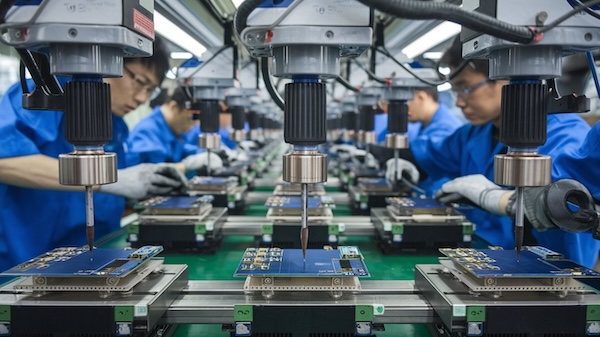
Electronics Manufacturing Carbide Tooling
Retop Carbide is designed to inform decision-makers in the electronics manufacturing sector about the advantages of adopting tungsten carbide wear parts. By exploring its defining properties, comparing it to alternative materials, and illustrating practical and financial benefits, this piece aims to highlight why tungsten carbide is a strategic investment for electronics production equipment.
Quick and easy: Enter your specifications and get a quote in one business day
Table of Contents
Expertise in Electronics Manufacturing Carbide Tooling
Retop Carbide’ specialty electronics manufacturing carbide tooling is trusted and used by the manufacturing leaders in the industry.
Types of Electronics Manufacturing Tooling
- Micro milling cutters
- PCB drilling bits
- Cutting and punching tools
- Milling and drilling bits
- Die inserts and molds
- Other
Introduction: Meeting the Demands of Modern Electronics Manufacturing
With consumer electronics becoming smaller, more intricate, and more advanced, manufacturing lines must handle tighter tolerances, delicate materials, and repetitive processes. Traditional wear parts often fail to deliver the durability and precision needed. Tungsten carbide, known for its exceptional hardness and wear resistance, provides a superior solution to meet the exacting demands of electronics manufacturing.
Details:
- Micro-Scale Components: Miniaturized parts and complex circuitry require tooling that can maintain accuracy over extended runs.
