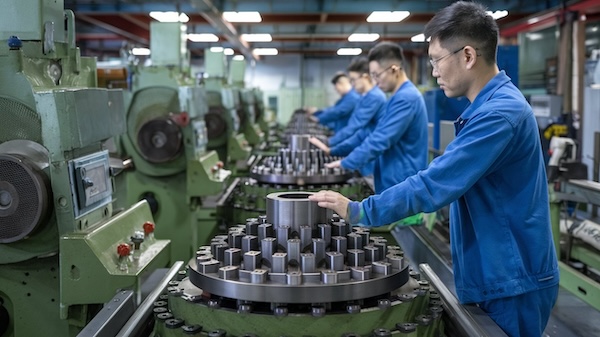
Carbide Powdered Metal Tooling
Retop designed to give powdered metallurgy tooling manufacturers a comprehensive overview of why tungsten carbide is an ideal choice. By detailing the benefits and comparing it to alternative materials, we aim to build confidence in the decision to adopt tungsten carbide tooling for improved efficiency, quality, and cost-effectiveness in powdered metallurgy processes.
Quick and easy: Enter your specifications and get a quote in one business day
Table of Contents
Expertise in Carbide Powdered Metal Tooling
Retop Carbide manufactures precision powdered metal tooling, including ammunition compacting dies, for the powdered metals industry using only the finest grade materials.
Types of Carbide Powdered Metal Tooling
- Compacting Dies and Punches
- Carbide Punches and Dies
- Powdered Metal Compacting Dies
- Compacting Core Rods
- Ammunition Compacting Dies
- Other Powdered Metal Tooling
Introduction: Meeting the Growing Demands of Powdered Metallurgy
Modern powdered metallurgy (PM) processes face heightened expectations. As industries push for components with finer tolerances, increased complexity, and enhanced mechanical properties, tooling must evolve to keep pace. Traditional tool materials often fall short under these intense conditions. Tungsten carbide has emerged as a solution that aligns with the rising quality and productivity standards in PM manufacturing.
Details:
- Industry Pressures: Growing demand for precision parts in automotive, aerospace, and medical sectors.
- Stricter Tolerances: Complex geometries and delicate features require tools capable of maintaining accuracy over extended runs.
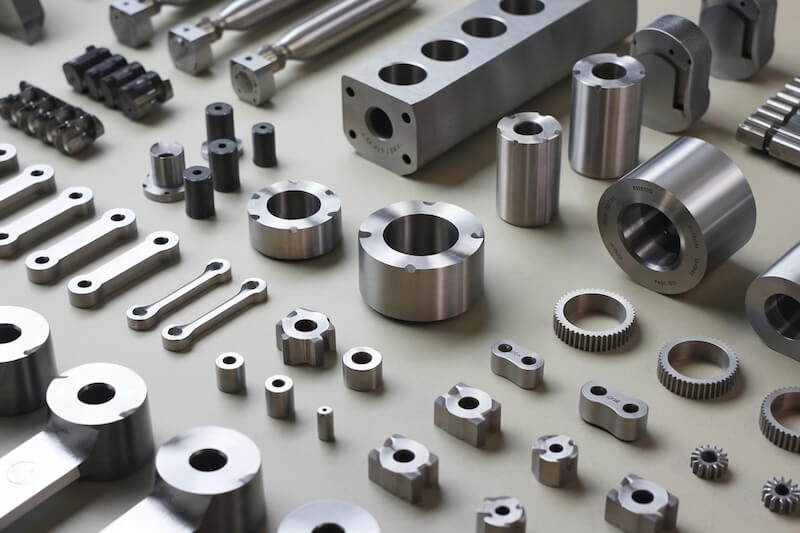
Understanding Tungsten Carbide: Composition and Core Properties
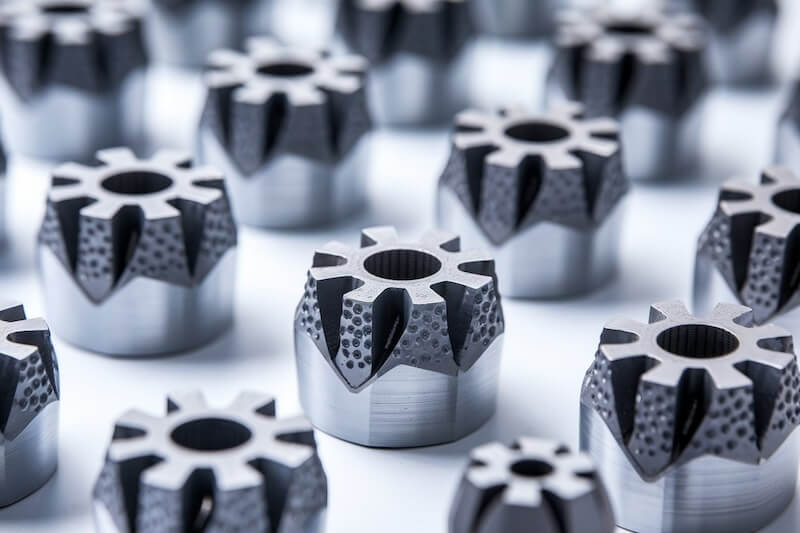
Tungsten carbide’s unique blend of tungsten carbide particles and metallic binders, often cobalt, creates a composite material significantly tougher and harder than conventional steels.
