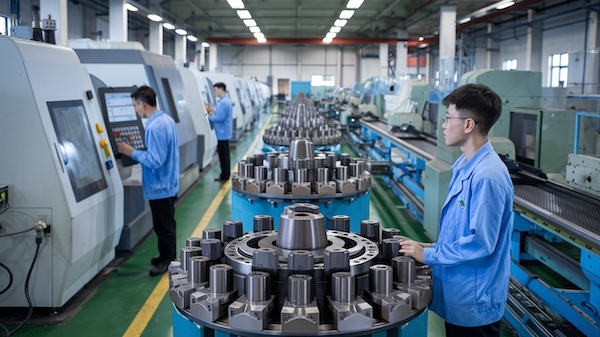
Tungsten Carbide Manufacturing Wear Parts
Retop designed to inspire confidence in tungsten carbide wear parts among machine operators across various industries. By detailing why tungsten carbide is the material of choice—offering superior durability, precision, and cost-effectiveness—we aim to reassure professionals that switching to or maintaining tungsten carbide components can significantly enhance their manufacturing processes.
Quick and easy: Enter your specifications and get a quote in one business day
Table of Contents
Expertise in Tungsten Carbide Manufacturing Wear Parts
Tungsten carbide is used in various manufacturing operations, including drills and mills, CNC lathes, vertical turret lathes, orifices, mechanical seal faces and seats, and chucks.
Types of Tungsten Carbide Manufacturing Wear Parts
- Tungsten Carbide Drill Wear Parts
- Tungsten Carbide Milling Wear Parts
- Wear Parts for CNC lathes
- Vertical Turret Lathe Wear Parts
- Tungsten Carbide Orifices
- Tungsten Carbide Mechanical Seal Faces
- Tungsten Carbide Seats
- Tungsten Carbide Chucks
The Demanding World of Modern Manufacturing Operations
As manufacturing processes become more advanced, the wear parts used in drills, mills, CNC lathes, vertical turret lathes, orifices, mechanical seals, and chucks must withstand higher loads, tighter tolerances, and harsher operating conditions.
Details:
- Rising Expectations: Today’s global marketplace demands faster production cycles, better finishes, and consistently high quality.