- High-Volume Production: Consistent tool performance supports continuous production without frequent downtime.
- Evolving Technologies: As electronics progress, robust wear parts help manufacturers swiftly adapt to new materials and designs.
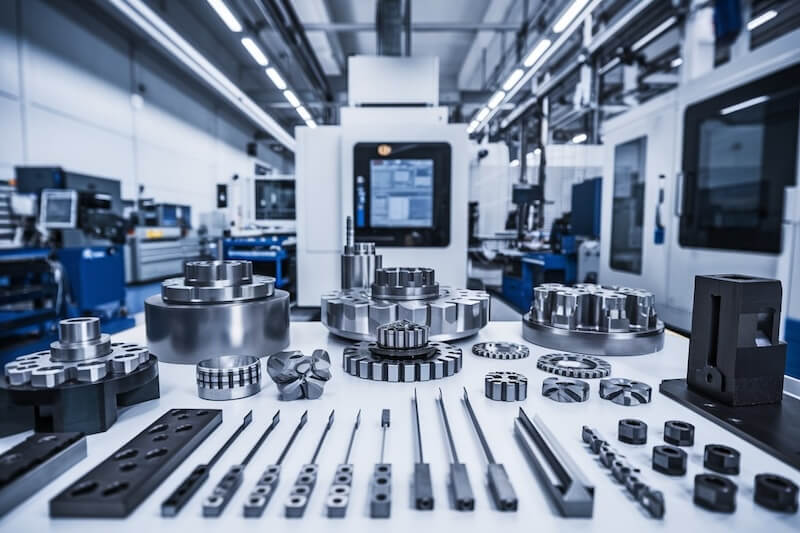
Understanding Tungsten Carbide: Properties and Advantages
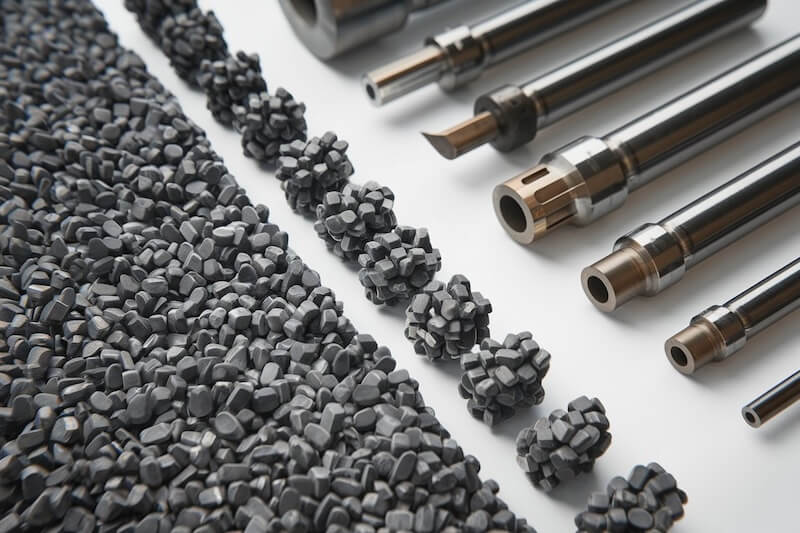
Tungsten carbide is a composite material combining tungsten carbide powder and a metallic binder, delivering near-diamond hardness, exceptional toughness, and thermal stability. This unique blend makes it a prime candidate for high-precision, high-volume electronics manufacturing.
Details:
- Extreme Hardness: Offers prolonged edge sharpness, ensuring uniform component dimensions and minimal tool wear.
- Heat and Corrosion Resistance: Performs reliably under challenging conditions, such as high-speed operations and contact with corrosive substances.
- Dimensional Stability: Maintains tight tolerances over long production runs, essential for consistent product quality in electronics.
Applications of Tungsten Carbide Wear Parts in Electronics Equipment
Tungsten carbide can be integrated into various electronics manufacturing stages, enhancing the reliability and efficiency of production lines.
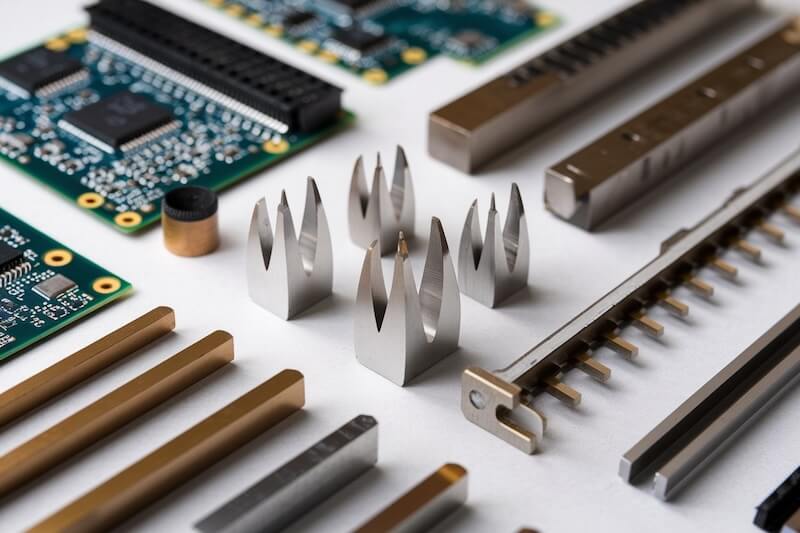
Cutting and Punching Tools
Carbide-tipped blades and punches retain their geometry, improving cut quality on printed circuit boards (PCBs).
