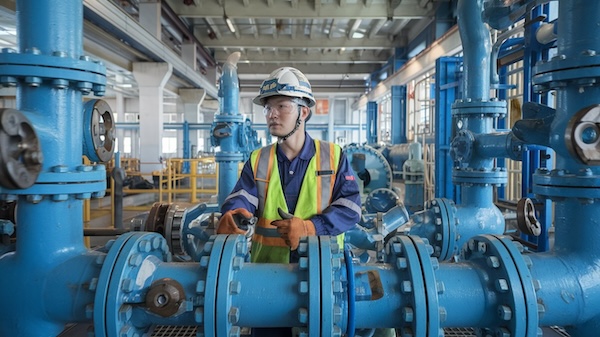
Oil and Natural Gas Wear Parts
Retop Carbide designed to provide a comprehensive understanding of tungsten carbide wear parts in the oil and natural gas industry. This piece targets both equipment operators and decision-makers, showing them the full value of investing in tungsten carbide solutions. By exploring the various applications, comparing tungsten carbide to other materials, and detailing the advantages it brings, Retop aims to equip industry professionals with the knowledge they need to make informed, strategic decisions.
Quick and easy: Enter your specifications and get a quote in one business day
Table of Contents
Expertise in Oil and Natural Gas Wear Parts Tooling
Retop Carbide produces top-quality tungsten carbide, ceramic, and tool steel wear parts, M.W.D. components, and specialized components designed for corrosive and abrasive conditions in the oil and natural gas industries.
Types of M.W.D. Components
- Mud Deflectors
- Valve Seats and Stems
- Choke Stems
- Rotors and Stators
- Erosion Sleeves – Bushings
- Flow Restrictor Bearings
- Main Pulser Components
- Solid Carbide or Two-Piece Threaded Nozzles
- Orifices – In Stock
- Poppets
- Valve Spools and Components
- Seal Rings
- Ported Flow Cages
- Carbide Cages
- Carbide Injection Nozzels
- Carbide Mixing Tubes
- Thrust Bearings
- Carbide Valve Sleeves
- Hydraulic Choke Trim
- Rotary Valve Bodies
- Stationary Valve Bodies
- Carbide Bottom Sleeves
- Main Valve Orifices
- Piston Rings
Types of High Pressure Components
- Solid Carbide Plungers
- Nozzles
- Seats and Stems
- Valve Tips
- Choke Nozzels
Types of Choke and Trim Components
- Flow Control Components
- Gates and Seats
- Bushings
Types of Drilling Components
- Stratapax Cutters
- Bit Nozzels
- Mud Nozzles
- Cutting Bits
- Mud Motor Bearings
Introduction: Meeting the Challenges of the Oil and Natural Gas Industry
The oil and natural gas sector demands highly reliable, durable, and efficient equipment to manage extreme conditions—high pressures, corrosive fluids, abrasive particles, and remote operational environments. Standard materials often struggle to maintain performance, driving the need for advanced wear parts like those made from tungsten carbide.
Details:
- Higher Operational Strain: Continuous drilling, pumping, and processing subject tools to intense mechanical stress.
- Global Competition: Companies face pressure to extract resources faster, more sustainably, and cost-effectively.
- Strategic Focus on Quality: Investing in superior wear parts ensures consistent uptime, improved safety, and better bottom-line results.
