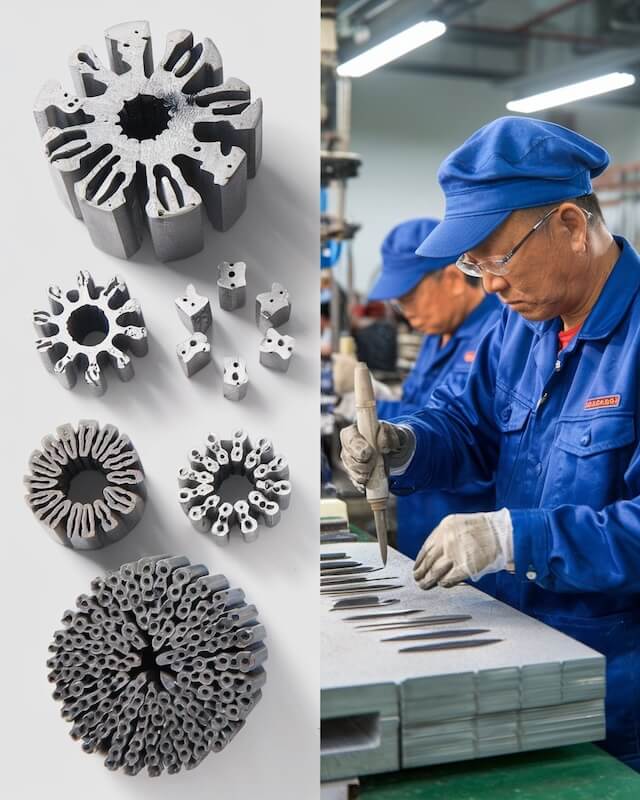
While both tungsten carbide preforms and finished products are made from similar materials, they serve different purposes in the manufacturing process:
Tungsten Carbide Preforms:
- Serve as the foundational blanks for further processing.
- Typically unshaped or in basic shapes like rods, blocks, or discs.
- Require additional machining, grinding, or polishing to achieve final specifications.
- Offer manufacturers flexibility to create customized shapes and sizes.
Finished Tungsten Carbide Products:
- Fully machined and finished components ready for use in specific applications.
- Shapes and sizes are tailored to meet precise industry standards and requirements.
- Undergo additional treatments such as coating or heat treatment for enhanced performance.
- Directly used in applications like cutting tools, wear-resistant parts, and precision instruments.
Understanding the distinction between preforms and finished products is essential for manufacturers to effectively utilize tungsten carbide in their production processes.
Applications of Tungsten Carbide Preforms
Tungsten carbide preforms are integral to a variety of industries due to their superior properties. Key applications include:
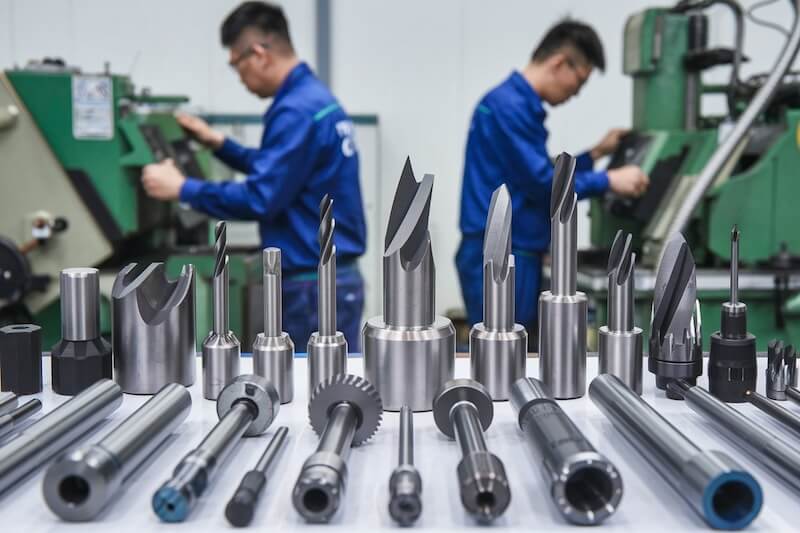
Cutting Tools
Used as blanks for making drills, milling cutters, and saw blades that require high precision and durability.
