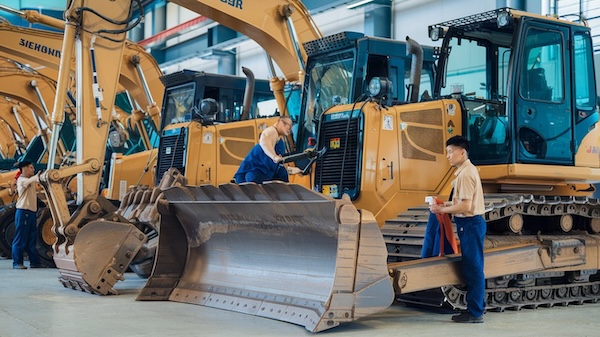
Construction Machines Carbide Wear Parts
Retop Carbide aimed at guiding construction industry decision-makers to appreciate the advantages of tungsten carbide wear parts. By exploring the unique properties of tungsten carbide, comparing it to alternative materials, and highlighting the operational and financial benefits, this piece will illustrate why choosing tungsten carbide wear parts is a strategic investment for construction machinery and equipment.
Quick and easy: Enter your specifications and get a quote in one business day
Table of Contents
Expertise in Construction Tungsten Carbide Tooling
Retop Carbide’ specialty construction tungsten carbide tooling is trusted and used by the manufacturing leaders in the industry.
Types of Construction Tungsten Carbide Tooling
- Cutting and milling tools
- Drill bits and augers
- Wear liners, plates, and inserts
- Concrete drill bits
- Masonry cutting tools
- Pavement milling teeth
- Others
Introduction: Meeting the Challenges of Modern Construction Projects
As construction projects grow increasingly complex, demands on machinery and equipment intensify. Higher workloads, stricter deadlines, and the need to handle abrasive materials push traditional wear parts beyond their limits. Tungsten carbide emerges as a solution that meets these evolving challenges, helping companies maintain efficiency and competitiveness.
Details:
- Growing Project Complexity: Larger infrastructure developments and tighter timelines require more robust, reliable equipment.
- Harsh Conditions: Operating in environments with dust, grit, and debris demands wear parts that withstand severe abrasion.
- Performance Under Pressure: Tungsten carbide parts ensure machinery can operate longer and more reliably under intense workloads.
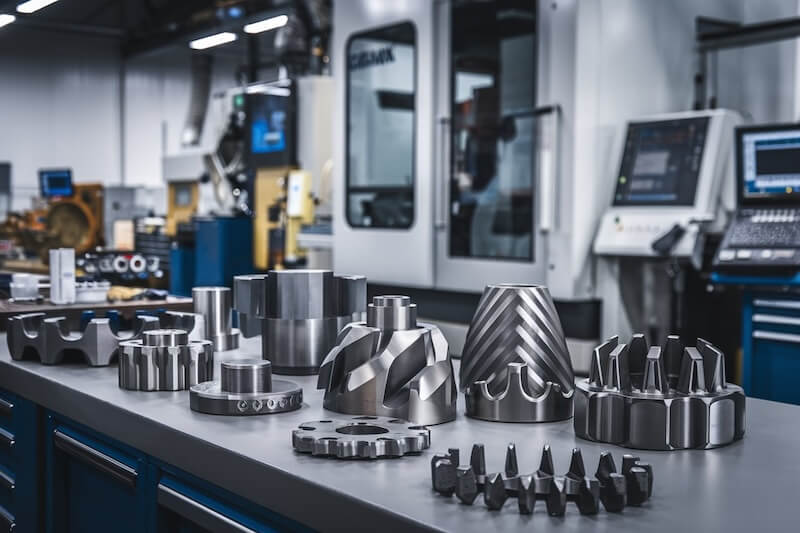
Understanding Tungsten Carbide: Composition and Key Properties
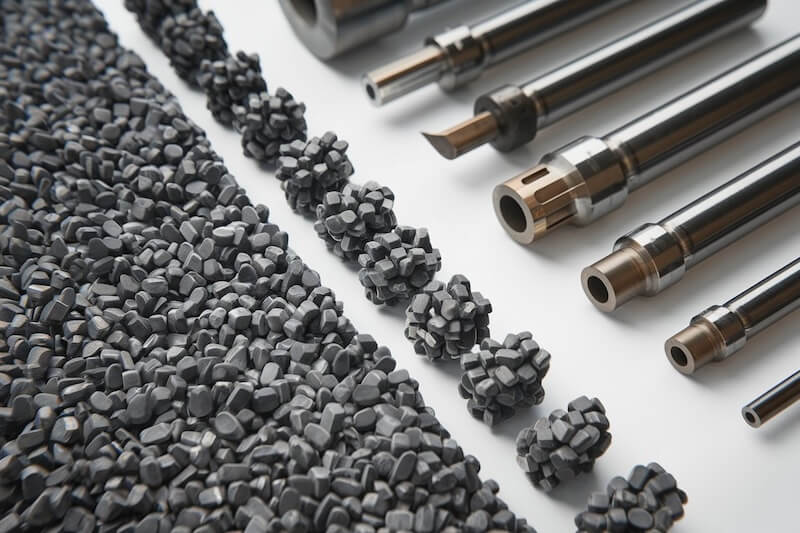
Tungsten carbide is a composite made from tungsten carbide powder and a metal binder, typically cobalt, resulting in a hard, dense material. This unique composition provides excellent hardness, toughness, and wear resistance, making it ideal for construction machinery wear parts.