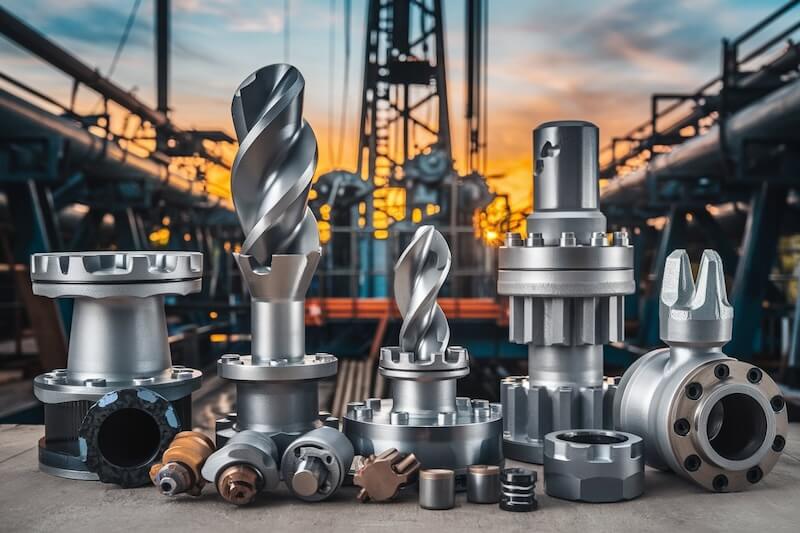
Understanding Tungsten Carbide: Composition and Key Properties
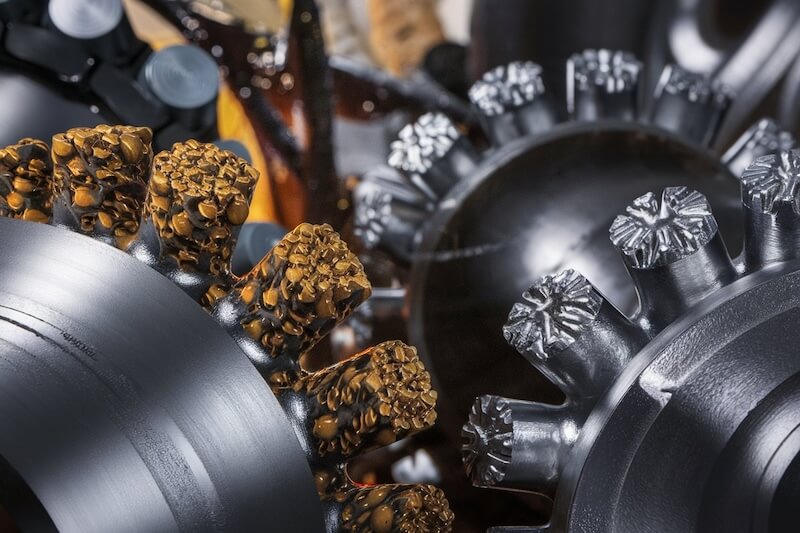
Tungsten carbide’s unique material composition endows it with properties that surpass conventional alloys or ceramic coatings used in oil and gas operations.
Details:
- Material Structure: A blend of tungsten carbide particles bonded by a metal binder (often cobalt), creating an extraordinarily hard composite.
- Hardness and Wear Resistance: Tungsten carbide ranks near diamond on the hardness scale, resisting abrasion even in slurry-laden fluids.
- Thermal and Chemical Stability: Maintains structural integrity under high temperatures and corrosive substances common in drilling muds, fracturing fluids, and production streams.
Types of Tungsten Carbide Wear Parts for Oil and Gas Applications
Tungsten carbide wear parts appear across the entire oil and natural gas value chain—from drilling to refining—improving performance and longevity.
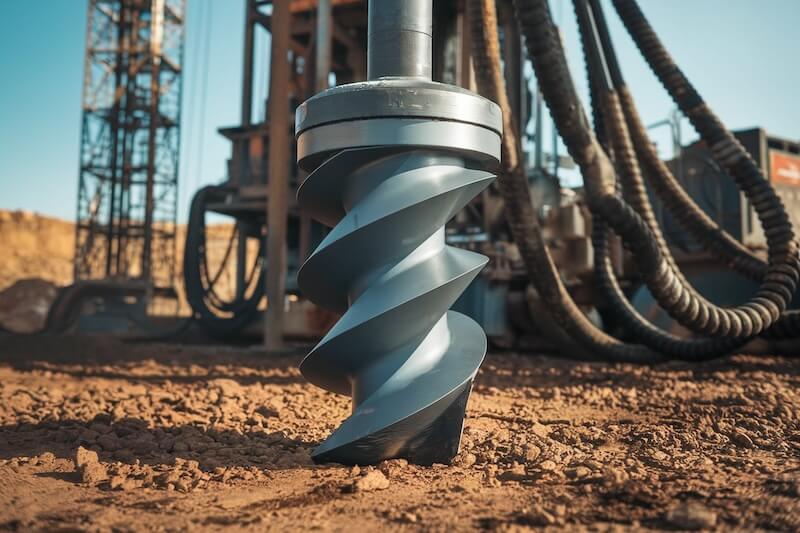
Drill Bits and Stabilizers
Carbide inserts enhance penetration rates, reduce bit wear, and prolong drilling campaigns.
