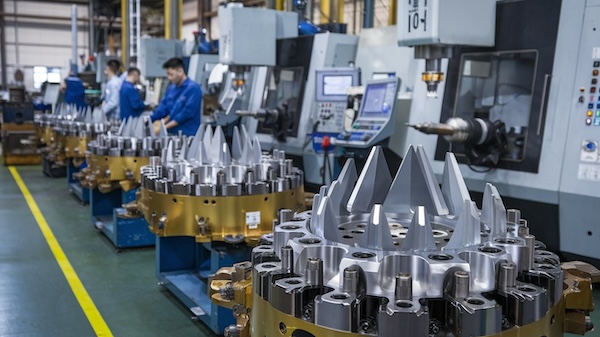
Aerospace Manufacturing Carbide Toolings
Retop is crafted to help aerospace manufacturing decision-makers understand the unique benefits of tungsten carbide wear parts. By examining the fundamental properties, comparing with other materials, and illustrating the operational and financial gains, we aim to convince industry leaders to incorporate tungsten carbide into their aerospace machinery and equipment.
Quick and easy: Enter your specifications and get a quote in one business day
Table of Contents
Expertise in Aerospace Manufacturing Carbide Tooling
Retop Carbide’ specialty aerospace manufacturing tooling is trusted and used by the manufacturing leaders in the industry.
Types of Aerospace Manufacturing Carbide Tooling
- High-speed end mills
- Reamers
- Countersinks
- Cutting and drilling tools
- Broaches and inserts
- Bushings, bearings, and guides
- Others
Introduction: Addressing the Growing Demands of Aerospace Manufacturing
As aerospace manufacturing advances, production lines face stringent requirements: tighter tolerances, advanced alloys, and complex geometries. Traditional wear parts often struggle under these evolving conditions. Tungsten carbide emerges as a high-performance solution, offering longevity, stability, and precision that helps meet increasing industry demands.
Details:
- Rising Complexity: High-value components require superior accuracy and minimal defects.
- High-Performance Materials: Machining advanced alloys like titanium or Inconel demands wear parts capable of withstanding intense stress and heat.
- Global Competition: Manufacturers need cutting-edge materials to maintain productivity, quality, and competitiveness in the global aerospace market.
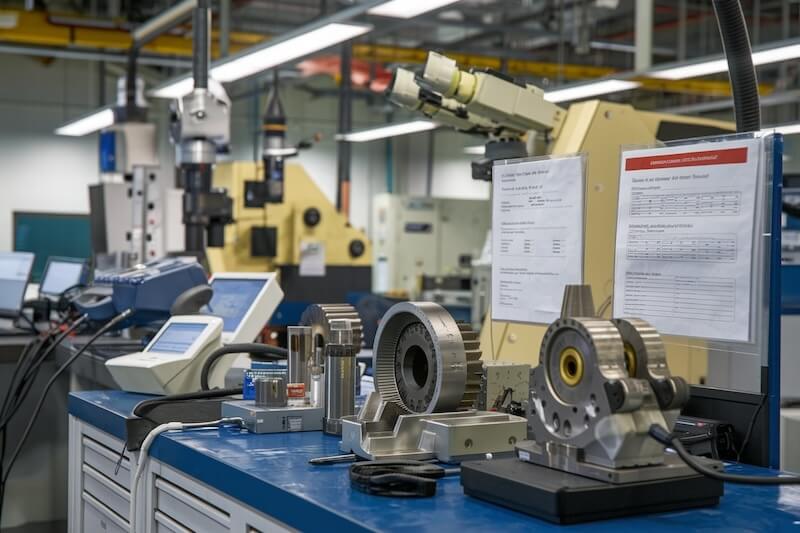
Understanding Tungsten Carbide: Properties and Advantages
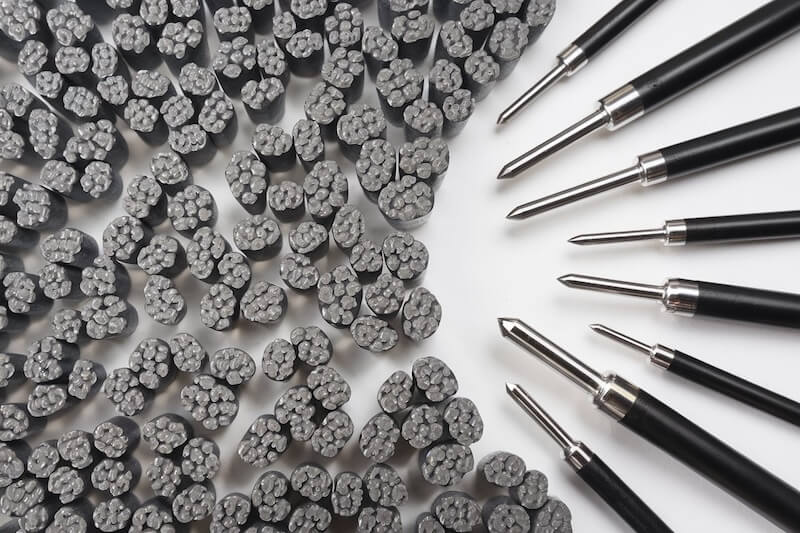
Tungsten carbide is a composite material made from tungsten carbide powder and a metallic binder. Its remarkable hardness, wear resistance, and thermal stability set it apart from conventional tooling materials. For aerospace applications, these properties ensure that machines operate efficiently, delivering precision and repeatability in harsh environments.
