
Metal Machining (CNC/Lathe/Mill)
Retop Carbide is aiming to provide a comprehensive understanding of tungsten carbide wear parts for decision-makers in the Metal Machining (CNC/Lathe/Mill) industry. By exploring the basics of tungsten carbide, comparing it to alternative materials, and illustrating the strategic benefits it offers, Retop helps industry leaders make informed decisions that drive efficiency, quality, and long-term profitability.
Quick and easy: Enter your specifications and get a quote in one business day
Table of Contents
Expertise in Carbide Metal Machining (CNC/Lathe/Mill) Tooling
Retop Carbide’ specialty metal machining tooling is trusted and used by the manufacturing leaders in the industry.
Types of Carbide Metal Machining (CNC/Lathe/Mill) Tooling
- Cutting inserts
- End mills and drills
- Boring bars and turning tools
- Tool holders and bushings
- Concrete drill bits
- Masonry cutting tools
- Pavement milling teeth
- Others
Introduction: The Evolving Demands of Metal Machining
As the Metal Machining industry advances, manufacturers must meet tighter tolerances, machine harder materials, and achieve faster turnaround times. Traditional wear parts often struggle under these pressures, leading to frequent tool changes, longer downtime, and compromised product quality. Tungsten carbide wear parts have emerged as a superior alternative, helping companies stay competitive and meet the industry’s escalating demands.
Details:
- Increasing Complexity: Complex geometries and precision machining require more robust tooling solutions.
- Shorter Lead Times: The pressure for faster delivery schedules demands durable wear parts that minimize stoppages.
- Market Competition: Companies must adopt cutting-edge materials, like tungsten carbide, to maintain a competitive edge.
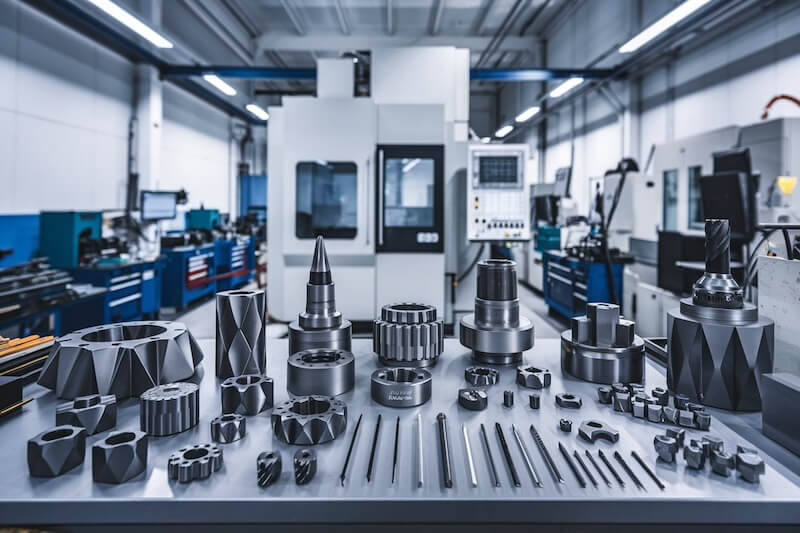
Understanding Tungsten Carbide: Composition and Core Properties
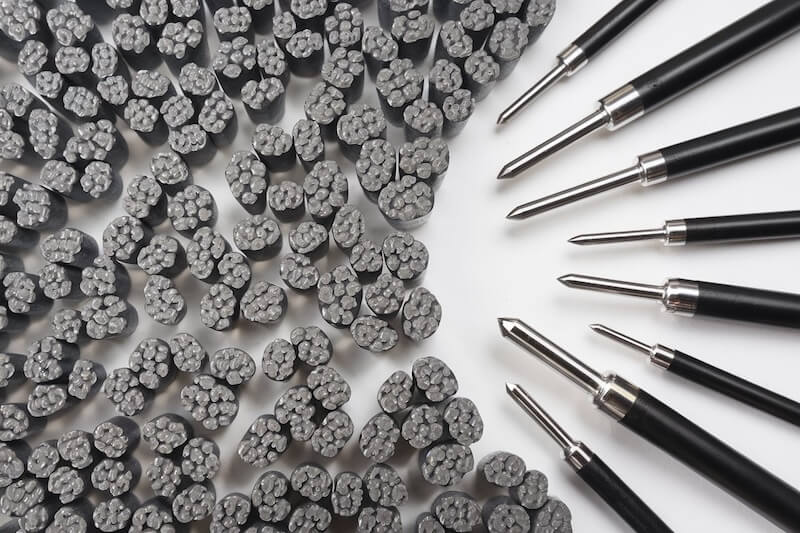
Tungsten carbide is not an ordinary metal; it is a hard, wear-resistant composite made by combining tungsten carbide powder with a metal binder, typically cobalt. This unique composition results in exceptional hardness, rigidity, and thermal stability. For CNC, lathe, and milling applications, tungsten carbide wear parts ensure prolonged tool life, consistent dimensional accuracy, and reliable performance under intense machining conditions.