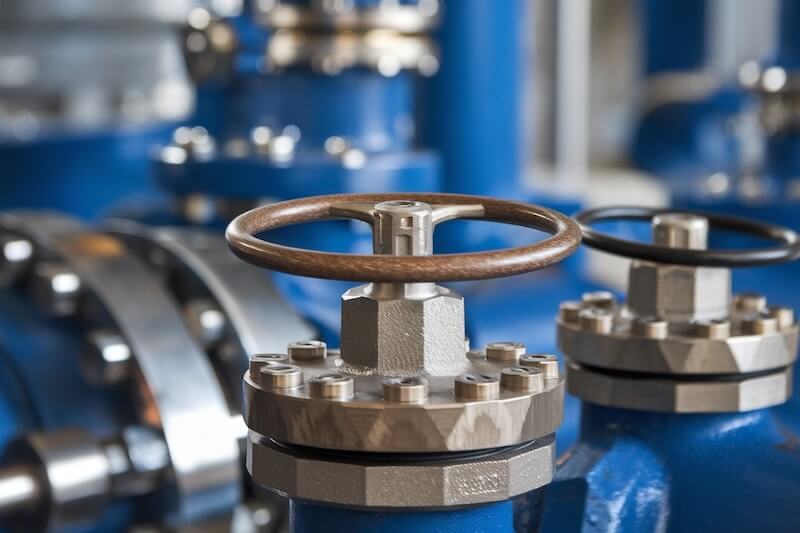
Valve Trim and Seats
In high-pressure or abrasive-flow applications, tungsten carbide seats and trims resist erosion, ensuring valve precision and extending service intervals.
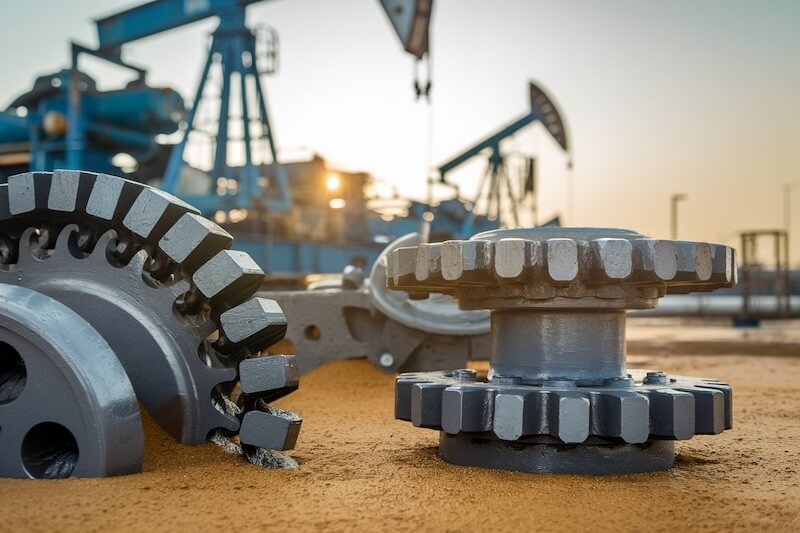
Pump Impellers and Rotors
Carbide-coated impellers mitigate damage from sand-laden fluids, increasing pump reliability.