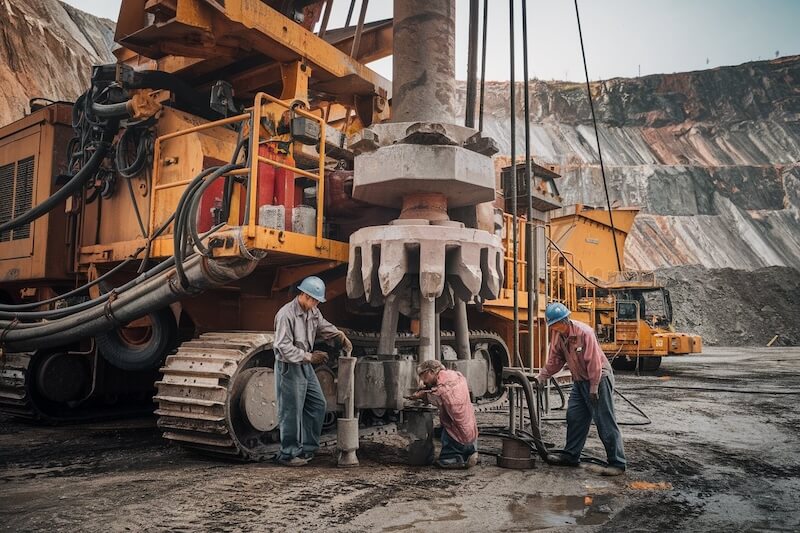
Mining Equipment
Serve as the base for components like wear-resistant bits and cutters that endure harsh conditions.
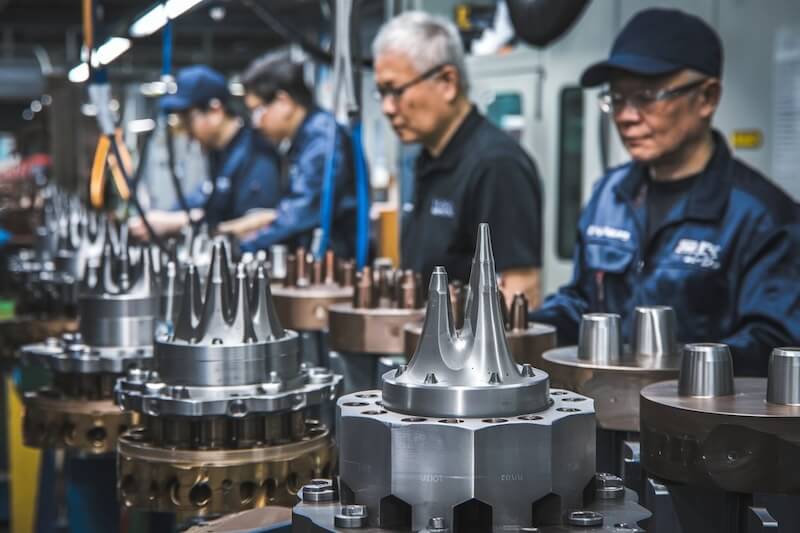
Automotive Industry
Used in manufacturing high-performance parts such as engine components and transmission parts.
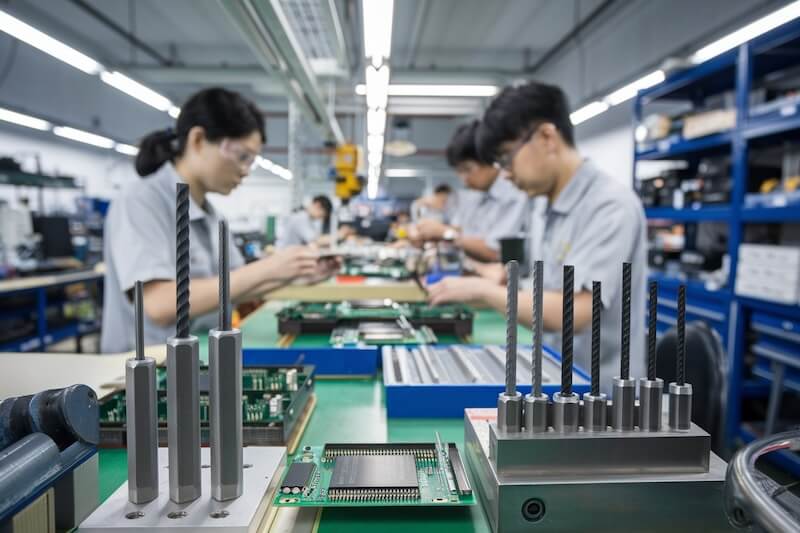
Electronics
Form the basis for precision tools used in the fabrication of electronic devices.