Details:
- Superior Hardness: Tungsten carbide’s hardness is close to diamond, ensuring minimal wear even in abrasive conditions.
- High Density and Strength: The composite structure resists chipping, cracking, and deformation.
- Thermal and Corrosion Resistance: Parts made of tungsten carbide maintain integrity under high temperatures and corrosive substances.
Types of Tungsten Carbide Wear Parts in Construction Equipment
Tungsten carbide isn’t limited to a single type of component; it can be integrated into various machinery parts that face heavy wear, enhancing equipment longevity and reliability.
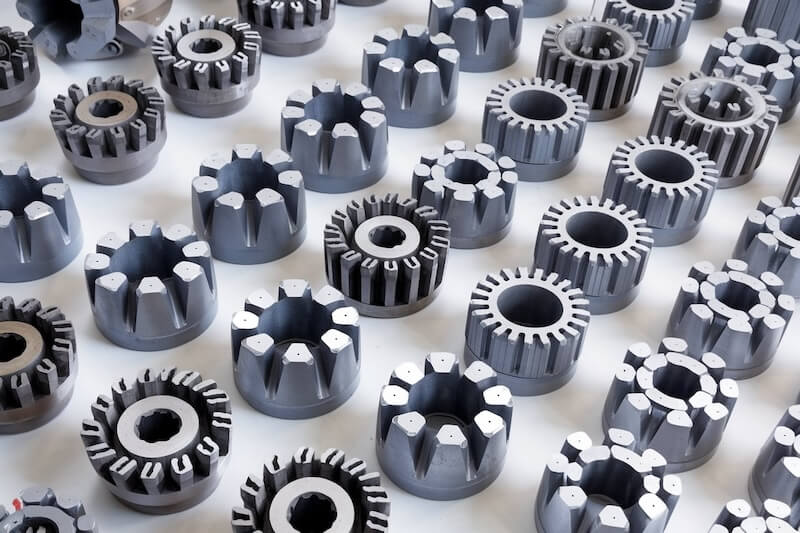
Cutting and Milling Tools
Road milling bits, cutter heads, and excavator teeth made from carbide deliver consistent performance and extended tool life.
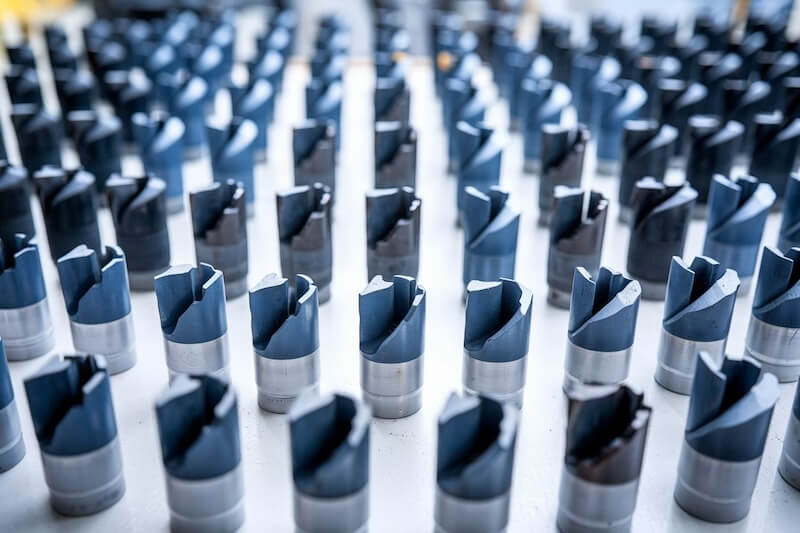
Drill Bits and Augers
Carbide-tipped drill bits and augers penetrate hard soils, rocks, and other challenging materials with reduced tool changes.