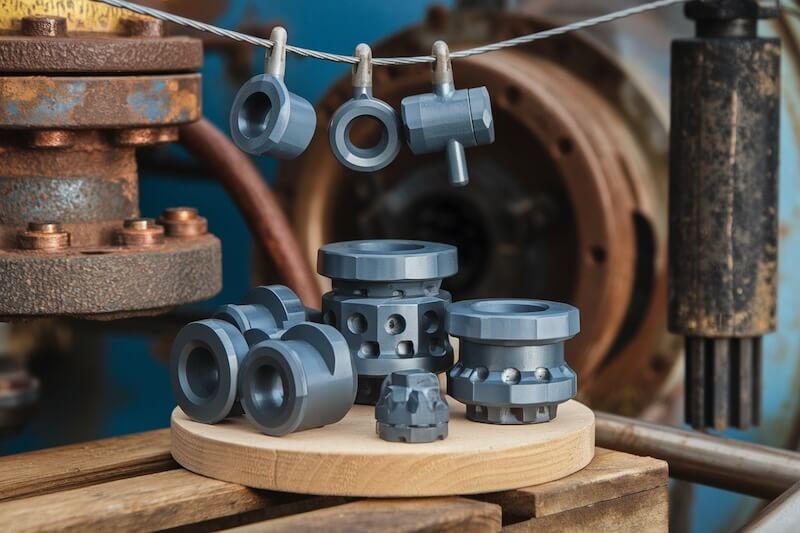
Flow Restrictors, Choke Beans, and Nozzles
Carbide elements regulate flow with minimal wear, improving precision and equipment life in downhole tools and surface equipment.
Quick and easy: Enter your specifications and get a quote in one business day
Comparing Tungsten Carbide to Other Materials
While alternatives like tool steel, ceramics, or specialty alloys have their place, tungsten carbide often outperforms them in critical oil and gas conditions.
Details:
- Versus High-Speed Steel: Tungsten carbide is harder and more wear-resistant, resulting in fewer tool changes and lower downtime.
- Versus Ceramics: Ceramics can be brittle, leading to catastrophic failures, while tungsten carbide offers a balance of hardness and toughness.
- Versus Specialty Alloys (e.g., Inconel): Although alloys offer corrosion resistance, tungsten carbide often provides better abrasion resistance, crucial in abrasive-laden wells and pipelines.
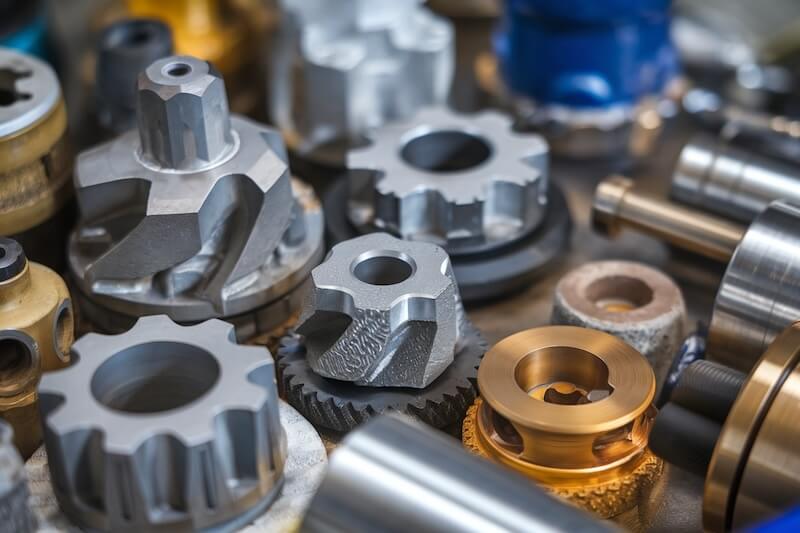
Operational Advantages: Boosting Efficiency and Reducing Costs
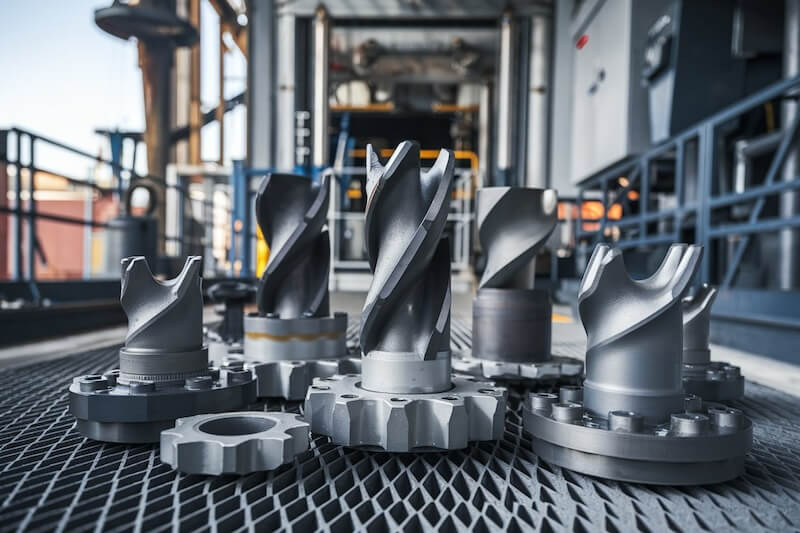
Upgrading to tungsten carbide wear parts delivers tangible improvements in productivity, maintenance schedules, and overall operational efficiency.
