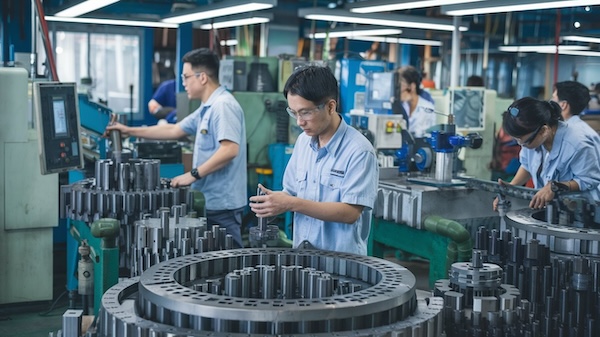
Tungsten Carbide Tooling
Retop aimed at decision-makers across various industries. Its goal is to provide a thorough understanding of tungsten carbide tooling, covering fundamental properties, practical benefits, and strategic considerations. By Retop's share, industry leaders can appreciate the full potential of tungsten carbide tooling in enhancing efficiency, quality, and long-term competitiveness.
Quick and easy: Enter your specifications and get a quote in one business day
Table of Contents
Expertise in Tungsten Carbide Tooling
Retop Carbide manufactures the highest-quality carbide tooling including carbide punches, dies and core rods. We also manufacture a variety of Tungsten Carbide Wear Parts for many industries.
Types of Tungsten Carbide Tooling
- Carbide Preforms
- Carbide Punches and Dies
- Compacting Punches and Dies
- Redraw Dies
- Core Rods
- Slitting Knives
- Draw Rings
- Draw Pads
- Carbide plugs
- Wear Parts
- Burnishing rolls
- Carbide Injection Nozzles
- Carbide Mixing Tubes
- Carbide Plungers
- Rotors
- Stators
- Erosion Sleeves
- Carbide Valve Seats
- Shaving Dies
- Poppet Tips
- Carbide Bottom Sleeves
- Spin Curl Rollers
- High Flow Rotors
- Carbide Wire Guides
- Main Valve Orifices
- Piston Rings
- Valve Tips
- Choke Nozzles
- Other
Introduction to Tungsten Carbide: A Key Material for Modern Manufacturing
Tungsten carbide has become a cornerstone in precision manufacturing due to its exceptional hardness, durability, and versatility.
Details:
- Defining Tungsten Carbide: A composite of tungsten and carbon, often bonded with cobalt or nickel binders, resulting in a material much harder than standard tool steels.
- Why It Matters: Its unique attributes tackle challenges that arise when machining abrasive metals, exotic alloys, and other hard-to-cut materials.
- Industry Adoptions: From automotive and aerospace to oil and gas, electronics, and tooling production, virtually every high-demand manufacturing sector recognizes tungsten carbide’s value.
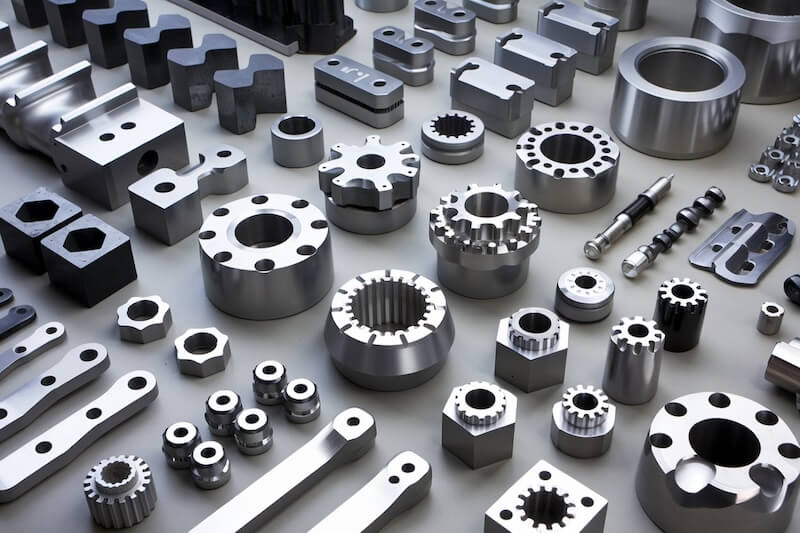
Understanding the Core Properties and Composition
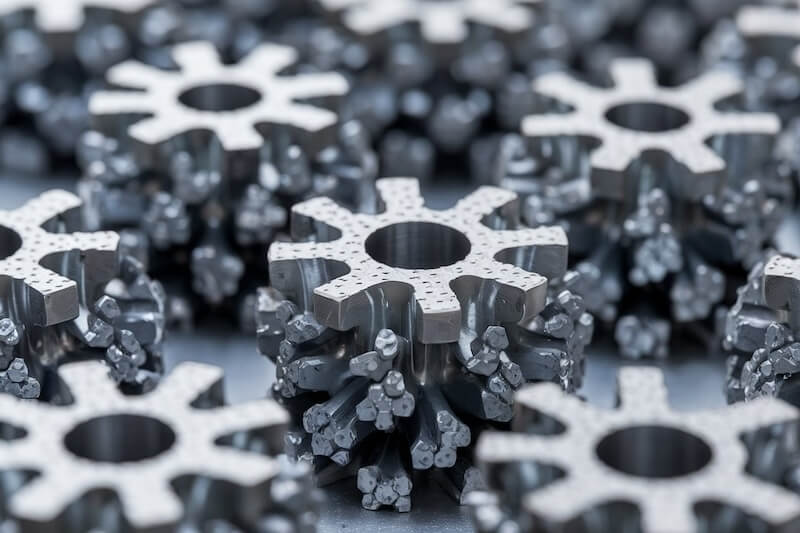
Familiarity with tungsten carbide’s material composition is crucial for selecting the right grade and achieving optimal results.
Details:
- Material Structure: Tungsten carbide’s microstructure is a network of extremely hard WC (tungsten carbide) particles embedded in a metallic binder, offering superior wear resistance and rigidity.
- Customizable Grades: By adjusting binder content and grain size, you can fine-tune properties for toughness, hardness, and resistance to thermal shock.
- Comparisons to Traditional Tools: Unlike conventional high-speed steel, tungsten carbide maintains cutting edges longer, tolerates higher temperatures, and delivers consistent precision over extended runs.
Productivity Gains and Cost Efficiency
Investing in tungsten carbide tools pays off by boosting productivity, cutting production times, and lowering overall costs.
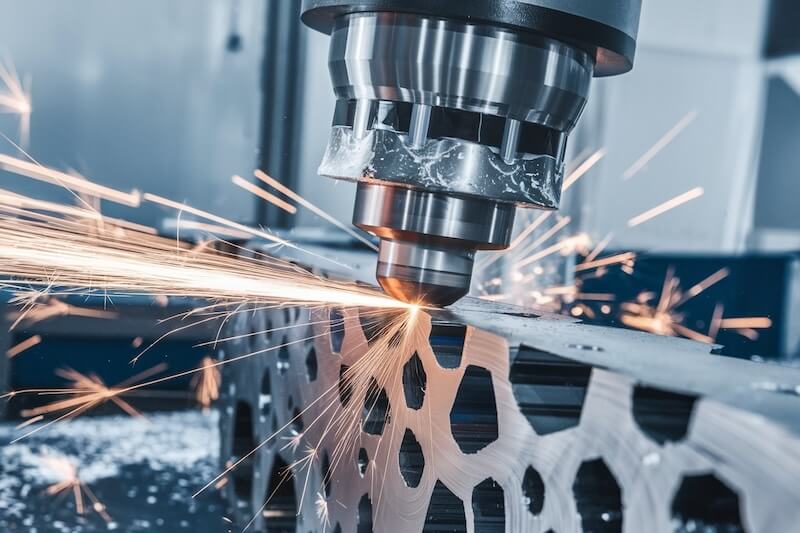
Higher Cutting Speeds
Carbide tools allow for faster machining rates, reducing cycle times and increasing throughput.