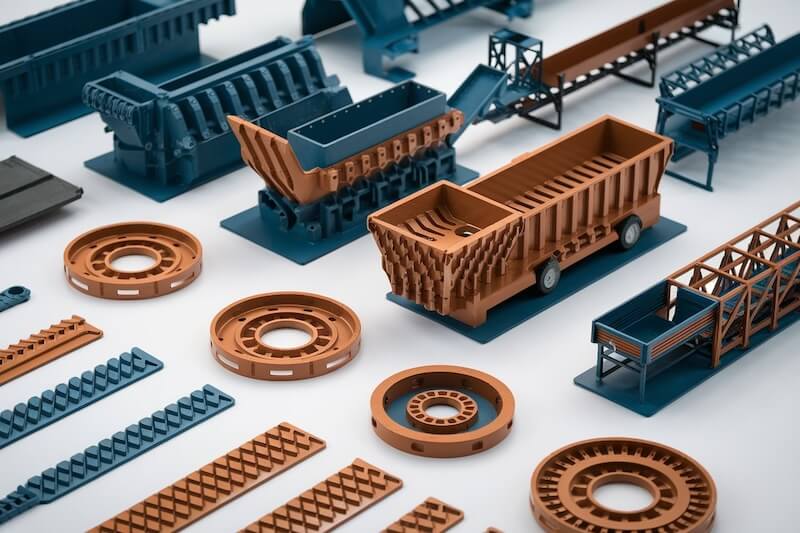
Wear Liners, Plates, and Inserts
Protective linings within crushers, hoppers, and conveyor systems reduce abrasion, extending maintenance intervals.
Quick and easy: Enter your specifications and get a quote in one business day
Comparing Tungsten Carbide to Other Wear-Resistant Materials
While steels, alloys, and ceramics have been common choices, tungsten carbide offers enhanced durability and performance that often surpasses these traditional materials.
Details:
- Versus Heat-Treated Steel: Tungsten carbide lasts significantly longer, reducing the frequency of downtime and lowering maintenance expenses.
- Versus Alloyed Steels or Hardened Castings: Carbide’s unmatched hardness and toughness result in fewer replacements and more stable production schedules.
- Versus Ceramics: Though hard, ceramics can be brittle. Tungsten carbide strikes a better balance between hardness and fracture resistance.
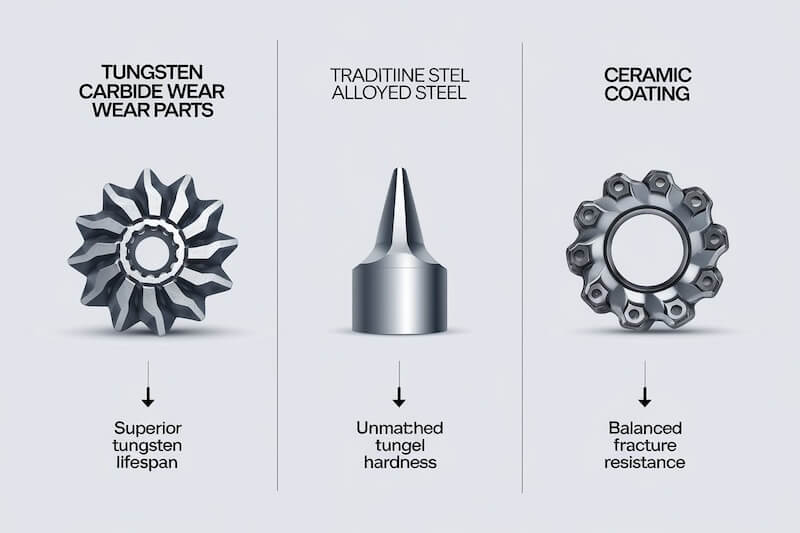
Operational Advantages: Boosting Efficiency and Reducing Downtime
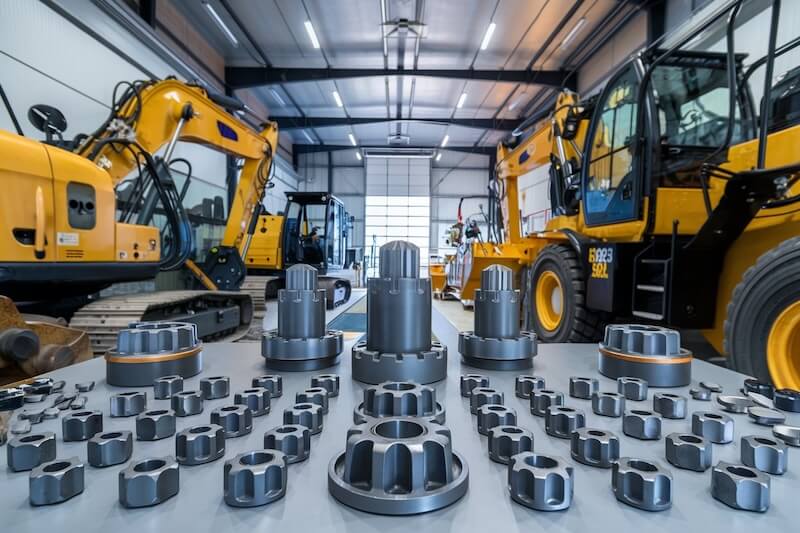
Tungsten carbide wear parts provide tangible benefits that directly impact a construction company’s bottom line. With parts that last longer and maintain their shape, operators enjoy steady productivity without frequent interruptions.
Details:
- Extended Service Life: Longer-lasting components mean fewer tool changes and reduced spare parts inventory.
- Consistent Performance: Stable cutting edges and surfaces produce uniform results, improving overall work quality.