Details:
- Near-Diamond Hardness: Extended tool life and consistent performance under heavy loads and abrasive conditions.
- Thermal Stability: Maintains integrity at high temperatures common in aerospace machining.
- Dimensional Accuracy: Ensures critical components maintain tight tolerances, enhancing part quality and safety.
Applications of Tungsten Carbide Wear Parts in Aerospace Equipment
Tungsten carbide can be integrated into a variety of aerospace manufacturing tools and equipment, optimizing every stage of production.
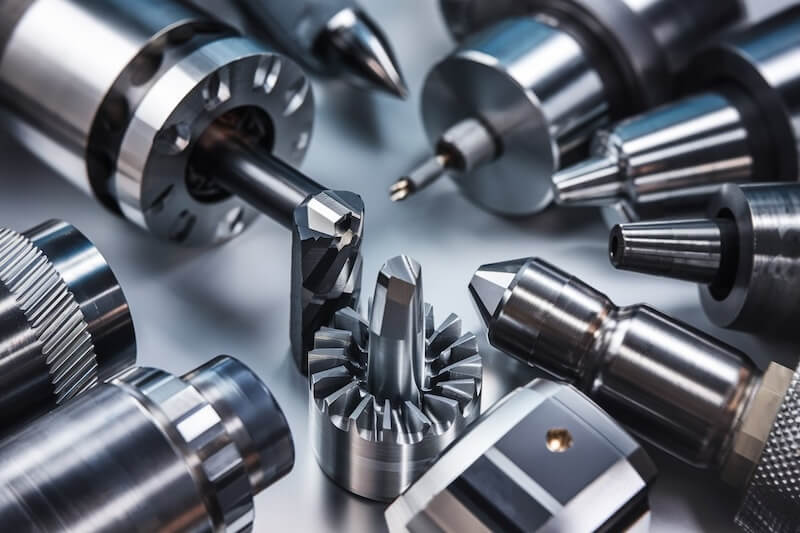
Cutting and Drilling Tools
Carbide-tipped end mills, drills, and reamers withstand repeated cutting cycles of tough aerospace alloys.
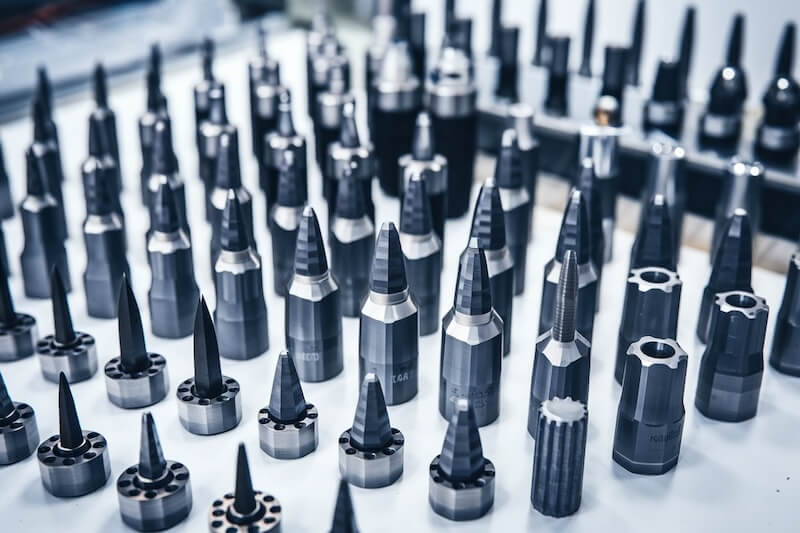
Broaches and Inserts
Carbide inserts offer superior edge retention for complex machining operations with reduced tool changes.