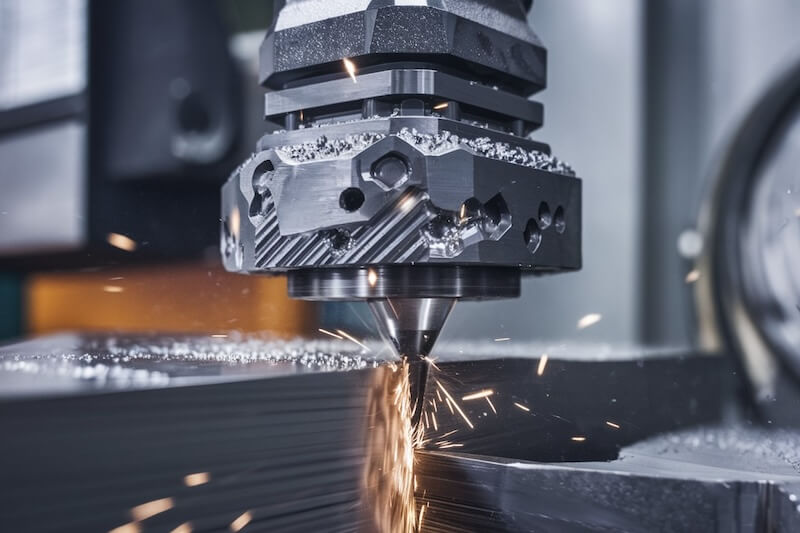
Improved Material Removal Rates
Aggressive cutting conditions become manageable, accelerating production without compromising on quality.
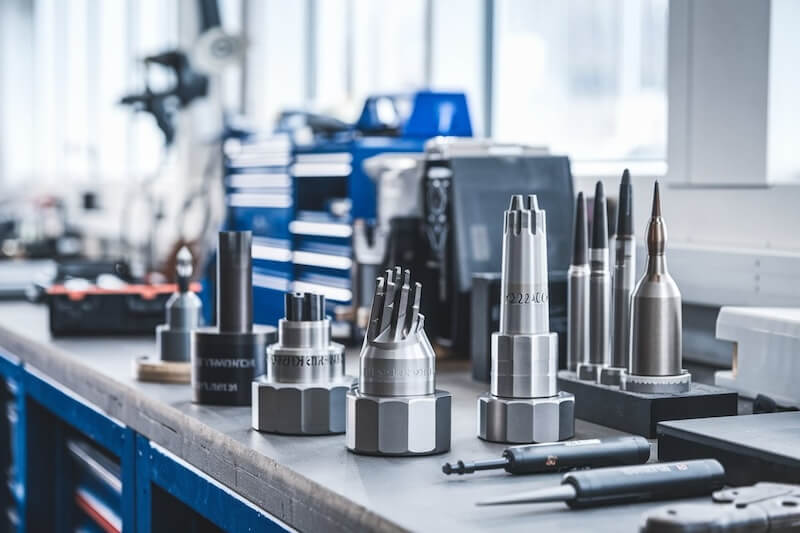
Lower Labor and Maintenance Costs
Extended tool life means fewer frequent tool changes, less downtime, and improved labor utilization on the shop floor.
Quick and easy: Enter your specifications and get a quote in one business day
Extended Tool Life and Reduced Downtime
Longevity is one of tungsten carbide’s standout attributes, leading to consistent operational stability and predictable scheduling.
Details:
- Durability Under Stress: Tungsten carbide resists wear in abrasive environments, preserving tool geometry longer than traditional materials.
- Less Frequent Replacements: Fewer replacements cut costs and ensure that machines can run steadily, avoiding sudden halts in production.
- Predictable Maintenance Cycles: Reliability in tool life planning helps manufacturers better anticipate inventory needs and optimize workflow.
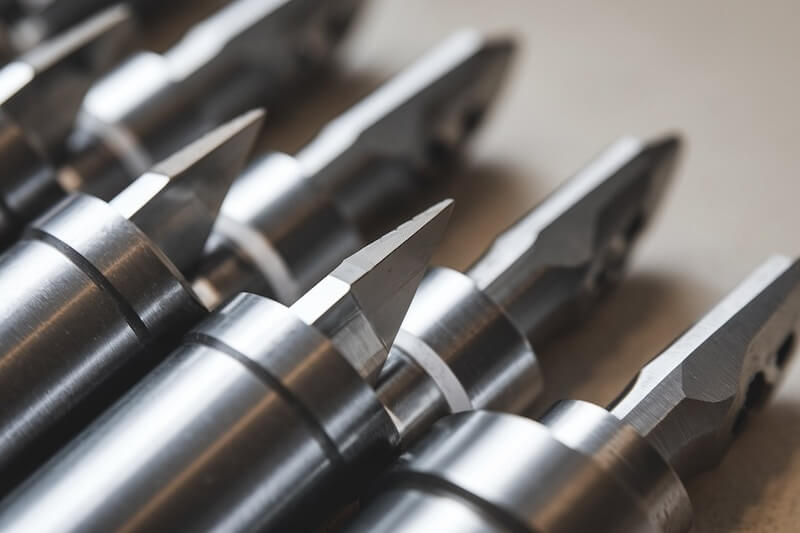
Applications Across Multiple Industries
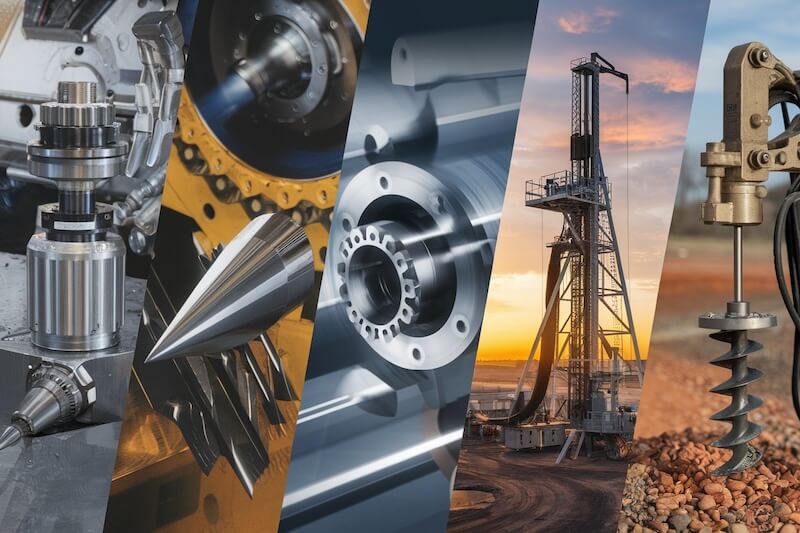
Tungsten carbide is not confined to a single sector; its adaptability unlocks benefits in a broad array of applications.
Details:
- Automotive and Aerospace: Achieving high-precision machining of engine components, turbine blades, and structural parts.
- Oil and Gas: Drilling tools and wear parts that endure extreme abrasion and high temperatures.