Details:
- Microstructure Advantages: Fine-grained structures enhance toughness and resist cracks or chips.
- High Hardness Levels: Closer to diamond on the hardness scale, tungsten carbide can handle abrasive materials.
- Thermal Stability: Maintains integrity under high cutting speeds and temperatures common in metal machining.
Types of Tungsten Carbide Wear Parts for CNC/Lathe/Mill Applications
Tungsten carbide can be formed into a wide range of wear parts that integrate seamlessly into metal machining equipment, enhancing performance at every stage.
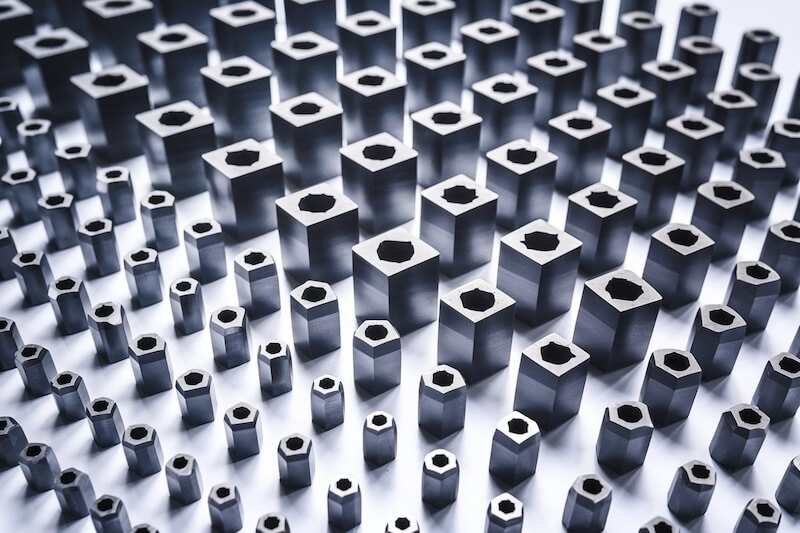
Cutting Inserts
Replaceable inserts with tungsten carbide edges deliver cleaner cuts, tighter tolerances, and longer tool life.
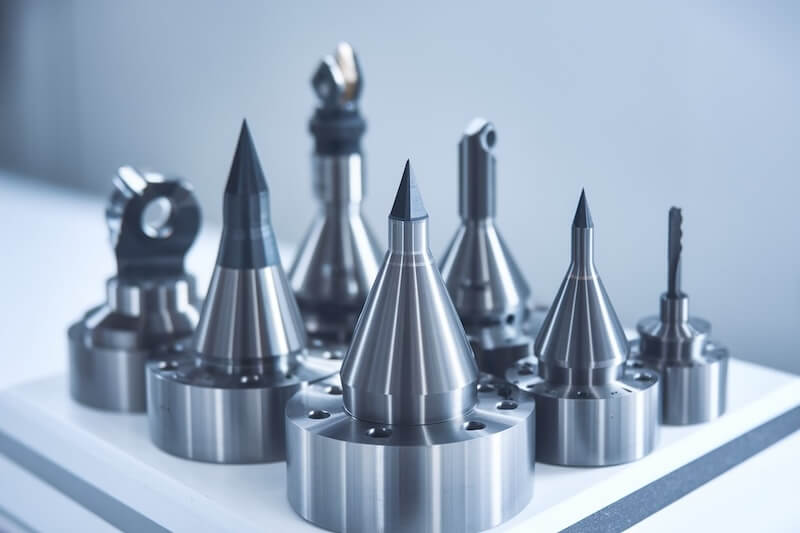
End Mills and Drills
Carbide-tipped tools maintain their sharpness, enabling higher cutting speeds without sacrificing surface finish or accuracy.

Boring Bars and Turning Tools
Carbide wear parts ensure stable cutting parameters, reducing chatter, improving dimensional stability, and prolonging service intervals.