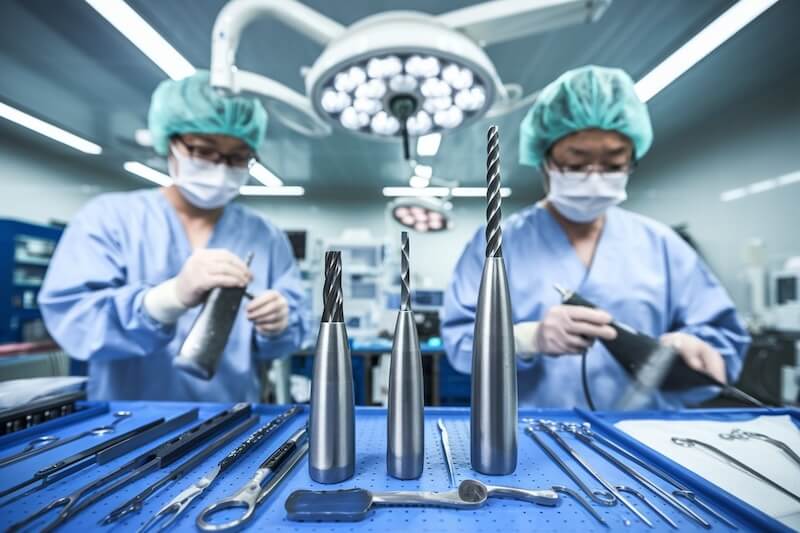
Medical Devices
Utilized in making surgical instruments that require high precision and biocompatibility.
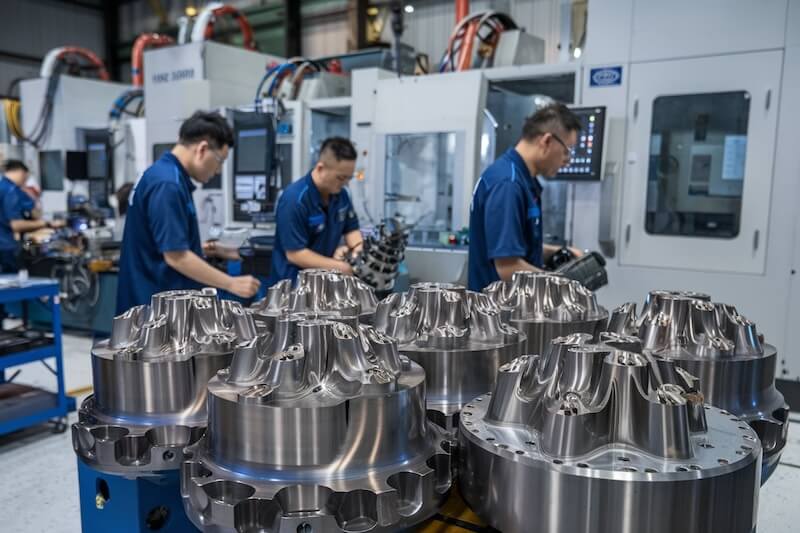
Aerospace
Employed in creating components that must withstand extreme temperatures and mechanical stresses.
The versatility of tungsten carbide preforms makes them indispensable in producing components that demand high performance and longevity.
Quick and easy: Enter your specifications and get a quote in one business day
Benefits of Using Tungsten Carbide Preforms
Choosing tungsten carbide preforms offers several advantages:
- Exceptional Hardness: Provides superior wear resistance, ensuring longer tool life and reduced maintenance costs.