Details:
- Extended Tool Life: Longer service intervals reduce the frequency of shutdowns for part replacements, enhancing uptime.
- Consistent Performance: Stable tool geometry leads to predictable drilling rates, flow control, and processing throughput.
- Reduced Maintenance and Labor: Less frequent component changes lower labor costs, spare part inventories, and logistical complexities.
Enhancing Safety and Reliability in the Field
Tools that resist wear and maintain integrity under extreme conditions help create safer working environments, protecting both personnel and equipment.
Details:
- Lower Failure Rates: Reliable tungsten carbide parts reduce the risk of sudden, dangerous equipment failures.
- Precision Under Pressure: Steady tool performance aids operators in controlling well pressure and flow, preventing accidents like blowouts.
- Compliance with Regulations: As safety and environmental standards tighten, adopting durable, high-performance wear parts ensures ongoing compliance.
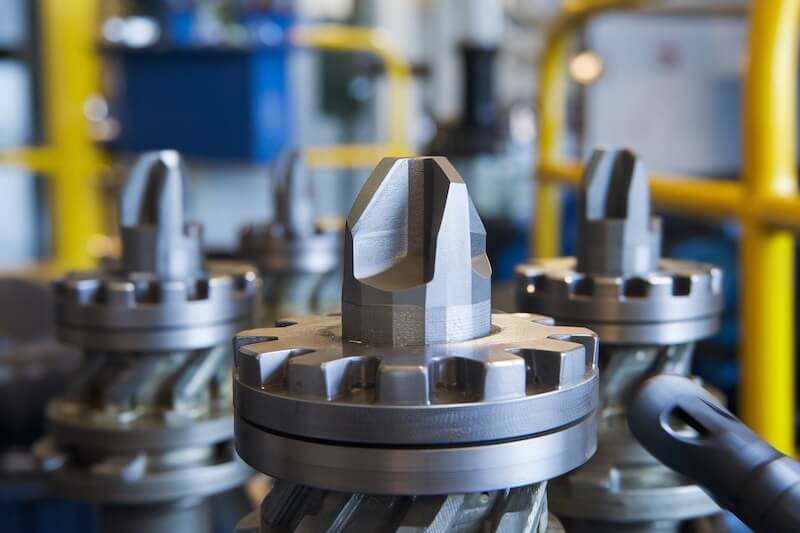
Sustainability and Environmental Responsibility
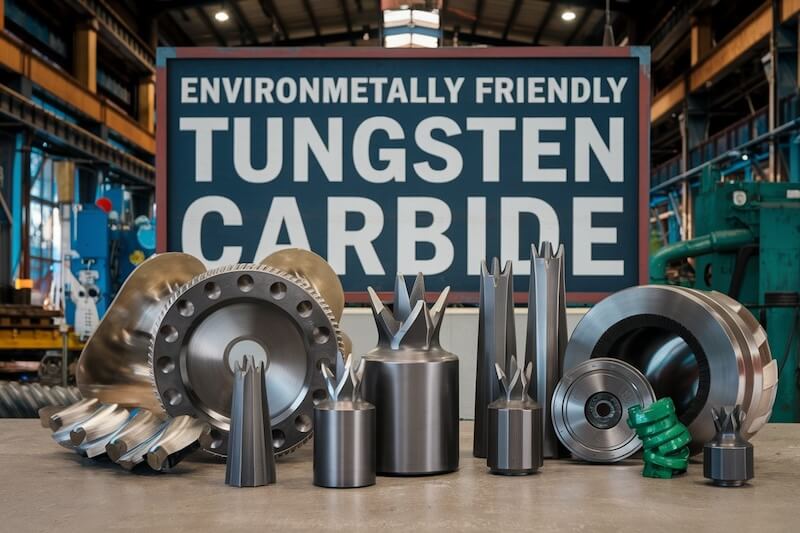
Durable tungsten carbide components help oil and natural gas companies meet sustainability goals by reducing waste, energy consumption, and environmental impact.