- Material Limitations: Traditional alloys or tool steels may not maintain their integrity over extended runs, leading to lost productivity.
- The Need for Superior Solutions: Machine operators seek robust wear parts that can handle the increasing complexities without frequent replacements.
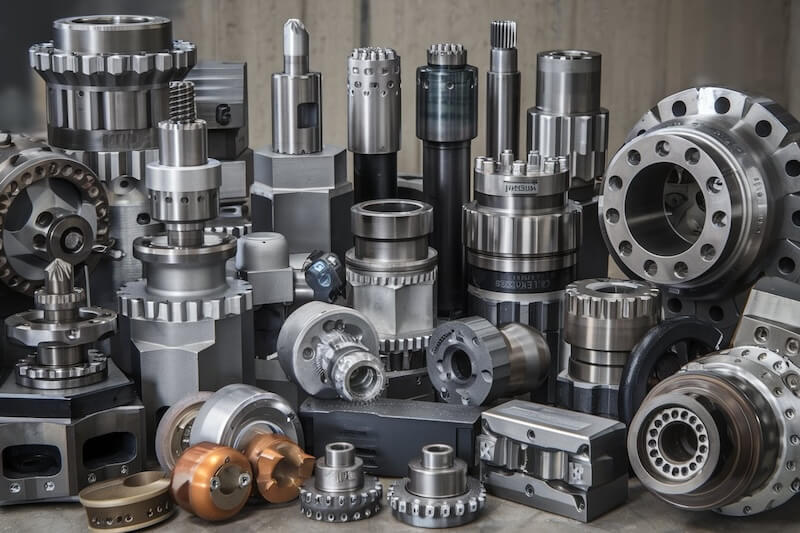
Understanding Tungsten Carbide’s Unique Composition and Properties
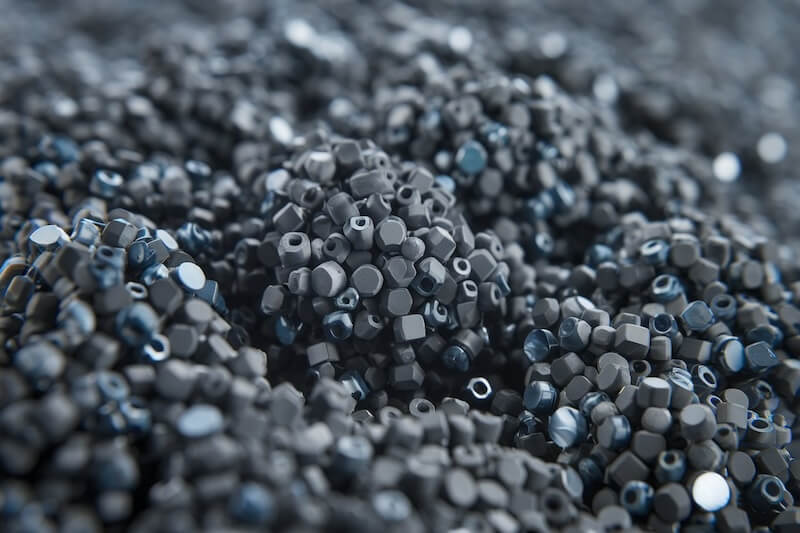
Tungsten carbide stands out due to its exceptional hardness, thermal stability, and wear resistance, all derived from its specialized composition.
Details:
- Composition: A blend of tungsten carbide particles bonded with metals like cobalt, creating a material significantly harder than standard tool steels.
- Inherent Strength: This compound structure ensures minimal deformation and excellent dimensional stability under heavy loads and high-speed operations.
- High-Temperature Performance: Tungsten carbide retains its properties even at elevated temperatures, making it ideal for demanding cutting, drilling, and sealing environments.
Extended Tool Life Means Reduced Downtime and Maintenance
One of the greatest advantages of tungsten carbide wear parts is their longevity, directly affecting operational efficiency.
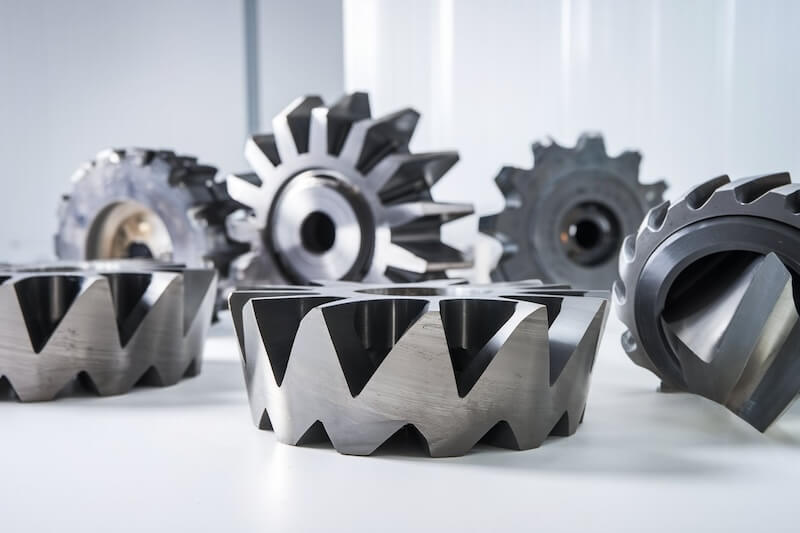
Less Frequent Replacements
Longer-lasting wear parts reduce the time spent changing tools, boosting uptime and throughput.