- Electronics and Medical Devices: Precision tooling for intricate micro-components where accuracy and surface finish are paramount.
- Mining and Construction: Heavy-duty tools that handle rock drilling, excavation, and concrete cutting with outstanding longevity and efficiency.
Achieving High Precision, Tight Tolerances, and Superior Surface Finishes
Consistent quality and precise part dimensions are critical in advanced manufacturing, and tungsten carbide excels in delivering both.
Details:
- Consistent Tolerances: Carbide tools maintain their cutting edges, ensuring tight dimensional control over long production runs.
- Superior Surface Finishes: Smooth and uniform surfaces minimize friction, enhance part performance, and reduce post-processing steps.
- Complex Geometries: Advanced CNC techniques combined with carbide tooling enable intricate shapes and design complexity without sacrificing quality.
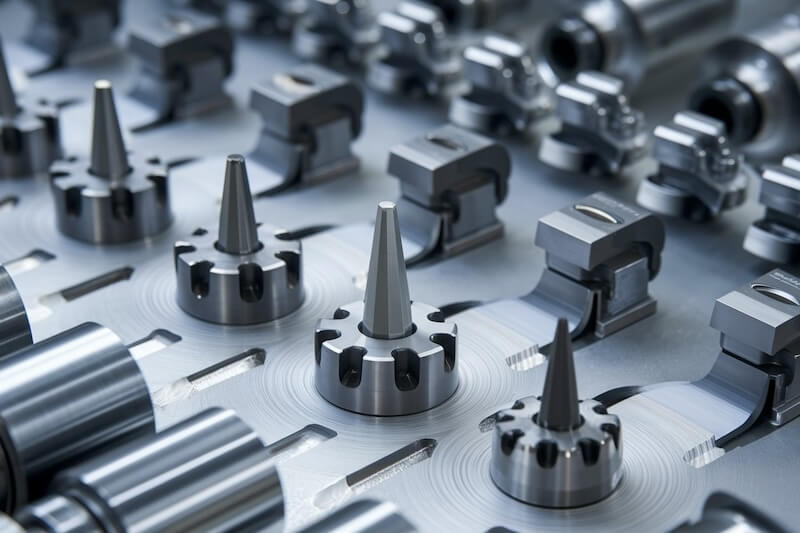
Sustainability and Environmental Benefits
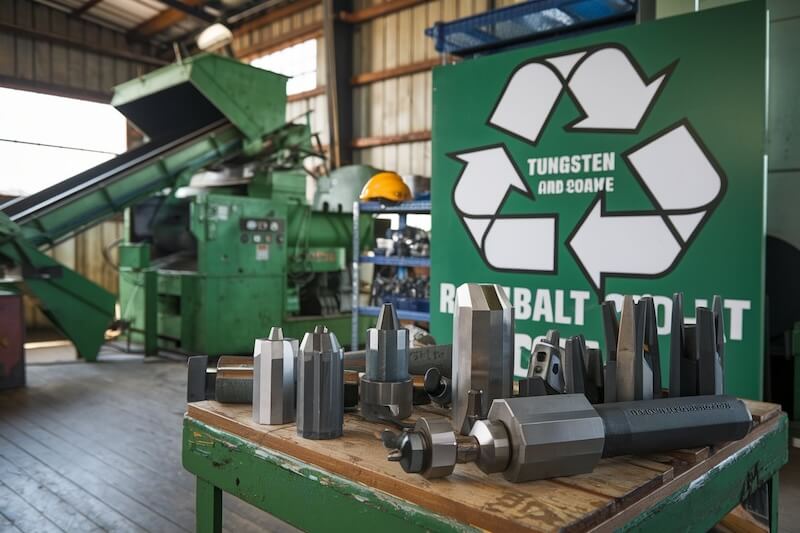
Tungsten carbide tooling supports sustainability goals by reducing material waste, energy consumption, and the overall environmental footprint.
Details:
- Longevity and Recycling: Longer tool life means fewer discarded tools, while tungsten and cobalt can be recycled, contributing to a circular economy.
- Energy Efficiency: Faster machining and fewer replacements translate to lower energy use per part, improving operational eco-friendliness.