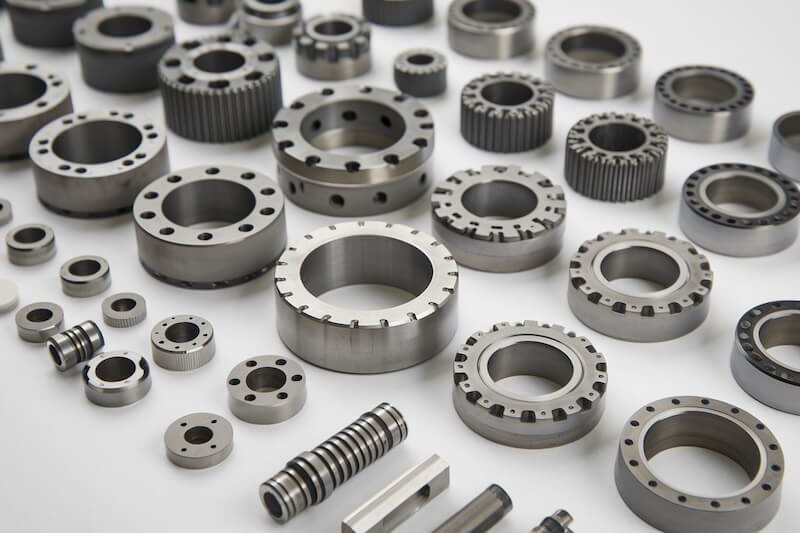
Bushings, Bearings, and Guides
Carbide wear parts ensure stable, low-friction movement within precision machines, enhancing output quality and lifespan.
Quick and easy: Enter your specifications and get a quote in one business day
Comparing Tungsten Carbide to Other Tooling Materials
While high-speed steel (HSS), tool steel, and coated alloys have historically served the aerospace industry, tungsten carbide often outperforms these alternatives, ensuring better operational results.
Details:
- Versus HSS or Tool Steel: Tungsten carbide’s hardness and toughness allow for higher cutting speeds and longer intervals before tool replacement.
- Versus Coated Tools: Once coatings wear off, underlying metals degrade quickly; carbide’s solid strength endures throughout its structure.
- Versus Ceramics: Ceramics can be brittle; tungsten carbide’s balanced combination of hardness and toughness provides dependable, long-term service.
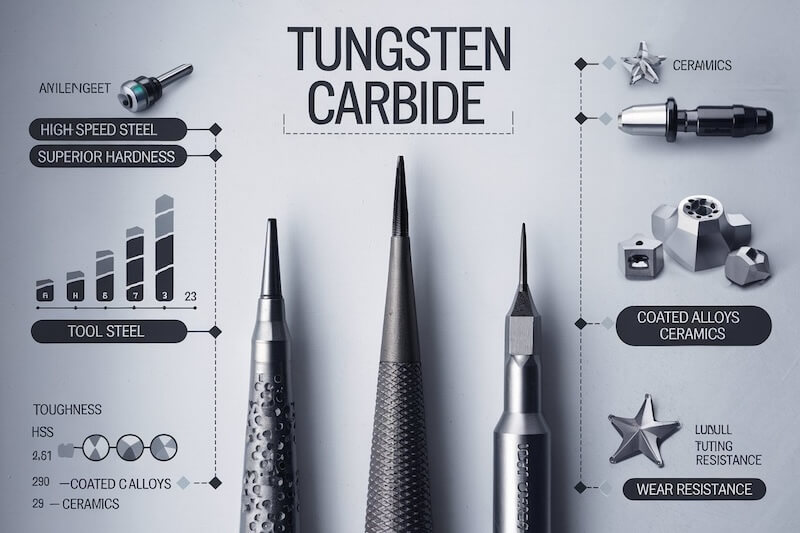
Operational Benefits: Efficiency, Consistency, and Quality
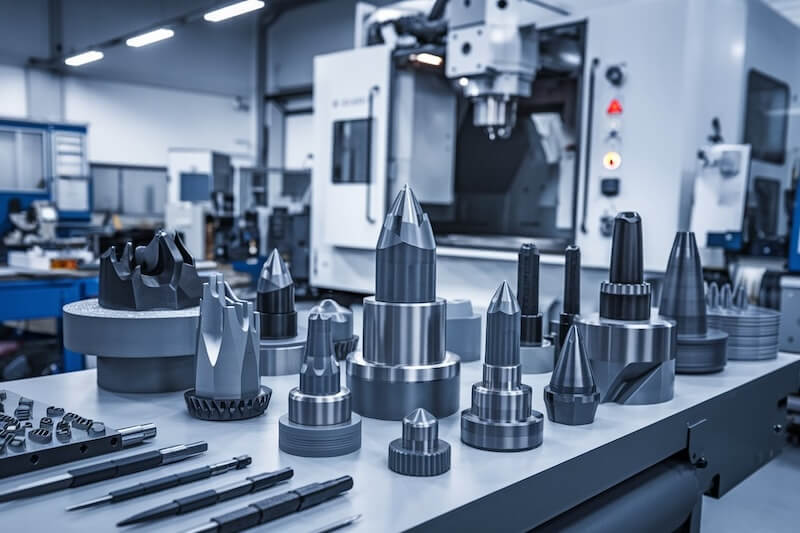
Adopting tungsten carbide wear parts brings immediate operational improvements, directly impacting the bottom line and enhancing overall manufacturing quality.
Details:
- Extended Tool Life: Fewer tool changes and reduced downtime lead to consistent production schedules and improved efficiency.
- Superior Surface Finishes: Stable, sharp edges and minimal tool deflection produce smoother surfaces, reducing post-processing steps.