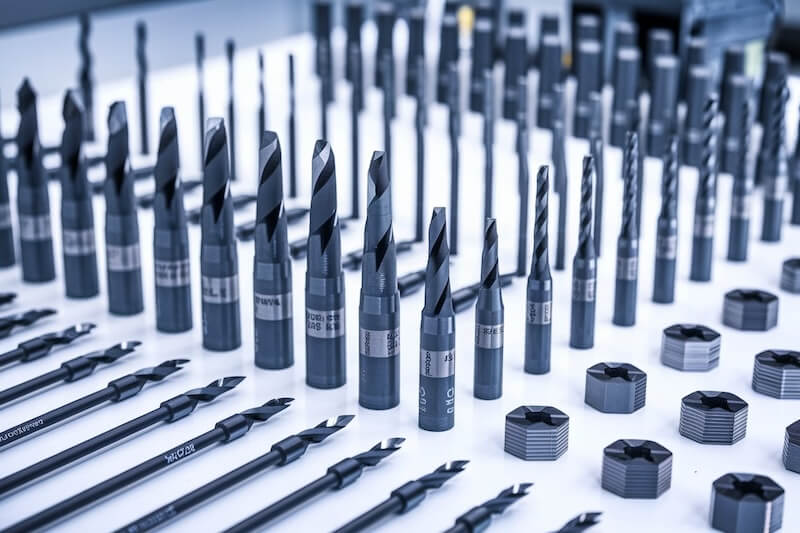
Milling and Drilling Bits
Carbide drills and end mills withstand abrasive fiberglass boards and hard substrates, minimizing breakages and achieving cleaner holes.
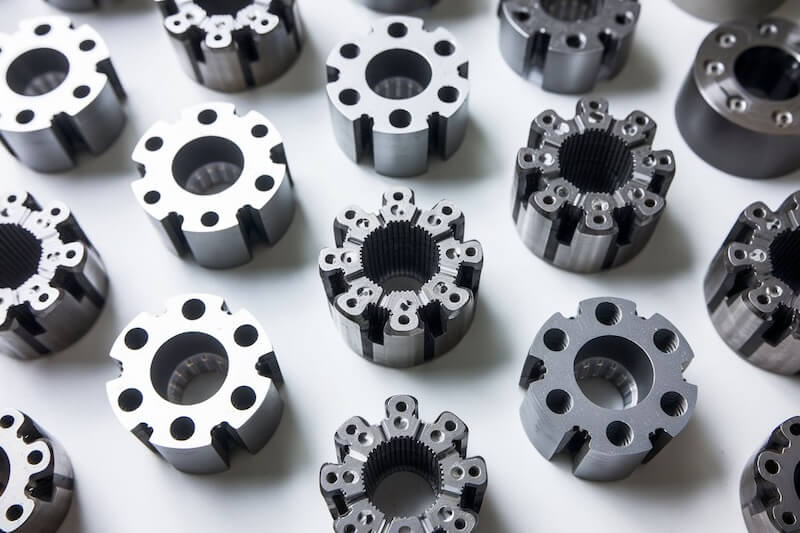
Die Inserts and Molds
Carbide inserts maintain the required precision in molding and stamping electronic components, ensuring consistent outputs.
Quick and easy: Enter your specifications and get a quote in one business day
Comparing Tungsten Carbide to Other Tooling Materials
While tool steels, high-speed steel (HSS), and coated alloys have their place, tungsten carbide’s longevity and resilience often surpass these alternatives, bringing direct benefits to electronics manufacturing.
Details:
- Versus Tool Steel: Tungsten carbide’s hardness and toughness extend tool life, reducing downtime and spare part needs.
- Versus HSS: Carbide’s higher wear resistance and dimensional stability enable higher cutting speeds and tighter tolerances.
- Versus Coated Alloys: Unlike coatings that wear off, tungsten carbide’s properties run through its entire structure, offering sustained performance.