- High Precision: Enables the production of components with tight tolerances and intricate details.
- Durability: Resistant to deformation and wear, making them ideal for demanding applications.
- Thermal Stability: Maintains structural integrity under high temperatures, suitable for high-speed machining.
- Versatility: Can be customized into various shapes and sizes to meet specific application needs.
- Cost-Effective: Reduces the need for frequent replacements due to their long-lasting nature.
These benefits make tungsten carbide preforms a preferred choice for manufacturers seeking reliable and high-performance materials.
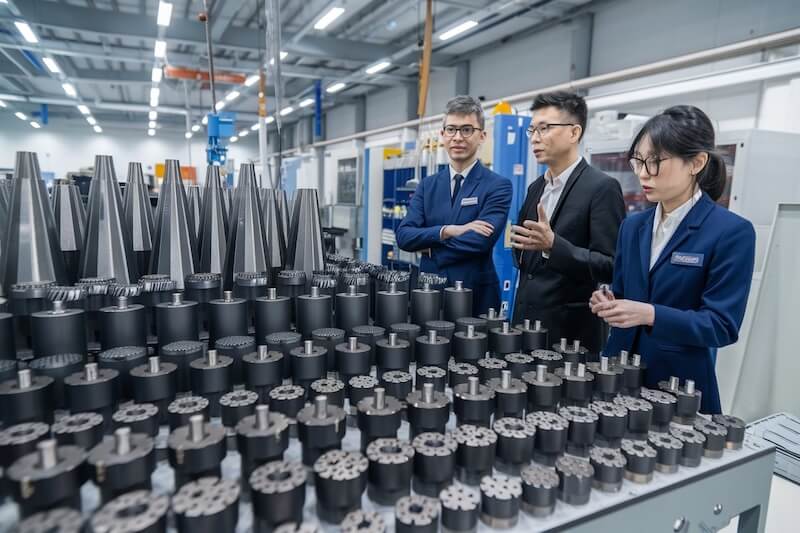
Who Needs to Buy Tungsten Carbide Preforms?
Tungsten carbide preforms are essential for a wide range of professionals and industries, including:
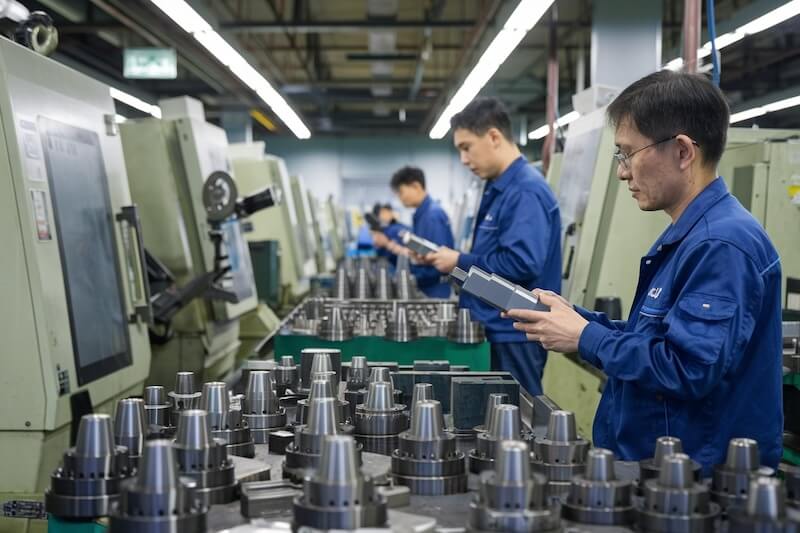
Tool Manufacturers
Companies producing cutting tools, drills, and machining equipment.