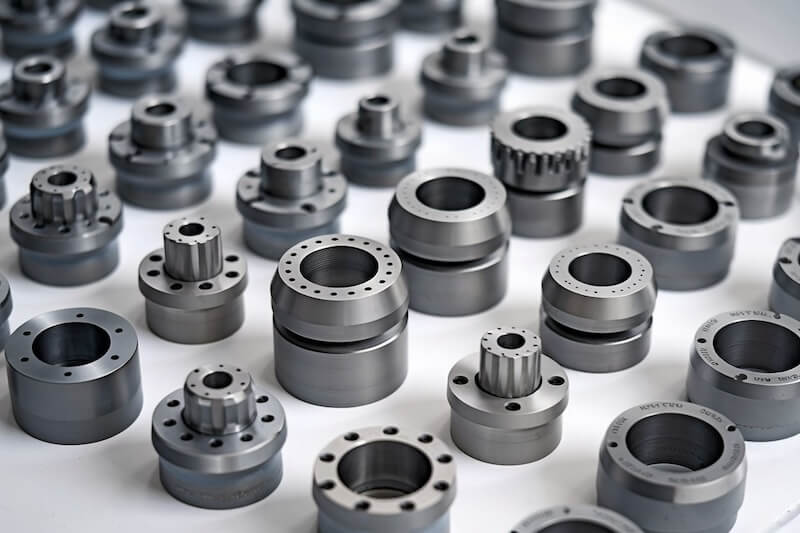
Tool Holders and Bushings
Supportive wear parts made from tungsten carbide maintain alignment and reduce vibration, contributing to smoother machining operations.
Quick and easy: Enter your specifications and get a quote in one business day
Comparing Tungsten Carbide to Other Tool Materials
While tool steels, high-speed steel (HSS), and coated alloys have their place, tungsten carbide wear parts frequently outperform these alternatives on critical metrics like durability, precision, and cost-efficiency.
Details:
- Versus Tool Steel: Tungsten carbide lasts significantly longer, reducing the frequency of replacements and machine downtime.
- Versus HSS: HSS dulls more quickly under high-speed or hard-material cutting, whereas carbide retains sharpness and edge geometry.
- Versus Coated Alloys: Once coatings wear off, underlying alloys degrade quickly; tungsten carbide’s solid structure ensures consistent performance from start to end.

Operational Advantages: Efficiency, Productivity, and Quality
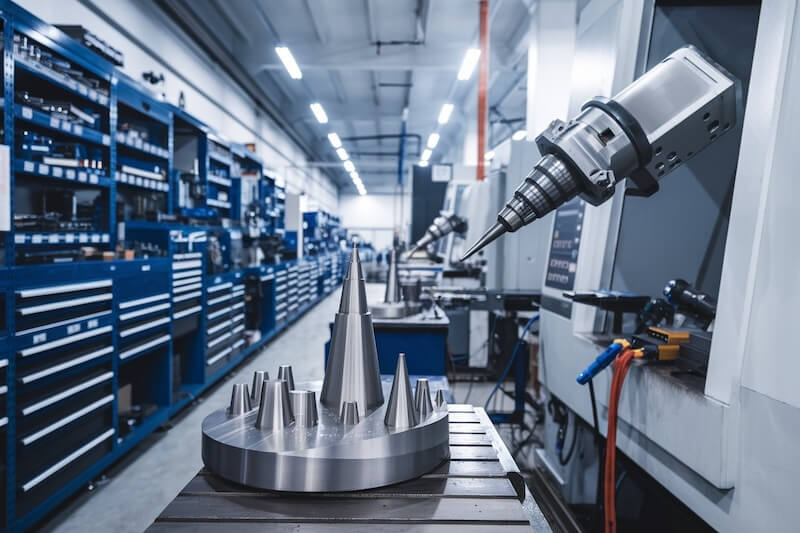
Investing in tungsten carbide wear parts transforms machining operations, offering a multitude of operational benefits that directly impact the bottom line.
Details:
- Extended Tool Life: With slower wear rates, companies reduce spare parts inventories and tooling expenses.
- Higher Cutting Speeds: Tungsten carbide enables faster machining rates, increasing throughput and decreasing cycle times.
- Improved Surface Finishes: Consistent edge geometry and minimal deflection lead to superior product quality with fewer rejected parts.
- Lower Scrap Rates: Enhanced dimensional accuracy reduces the need for rework and corrective machining, improving material utilization.
Cost Savings and Long-Term Return on Investment
While tungsten carbide components may initially be more expensive than traditional options, the long-term financial gains justify the investment.
Details:
- Reduced Maintenance Costs: Longer tool life and stable performance diminish the frequency of maintenance shutdowns and emergency repairs.
- Lower Labor Costs: Operators spend less time changing tools and making machine adjustments, increasing overall workforce productivity.
- Better Resource Allocation: With fewer defective parts and improved efficiency, machining facilities can allocate resources more effectively, boosting profit margins.