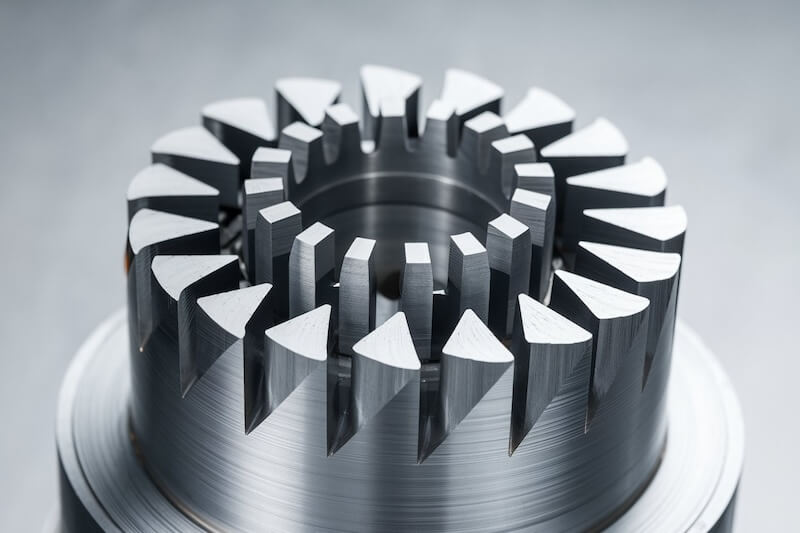
Stable Cutting Edges
Consistent tool geometry over prolonged periods maintains performance quality, minimizing adjustments.

Predictable Maintenance Schedules
Operators can plan service intervals more accurately, leading to smoother, more cost-effective production planning.
Quick and easy: Enter your specifications and get a quote in one business day
Enhanced Precision and Performance Under Stress
Tungsten carbide wear parts do more than just last longer; they enable higher precision and consistency, which is critical to meeting strict component tolerances.
Details:
- Superior Surface Finishes: Stable cutting edges and minimal tool wear result in smoother finishes on machined parts, reducing post-processing needs.
- Tight Tolerances Maintained: Less wear and deformation allow operators to maintain specified dimensions and shapes over large production runs, ensuring quality and consistency.
- Improved Process Control: Reliable tooling reduces variable factors in machining, granting operators greater control over cutting parameters and outcomes.
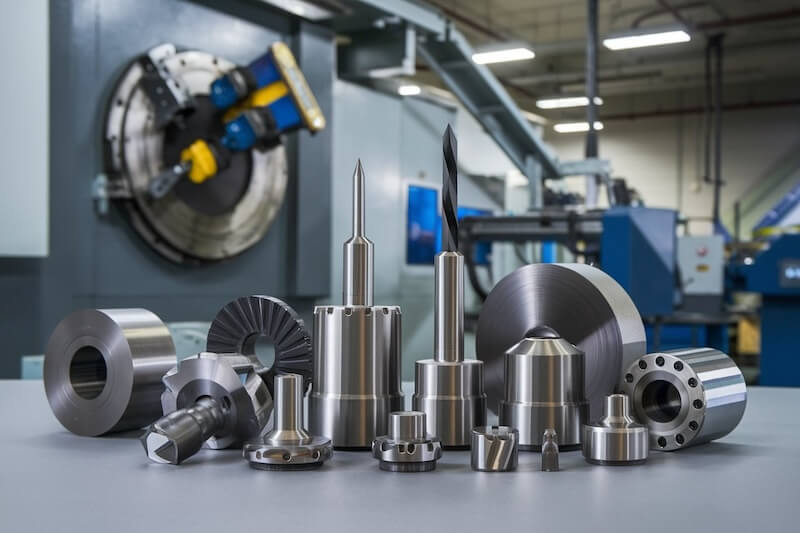
Lower Overall Costs Through Efficiency and Reliability
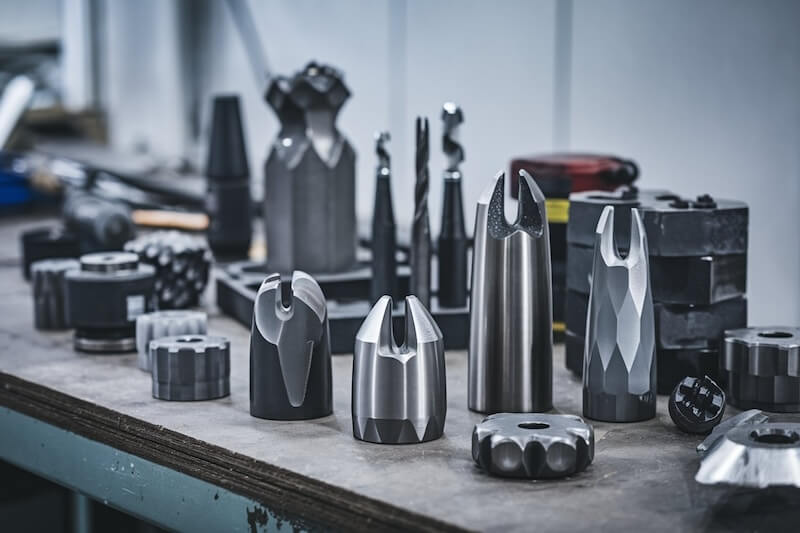
Although the initial price of tungsten carbide wear parts may be higher than standard alternatives, their long-term operational savings make them the more economical choice.