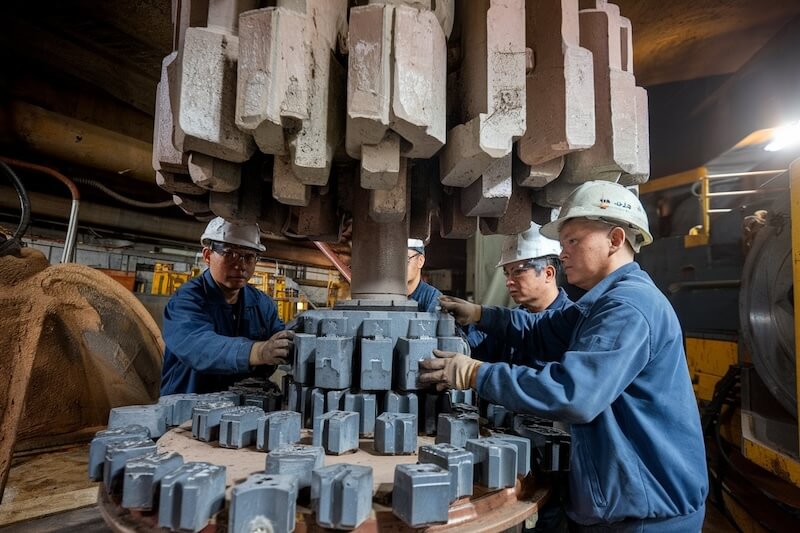
Mining Industry
Manufacturers of mining equipment that require durable and wear-resistant components.
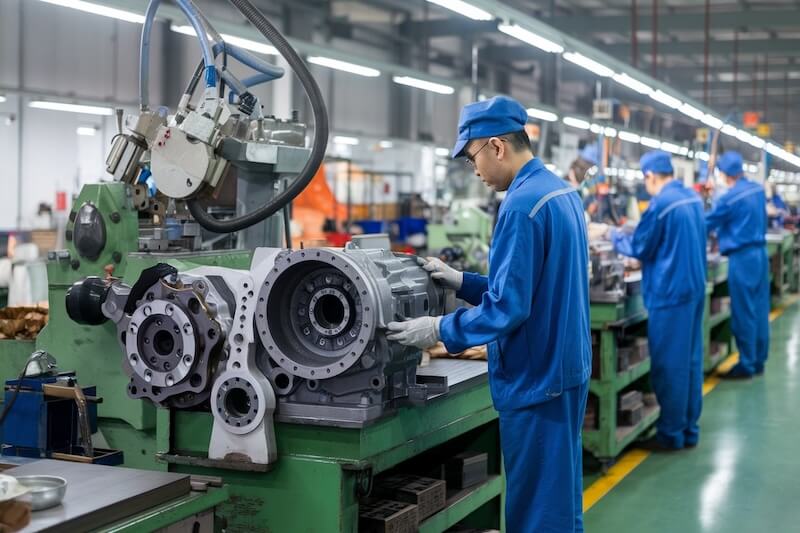
Automotive Sector
Producers of high-performance automotive parts and components.
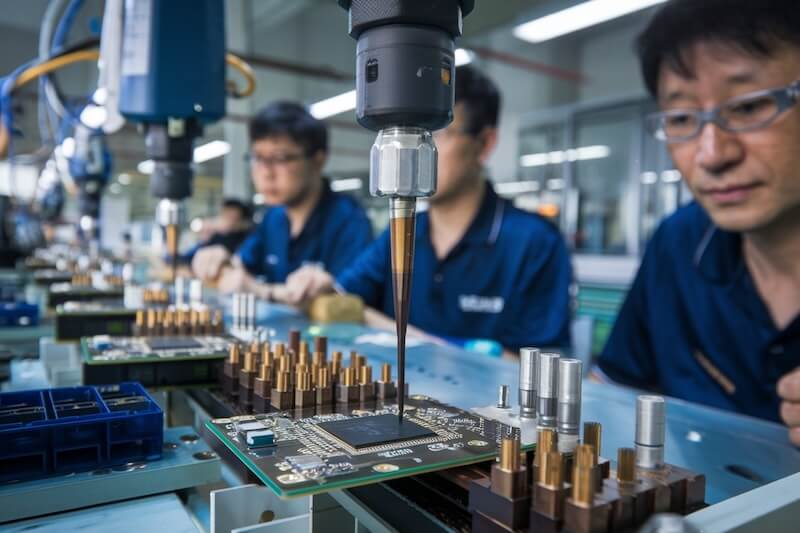
Electronics Manufacturers
Companies involved in the precision fabrication of electronic devices and components.