Details:
- Hardness and Toughness: Near-diamond hardness prevents rapid wear, while balanced toughness resists fracturing.
- Thermal Stability: Maintains structural integrity under high pressures and temperatures commonly encountered in PM compaction and sintering processes.
- Dimensional Stability: With minimal deformation, tungsten carbide tooling ensures consistent part sizes and shapes.
Comparing Tungsten Carbide with Other Tooling Materials
While traditional steels, high-speed steels (HSS), or tool steels have been industry mainstays, tungsten carbide frequently surpasses them on critical performance metrics.
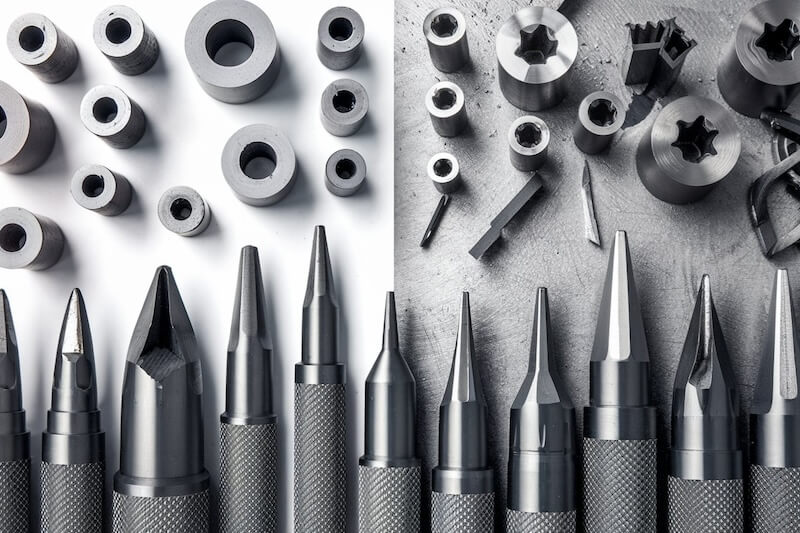
Longer Wear Life vs. Steel
Tungsten carbide’s extreme hardness outlasts steel tools, reducing the frequency of costly replacements.
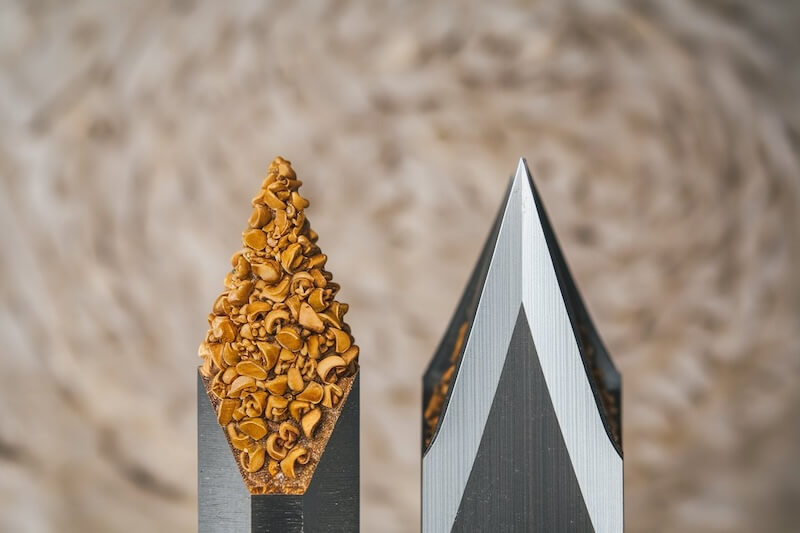
Improved Edge Retention vs. HSS
Carbide maintains a sharper cutting edge for longer, promoting better part definition and surface finish.