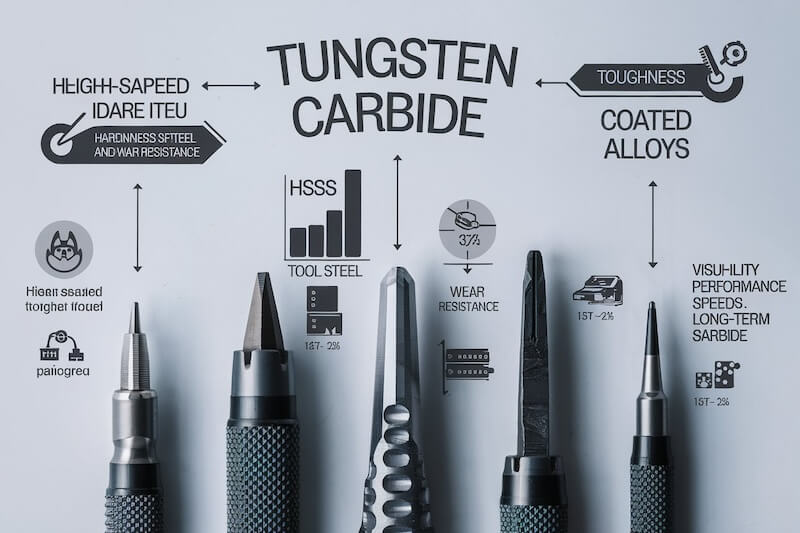
Operational Advantages: Efficiency, Quality, and Consistency
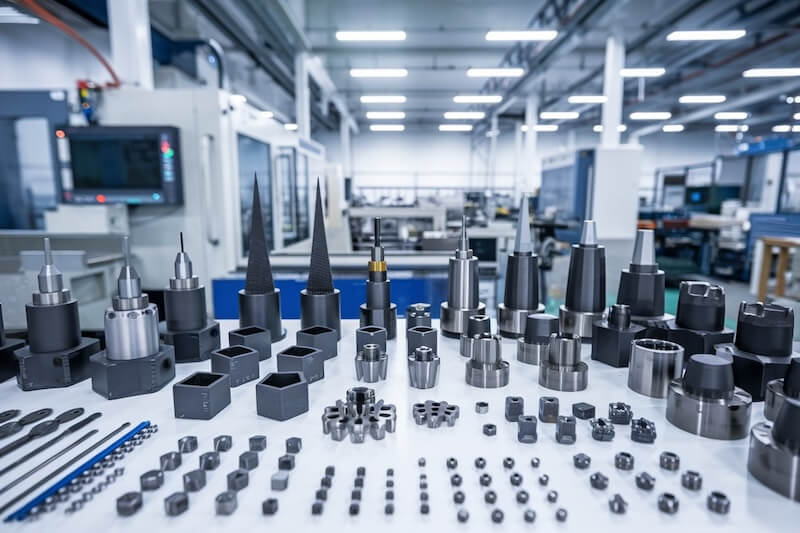
Implementing tungsten carbide wear parts yields tangible improvements in production line efficiency, component quality, and overall manufacturing consistency.
Details:
- Longer Tool Life: Fewer replacements mean less downtime and smoother production flow.
- Improved Surface Finishes: Consistent edge sharpness results in cleaner cuts and more precise component geometries.
- Lower Defect Rates: Enhanced accuracy and stable performance reduce material wastage and rework costs.
Cost Savings and Enhanced ROI
While tungsten carbide may entail a higher initial investment, the long-term financial benefits—from reduced maintenance to higher throughput—justify the cost and contribute to a strong return on investment.
Details:
- Reduced Maintenance Expenses: Prolonged tool lifespan cuts labor, inventory, and replacement part costs.
- Minimized Scraps and Reworks: Stable, accurate machining lowers the number of defective components, protecting profit margins.
- More Predictable Scheduling: Reliable tooling supports on-time delivery and efficient resource allocation.