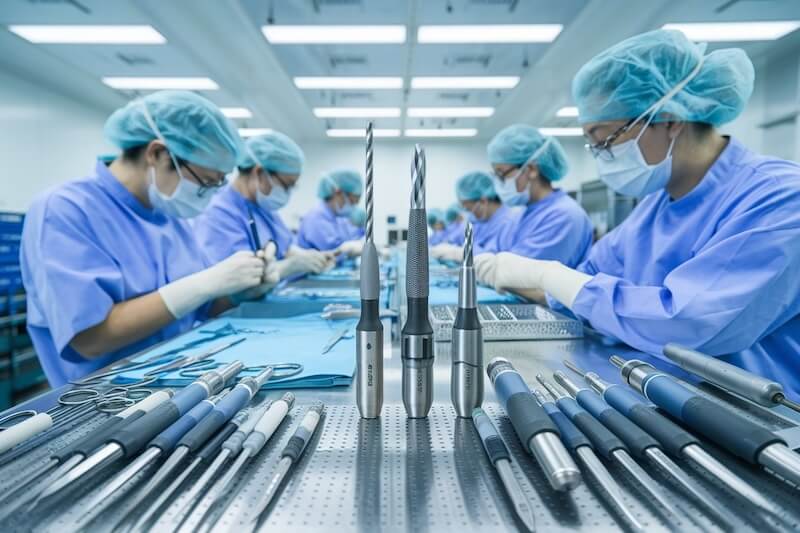
Medical Device Manufacturers
Producers of surgical instruments and medical tools requiring high precision.
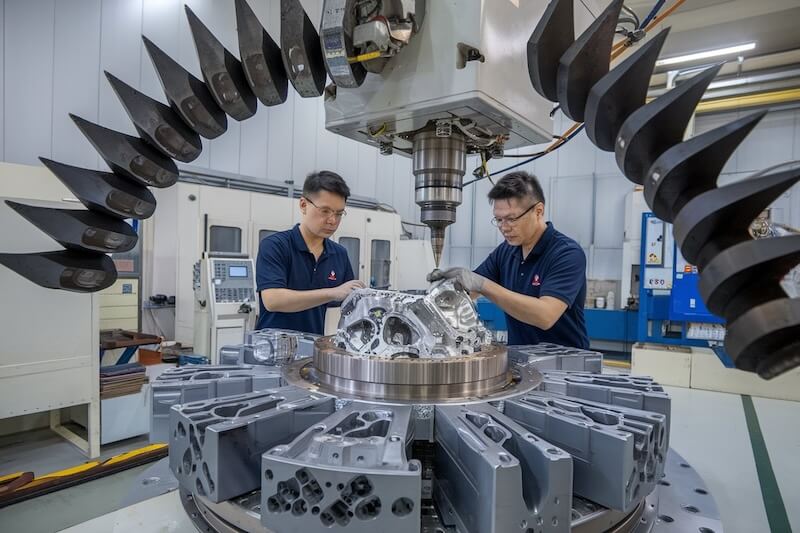
Aerospace Industry
Manufacturers creating components that must withstand extreme conditions and stresses
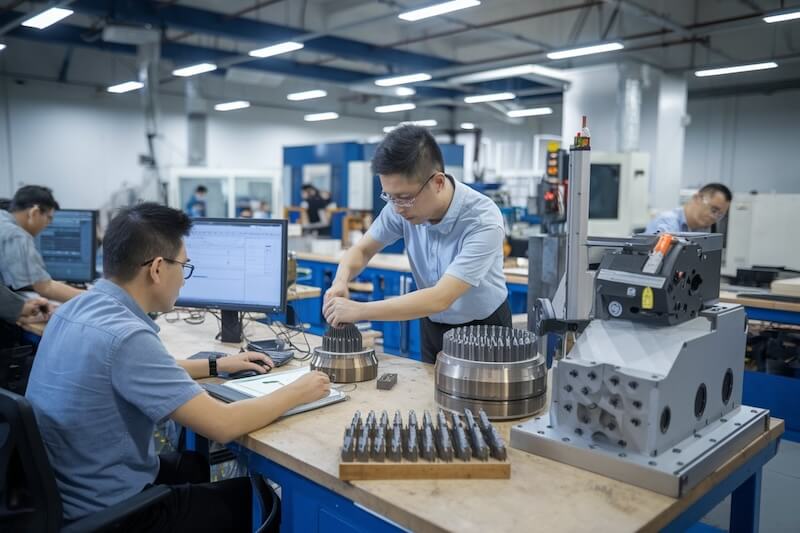
Engineering Firms
Companies involved in designing and producing custom machinery and equipment.