- Reduced Machine Setup Times: With fewer unexpected breakdowns, operators spend more time producing and less on adjustments or rework.
Cost Savings and Improved Profitability over the Long Term
Although tungsten carbide components may carry a higher initial cost, the return on investment (ROI) becomes evident through lower maintenance expenses, minimized downtime, and improved material utilization.
Details:
- Fewer Replacements: Longer wear part lifespans reduce the cost of frequent tool purchases.
- Lower Labor Costs: Less time spent on maintenance translates into higher labor productivity.
- Better Resource Allocation: With reliable tooling, companies can plan projects more effectively, meeting deadlines and enhancing client satisfaction.
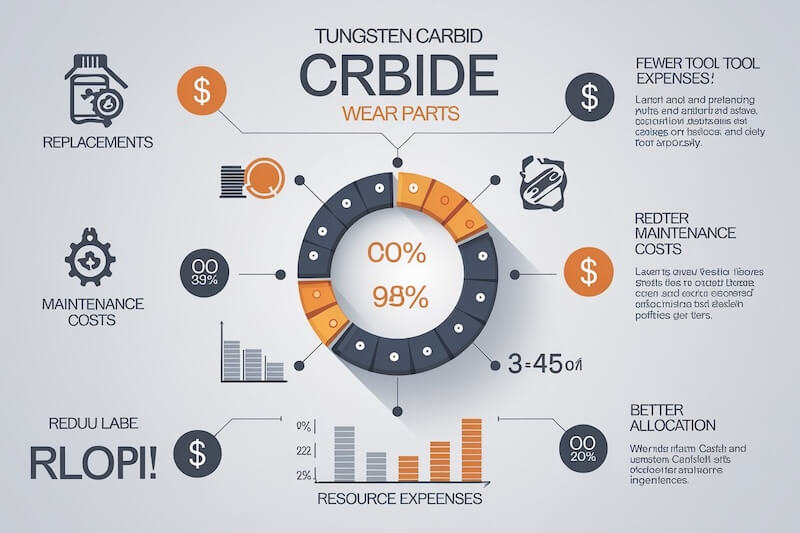
Adapting to a Range of Construction Machines and Conditions
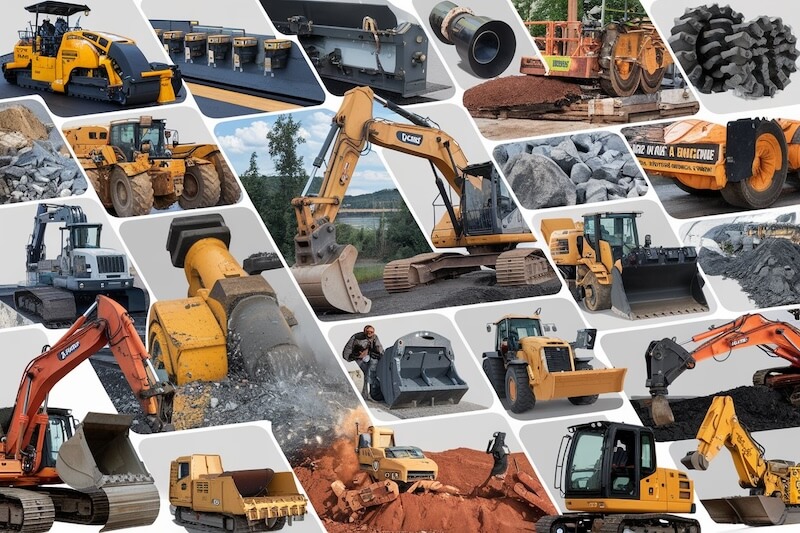
The construction industry involves a wide array of applications—from road construction to earthmoving and demolition. Tungsten carbide’s versatility allows it to excel in each scenario, ensuring equipment can handle varying materials and conditions with ease.
Details:
- Roadwork Machines: Milling drums, planer teeth, and asphalt cutters benefit from carbide’s abrasion resistance.
- Earthmoving Equipment: Excavators, loaders, and trenchers equipped with carbide wear parts maintain productivity in rock-laden and abrasive terrains.
- Demolition Tools: Carbide-tipped breakers and hammers retain their cutting edges, improving the speed and efficiency of material removal.