Details:
- Cost per Part: When measured over the total output rather than the sticker price of the tool, tungsten carbide often emerges as the more cost-effective solution.
- Reduced Scrap and Rework: Consistent tool performance lowers the chances of defective parts, saving on materials and labor.
- Energy Savings: Efficient cutting with razor-sharp, long-lasting tools can also lower energy consumption on the shop floor.
Versatility Across Multiple Industries and Applications
Tungsten carbide’s benefits aren’t confined to a single sector—they apply broadly, from heavy industry to precision engineering.
Details:
- Drills and Mills: In drilling and milling operations, tungsten carbide endures abrasive materials and tough alloys with minimal degradation.
- CNC Lathes and Vertical Turret Lathes: Stable, precise cutting edges deliver improved tool life and repeatability, critical for complex components.
- Orifices, Mechanical Seals, and Chucks: Wear parts made of tungsten carbide handle corrosive fluids, high pressures, and constant mechanical stress without failing prematurely.
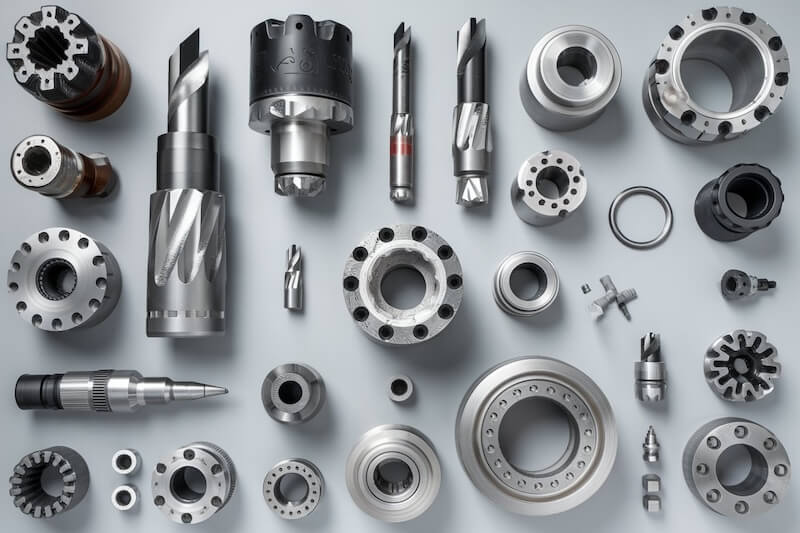
Sustainability and Environmental Benefits
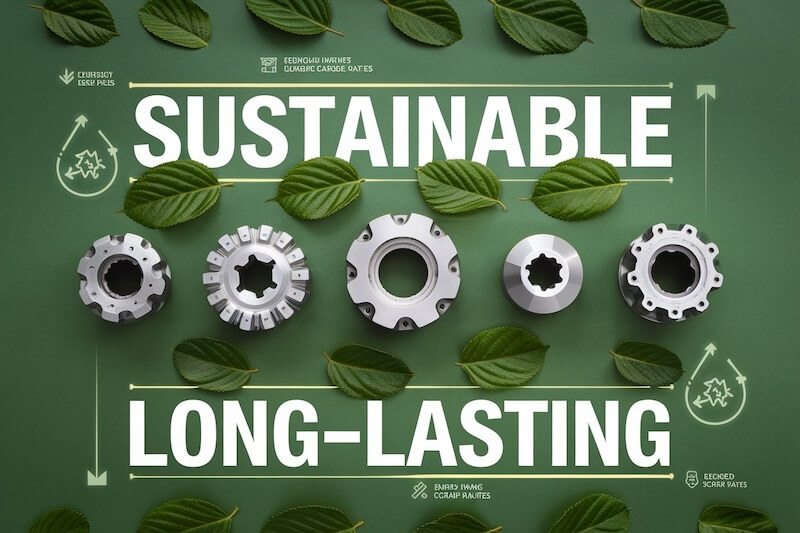
Longer-lasting tools that maintain efficiency align with sustainability goals and responsible resource usage.