- Predictable Performance: Consistent tool behavior maintains process reliability, ensuring compliance with strict aerospace standards.
Cost Savings and Long-Term Return on Investment
Although tungsten carbide can cost more upfront, the long-term financial returns justify the investment through reduced maintenance, lower scrap rates, and optimized productivity.
Details:
- Reduced Maintenance Costs: Longer-lasting wear parts diminish the frequency of replacements and unscheduled repairs.
- Less Scrap and Rework: Improved accuracy and consistent tool geometry minimize material wastage and re-machining efforts.
- Better Resource Allocation: With reliable tools, plant managers can plan production runs more effectively, meeting tight deadlines and customer expectations.
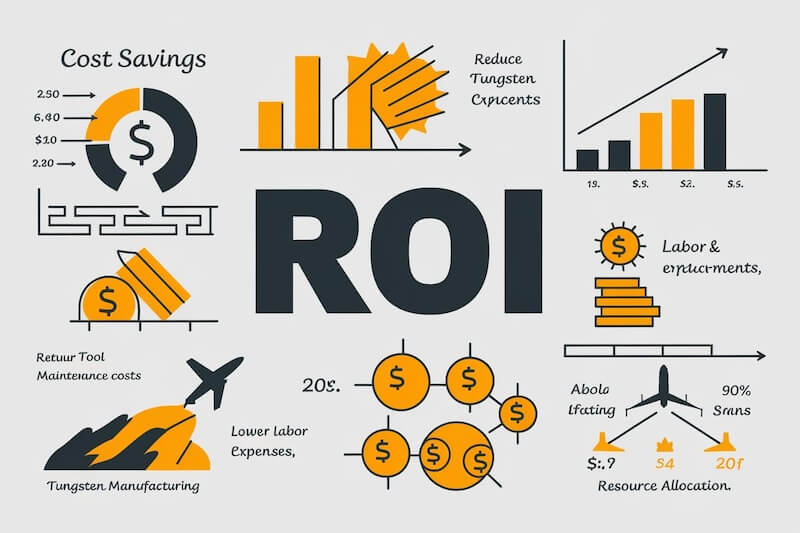
Meeting Regulatory and Quality Standards in Aerospace Manufacturing
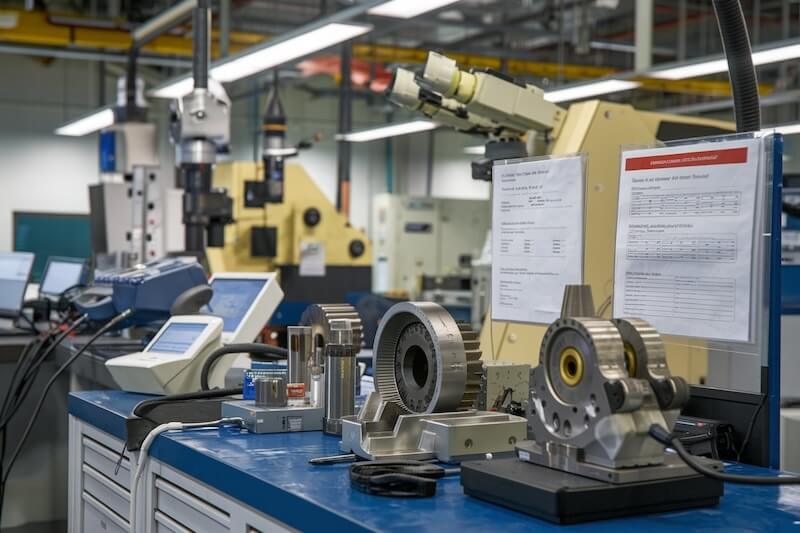
Aerospace components face rigorous quality, safety, and compliance standards. Tungsten carbide wear parts help meet these stringent criteria by providing consistent, high-quality machining results, ultimately supporting certification and regulatory approvals.
Details:
- Enhanced Reliability: Durability and repeatability ensure that parts meet demanding aerospace specifications.
- Traceability and Documentation: Top-tier suppliers provide certifications and quality reports, reassuring compliance with international aerospace standards.