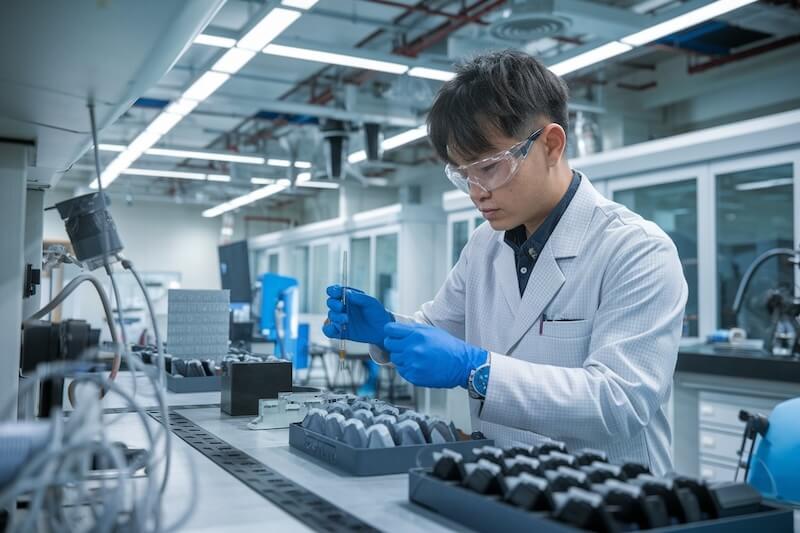
Research and Development
Laboratories and institutions developing new applications and technologies involving tungsten carbide.
These buyers seek high-quality preforms to ensure the performance and reliability of their final products.
How to Choose the Right Tungsten Carbide Preform Manufacturer
Selecting the appropriate manufacturer is critical to obtaining high-quality tungsten carbide preforms. Consider the following factors:
- Quality Control: Ensure the manufacturer has stringent quality assurance processes and relevant certifications (e.g., ISO 9001).
- Customization Capabilities: Look for manufacturers that offer flexibility in shaping, sizing, and material composition to meet specific needs.
- Experience and Reputation: Choose established manufacturers with a proven track record and positive customer reviews.
- Technical Expertise: Ensure the manufacturer has the necessary technical knowledge and skilled personnel to produce precise preforms.
- Production Capacity: Verify that the manufacturer can handle your order volume and meet your lead time requirements.
- Material Sourcing: Confirm that the manufacturer uses high-grade raw materials and maintains reliable supply chains.
- Pricing: Compare pricing structures to ensure competitive rates without compromising on quality.
- Customer Support: Opt for manufacturers that provide excellent customer service, including technical support and after-sales assistance.
By evaluating these factors, buyers can ensure they partner with a reliable manufacturer that meets their quality and performance standards.