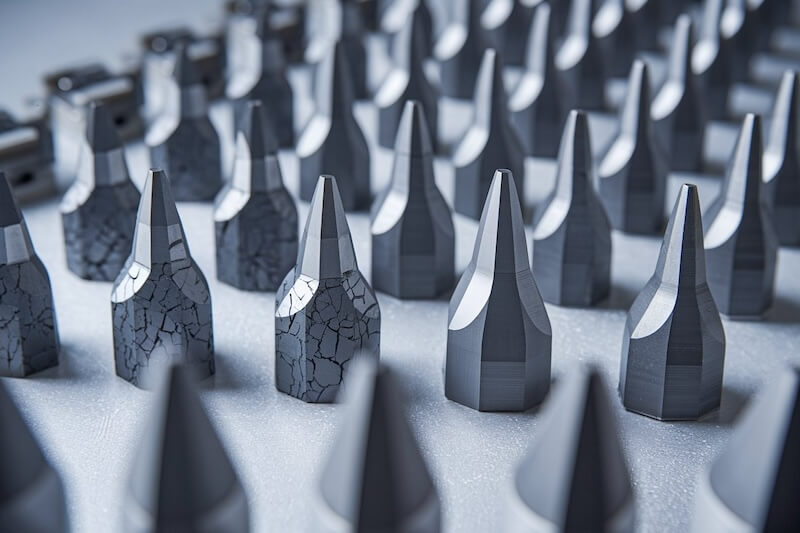
Resistance to Microcracks vs. Ceramics
Unlike certain ceramics that can be brittle, tungsten carbide balances hardness with toughness, reducing sudden tool failures.
Quick and easy: Enter your specifications and get a quote in one business day
Extended Tool Life and Reduced Downtime
By resisting wear and maintaining tool geometry, tungsten carbide significantly lowers the frequency of tool changes, maintenance interventions, and production interruptions.
Details:
- Stable Production Cycles: Reduced tool wear means fewer unscheduled stoppages, boosting throughput and meeting delivery timelines.
- Predictable Maintenance Schedules: Operators can plan part runs and maintenance windows with greater accuracy, improving overall operational efficiency.
- Inventory Management: Longer-lasting tools simplify inventory planning, lowering storage costs and simplifying logistics.
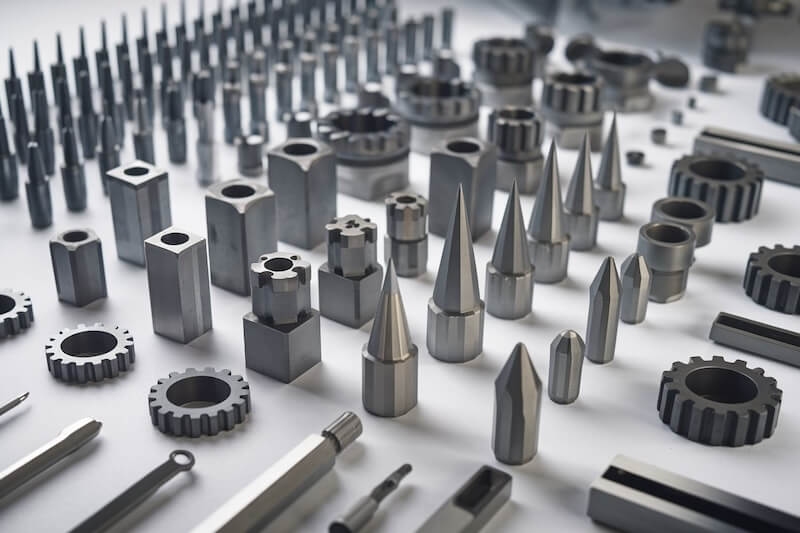
Enhanced Precision and Component Quality
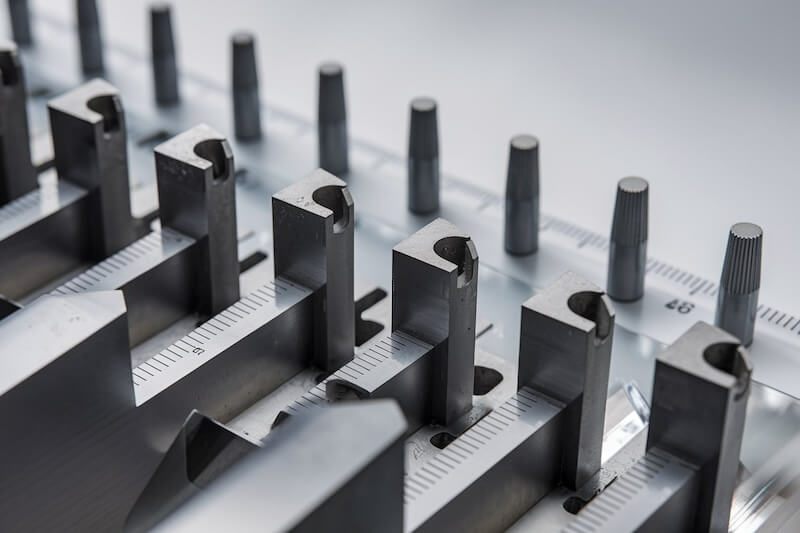
Tungsten carbide’s dimensional stability and durability contribute directly to better part-to-part consistency, tighter tolerances, and improved final product quality.
Details:
- Consistent Compaction: Carbide tooling ensures uniform pressure distribution, critical for achieving optimal density and mechanical properties in PM components.
- Surface Finish Improvements: Cleaner, more precise edges result in smoother part surfaces and reduced post-processing requirements.
- Lower Defect Rates: Reliability in tooling geometry reduces scrap, rework, and variance in part dimensions, enhancing yield rates.
Operational Cost Savings and Long-Term ROI
Although the initial cost of tungsten carbide tooling may be higher than conventional alternatives, the long-term financial benefits are substantial.
Details:
- Reduced Replacement Frequency: Fewer purchases over the tool’s lifespan slash overall tooling expenses.
- Less Labor for Tool Changes: Minimizing downtime and manual intervention lowers labor costs and maximizes productivity.
- Energy Efficiency: Stable tooling often correlates with smoother machine operations, reducing energy consumption and environmental impact.
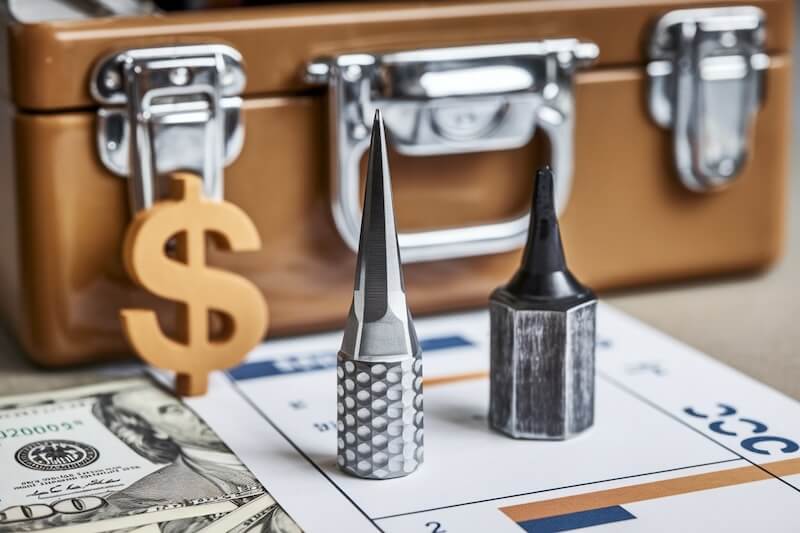
Future-Proofing Against Industry Evolution
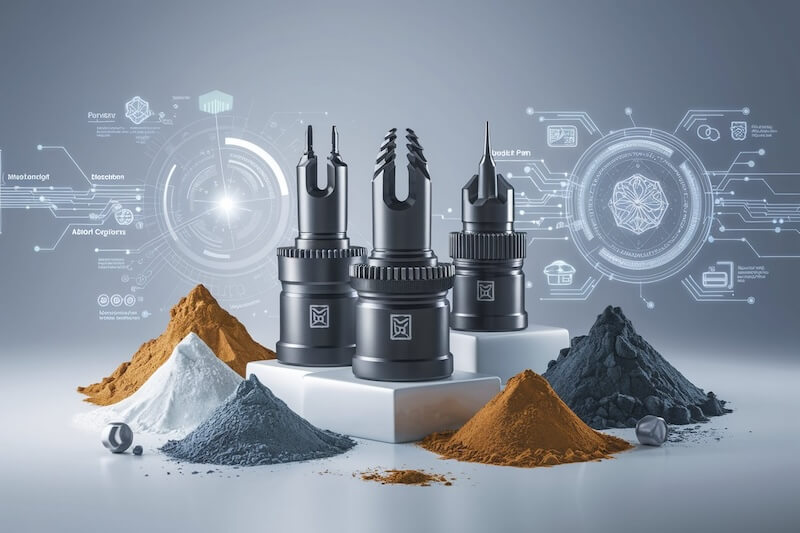
As powdered metallurgy continues advancing toward more complex parts, innovative materials, and tighter specifications, tungsten carbide tooling remains a forward-looking choice.