Details:
- Lower Material Waste: Extended tool life means fewer tools discarded, reducing overall material consumption.
- Reduced Energy and Resource Use: Efficient machining and fewer defective parts can lower total energy usage and resource inputs.
- Compliance with Regulations: As environmental standards tighten, investing in durable, reliable materials helps companies stay ahead of regulatory requirements.
Choosing Tungsten Carbide: A Strategic Investment for the Future
Embracing tungsten carbide wear parts is about more than just solving immediate issues—it’s about future-proofing operations against evolving market demands.
Details:
- Ongoing Innovation: Tungsten carbide tool technology continues to advance, offering even better performance as manufacturing challenges grow.
- Partnership with Trusted Suppliers: By working with reliable providers who understand your specific applications, you can tailor tungsten carbide solutions for optimal results.
- Long-Term Competitive Edge: Companies that adopt tungsten carbide wear parts can deliver higher quality products at lower costs, ultimately reinforcing their market position.
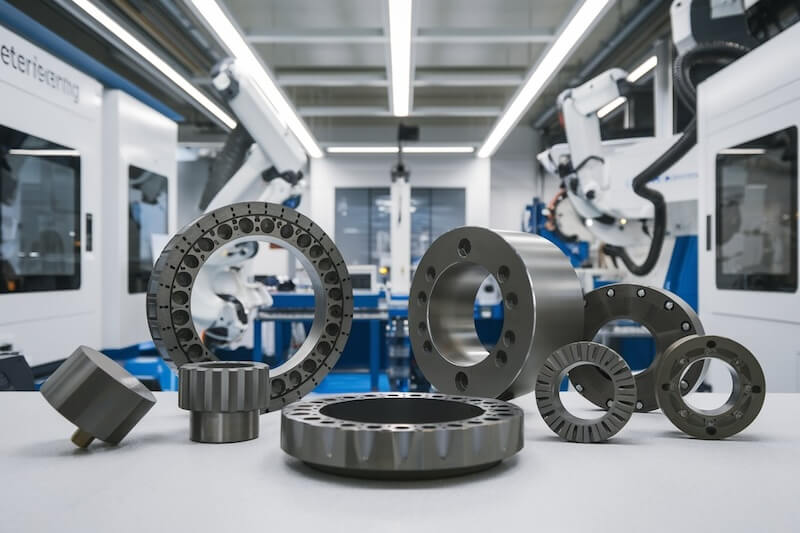
Conclusion
For machine operators across diverse industries—be it drilling, milling, CNC turning, sealing, or holding parts in place—tungsten carbide wear parts represent a strategic upgrade.
Their exceptional hardness, stability, longevity, and versatility translate into improved output, better quality, and lower overall costs.
Investing in tungsten carbide is not merely a response to today’s manufacturing challenges; it’s a proactive step towards achieving sustained operational excellence, ensuring that as demands increase, your production line remains efficient, reliable, and ready for the future.
Quick and easy: Enter your specifications and get a quote in one business day