Versatility for Various Metals and Complex Geometries
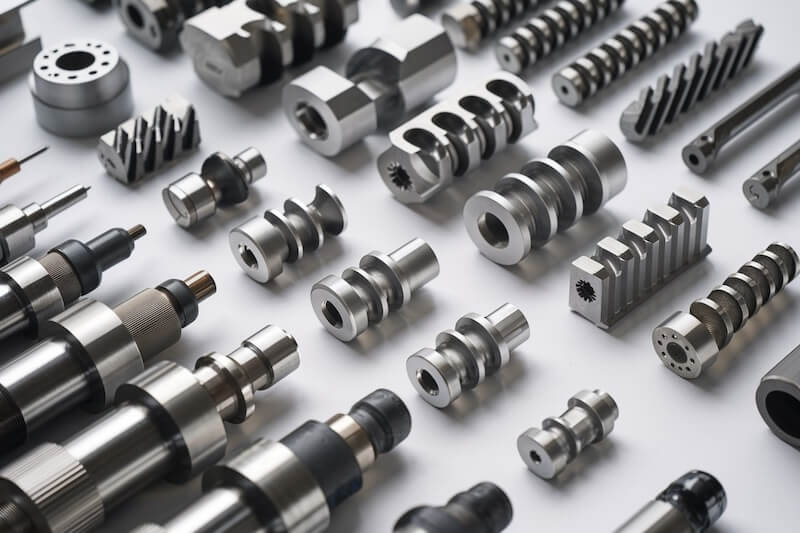
The Metal Machining industry deals with a range of materials—from aluminum and steel to titanium and high-strength alloys. Tungsten carbide’s versatility allows it to handle diverse metals and tackle intricate part designs with ease.
Details:
- Adaptive Tooling: Carbide tools excel in cutting both soft metals and heat-resistant superalloys without losing effectiveness.
- Complex Shapes and Contours: Dimensional stability and wear resistance enable precise machining of intricate features and tight corners.
- Future-Ready Solutions: As market demands shift toward lighter, stronger, and more complex components, tungsten carbide tools are well-positioned to meet these evolving challenges.
Selecting the Right Supplier and Ensuring Quality Assurance
To maximize the benefits of tungsten carbide wear parts, partnering with a reputable supplier that emphasizes quality, innovation, and technical support is crucial.
Details:
- Material Consistency: Reliable suppliers maintain strict quality controls and provide detailed material certifications, ensuring parts meet specified standards.
- Technical Consultation: Experienced suppliers offer guidance on tool geometries, carbide grades, and coatings best suited for particular machining tasks.
- After-Sales Support: Ongoing assistance, including tool reconditioning and performance optimization, guarantees that companies realize the full value of their tungsten carbide investments.
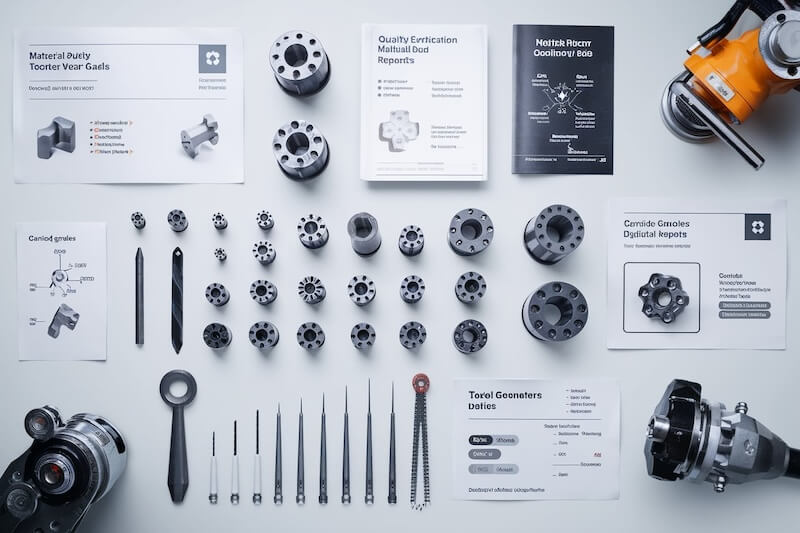
Conclusion
For decision-makers in the Metal Machining (CNC/Lathe/Mill) industry, tungsten carbide wear parts present a strategic upgrade that addresses modern manufacturing challenges.
By embracing tungsten carbide tools, companies can achieve longer tool life, better machining efficiency, improved product quality, and substantial cost savings over time.
From cutting inserts and end mills to tool holders and bushings, this material’s remarkable properties empower businesses to stay competitive, meet evolving customer demands, and secure their position at the forefront of precision machining.
Quick and easy: Enter your specifications and get a quote in one business day