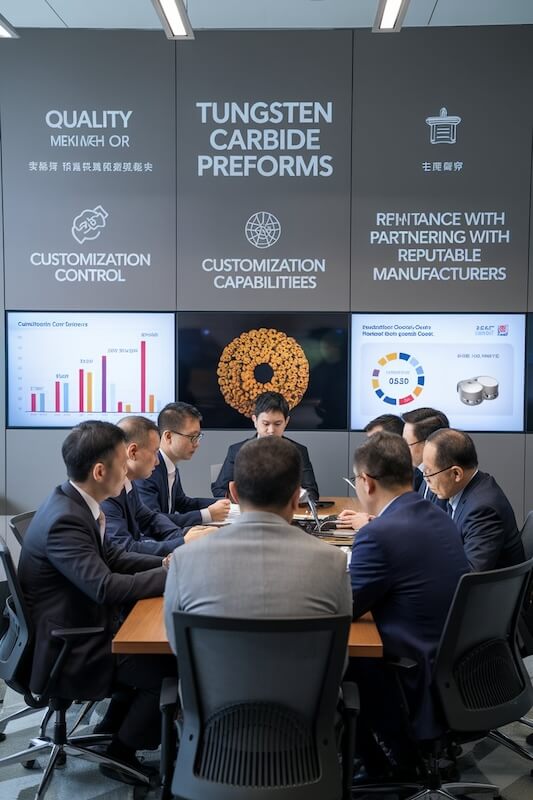
Future Trends in Tungsten Carbide Preforms
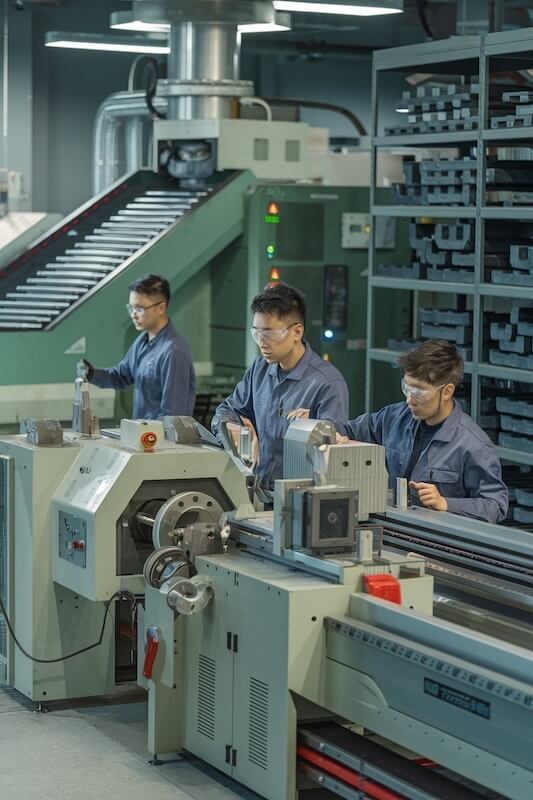
The tungsten carbide preforms industry is evolving with several emerging trends:
- Advanced Manufacturing Techniques: Adoption of technologies like additive manufacturing (3D printing) to create more complex and precise preforms.
- Material Innovations: Development of new binder materials and composites to enhance performance and expand application ranges.
- Sustainability: Increased focus on eco-friendly manufacturing processes, including recycling and reducing waste.
- Customization and Flexibility: Greater emphasis on providing highly customized solutions to meet diverse and specific industry needs.
- Automation and AI Integration: Implementation of automated systems and artificial intelligence to optimize production processes and improve quality control.
- Enhanced Surface Treatments: Innovations in surface coating and treatment to further improve wear resistance and durability.
- Global Supply Chain Optimization: Efforts to streamline supply chains for better reliability and reduced lead times amidst global challenges.
- Regulatory Compliance: Stricter adherence to international standards and regulations to ensure product safety and environmental sustainability.
Staying abreast of these trends allows manufacturers and buyers to leverage the latest advancements in tungsten carbide preform technology.
Conclusion
Tungsten carbide preforms are indispensable in the manufacturing of high-performance tools and components across various industries. Their exceptional hardness, precision, and durability make them the material of choice for applications that demand reliability and longevity.
By understanding the composition, benefits, and applications of tungsten carbide preforms, as well as knowing how to select the right manufacturer, businesses can enhance their production capabilities and achieve superior results.
As the industry continues to innovate, tungsten carbide preforms will remain at the forefront of advanced manufacturing, driving progress and efficiency in numerous sectors worldwide.
Quick and easy: Enter your specifications and get a quote in one business day