Details:
- Adapting to New Powders: Tungsten carbide tools handle emerging powder formulations, from tough alloys to specialized composites, without compromising performance.
- Emerging Markets and Technologies: As additive manufacturing and hybrid PM processes expand, carbide’s adaptability ensures ongoing relevance.
- Global Competitiveness: Companies investing in tungsten carbide solutions position themselves as market leaders capable of meeting future challenges.
Partnering with Reliable Suppliers and Tailoring Solutions
Maximizing tungsten carbide’s benefits depends on working with reputable suppliers who can customize tooling solutions to specific PM applications.
Details:
- Customized Grades and Geometries: Expert suppliers can fine-tune carbide compositions, tool shapes, and coatings to match unique powder characteristics and process parameters.
- Ongoing Support and Training: Technical assistance and reconditioning services ensure that manufacturers extract the full value from their investment.
- Strategic Alliances: Building a long-term relationship with a knowledgeable supplier guarantees consistent tool quality, improved lead times, and stable operational performance.
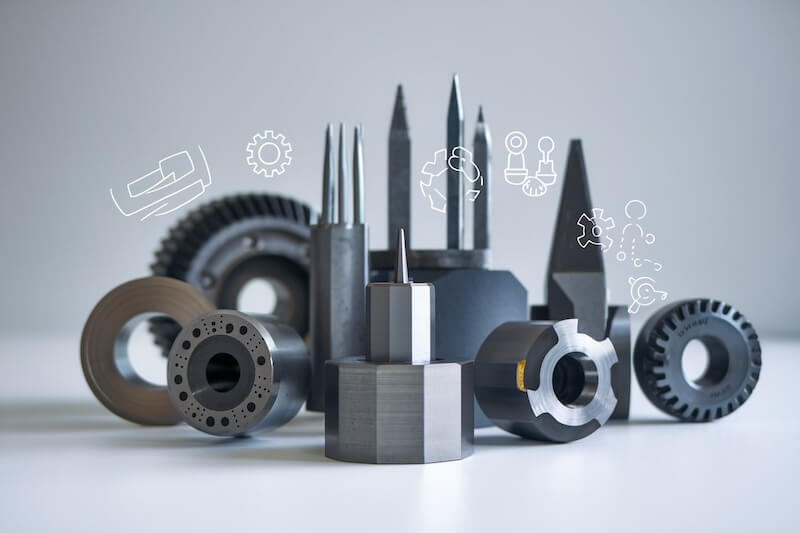
Conclusion
The journey from powdered metals to high-performance components is challenging, and the tools used in the process are pivotal to success.
Tungsten carbide excels as a PM tooling material thanks to its exceptional hardness, wear resistance, dimensional stability, and adaptability to evolving industry demands.
By outlasting traditional materials, reducing downtime, and improving part quality, tungsten carbide delivers significant long-term advantages. Making the switch to tungsten carbide tooling is not just a tactical move—it’s a strategic investment in efficiency, product quality, and future competitiveness.
Quick and easy: Enter your specifications and get a quote in one business day