- Improved Safety Margins: Quality-assured components lead to safer aircraft assemblies, bolstering brand reputation and customer trust.
Selecting a Trusted Supplier and Ensuring Quality Assurance
To realize the full benefits of tungsten carbide, choose a supplier that emphasizes quality, technical expertise, and after-sales support.
Details:
- Material Certifications: Reliable suppliers offer detailed material and inspection reports, confirming adherence to aerospace-grade specifications.
- Technical Consultation: Skilled engineers recommend optimal carbide grades, tool geometries, and coatings suited for specific aerospace applications.
- Ongoing Support: Maintenance advice, tool reconditioning, and performance optimization services help manufacturers maximize their tungsten carbide investments.
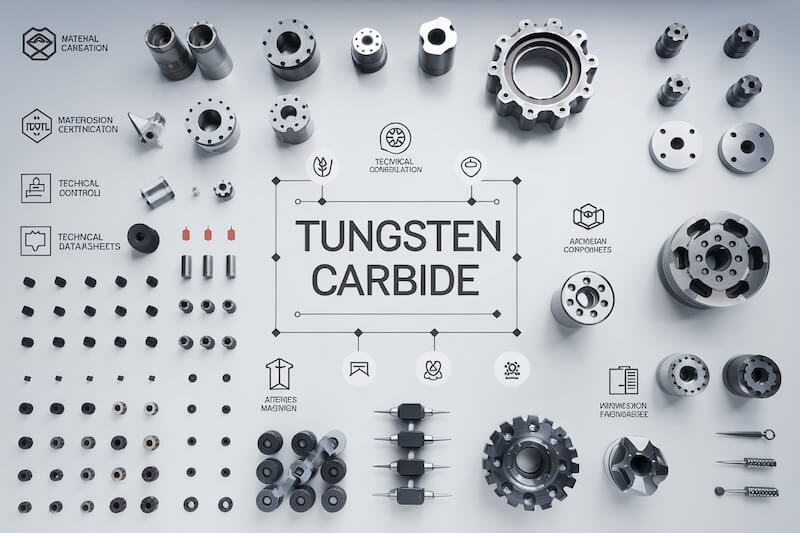
Conclusion
As the aerospace manufacturing sector grows more demanding, tungsten carbide wear parts provide a strategic advantage.
Their exceptional hardness, thermal stability, and precision equip aerospace machinery with the durability and accuracy needed to navigate complex alloys and tight tolerances.
By investing in tungsten carbide, decision-makers not only enhance operational efficiency, reduce long-term costs, and comply with rigorous standards but also strengthen their competitive position in an evolving global industry.
Quick and easy: Enter your specifications and get a quote in one business day