Details:
- Longer Service Life, Less Waste: Fewer worn-out tools mean less material ending up in landfills.
- Efficient Operations: Stable cutting and flow control can improve energy efficiency, reducing carbon footprints.
- Resource Conservation: Extending component life curtails the need for frequent raw material procurement, aligning with environmental stewardship and corporate responsibility.
Making the Informed Choice: Investing in Tungsten Carbide Wear Parts
Understanding the properties and benefits of tungsten carbide empowers industry leaders and equipment operators to choose the best wear parts for their operations.
Details:
- Strategic Partnerships: Collaborate with reputable suppliers who can tailor tungsten carbide grades and geometries to specific equipment and processes.
- Long-Term Value: While initial costs may be higher, the ROI manifests through lower downtime, improved throughput, and longer component life.
- Future-Ready Operations: As industry demands evolve—deeper wells, harsher environments—tungsten carbide remains a proven and adaptable material solution.
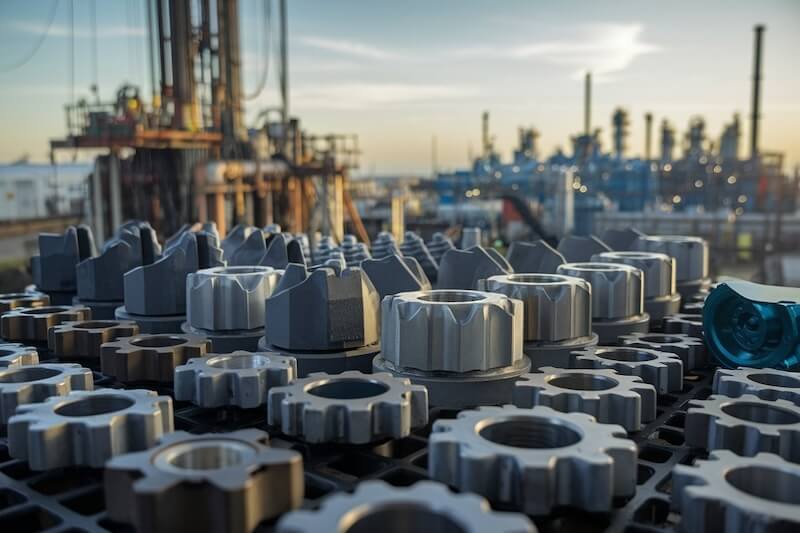
Conclusion
From drill bits and valve trims to pump components and flow restrictors, tungsten carbide wear parts stand as a cornerstone of efficiency, reliability, and sustainability in the oil and natural gas industry.
By understanding their composition, comparing them to alternative materials, and recognizing the operational and long-term advantages, decision-makers can confidently invest in solutions that drive productivity, reduce costs, and ensure safety.
Tungsten carbide wear parts ultimately position companies for success amid the evolving challenges of the energy sector—laying a foundation for stronger, more resilient operations today and in the future.
Quick and easy: Enter your specifications and get a quote in one business day