Selecting a Trustworthy Supplier and Ensuring Quality Assurance
To maximize the benefits of tungsten carbide wear parts, partnering with a reputable supplier that emphasizes quality control, innovation, and after-sales support is crucial.
Details:
- Material Certifications: Reliable suppliers provide documentation and test reports, confirming that parts meet industry standards.
- Technical Consultation: Expert guidance in choosing the right carbide grades and tool geometries ensures optimal performance in specific projects.
- After-Sales Support: Ongoing assistance, including maintenance tips and part reconditioning services, helps companies get the most out of their investment.
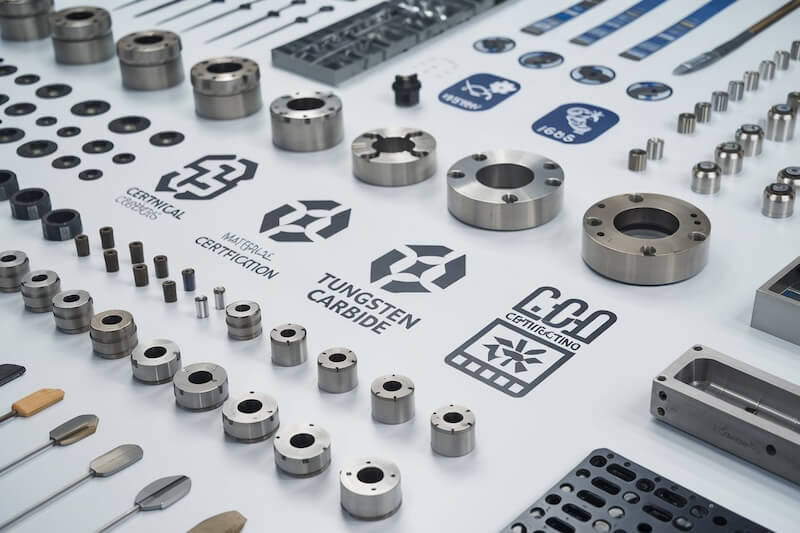
Conclusion
As the construction industry continues to evolve, adopting materials like tungsten carbide becomes a strategic necessity.
Tungsten carbide wear parts empower companies to tackle more demanding projects, operate equipment longer with less downtime, and ultimately achieve greater cost-effectiveness.
By understanding its properties, evaluating its advantages over traditional alternatives, and selecting a reputable supplier, decision-makers can confidently incorporate tungsten carbide wear parts into their machinery. This forward-thinking choice enhances productivity, operational efficiency, and competitiveness—positioning construction companies for long-term success.
Quick and easy: Enter your specifications and get a quote in one business day