- Less Scrap and Rework: Precise machining reduces the number of defective parts, saving materials and decreasing landfill contributions.
Partnering with a Reputable Tungsten Carbide Tool Supplier
Working with an experienced tungsten carbide tooling provider ensures you get tailored solutions, technical guidance, and ongoing support.
Details:
- Expert Consultation: Trusted suppliers help select the right carbide grade, tool geometry, and coatings to maximize productivity and part quality.
- Customized Solutions: From specialized cutting tools to wear-resistant inserts, a dependable partner can develop tools perfectly aligned with your manufacturing needs.
- After-Sales Support: Prompt service, training, and quick turnaround on regrinding or re-tipping services maintain smooth operations and build long-term value.
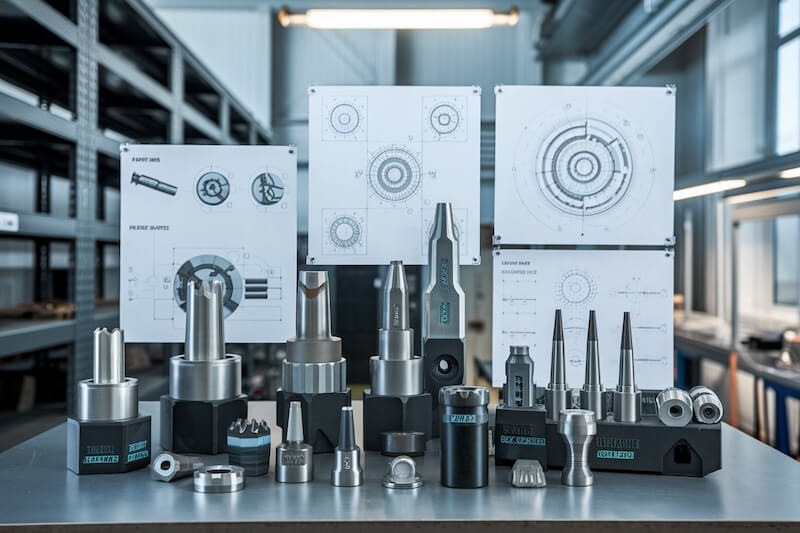
Conclusion
Tungsten carbide tooling stands as a fundamental component in modern manufacturing across multiple industries.
Its unparalleled hardness, durability, and adaptability lead to improved productivity, cost savings, sustainability, and overall product quality.
From understanding the raw material properties to implementing the right tooling strategies, decision-makers can confidently invest in tungsten carbide solutions to elevate their manufacturing capabilities. Partnering with a reputable supplier ensures that these advantages are fully realized, transforming production lines into hubs of innovation, consistency, and growth.
Quick and easy: Enter your specifications and get a quote in one business day