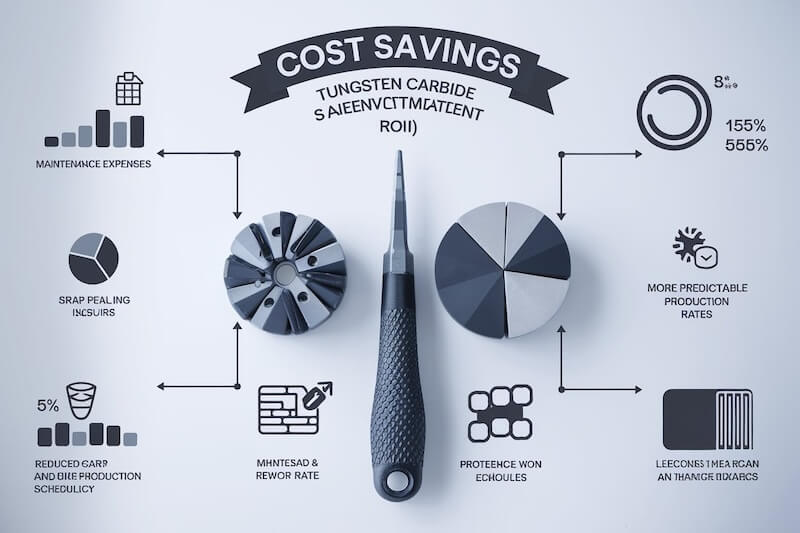
Scalability and Adaptability for Emerging Electronics Trends

As the electronics industry evolves, new materials, form factors, and assembly techniques emerge. Tungsten carbide’s robust properties prepare manufacturers to adapt quickly and maintain competitiveness in a dynamic marketplace.
Details:
- Next-Generation Devices: Tungsten carbide tooling can handle challenging new substrates, including advanced composites or flexible PCBs.
- Increased Automation: Long-lasting wear parts integrate seamlessly with automated systems, enhancing productivity in high-speed assembly lines.
- Future-Ready Manufacturing: Investing in durable tooling ensures companies can accommodate future changes without frequent reinvestments.
Selecting a Trusted Supplier and Ensuring Quality Control
To fully capitalize on tungsten carbide’s advantages, partner with a reliable supplier that prioritizes quality assurance, technical support, and customization.
Details:
- Quality Certifications: Reputable suppliers provide documentation verifying material authenticity and adherence to industry standards.
- Technical Consultation: Expert guidance on carbide grades, coatings, and geometries ensures optimal performance in unique manufacturing processes.
- After-Sales Support: Ongoing assistance with tool reconditioning, maintenance advice, and performance optimization helps maximize returns on investment.
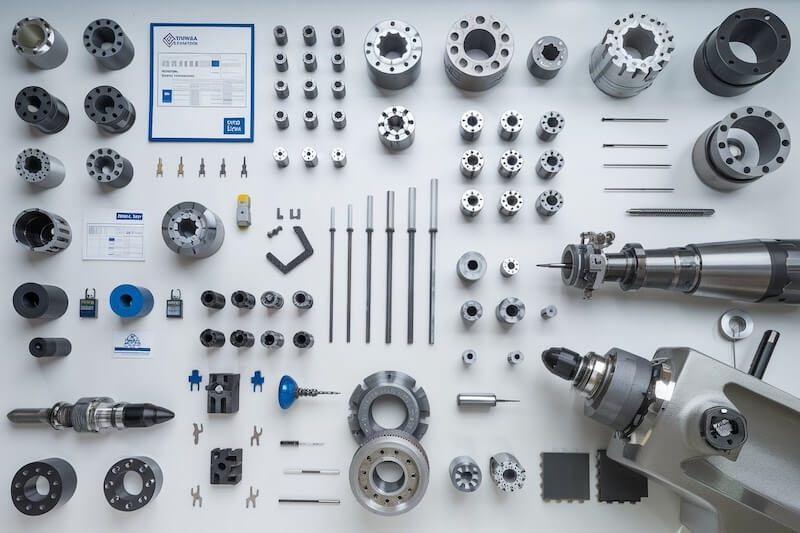
Conclusion
In the rapidly advancing field of electronics manufacturing, adopting tungsten carbide wear parts is more than a product upgrade—it’s a strategic move.
By delivering unparalleled hardness, wear resistance, and consistency, tungsten carbide components help electronics manufacturers streamline production, enhance product quality, and confidently face future challenges.
Decision-makers who invest in tungsten carbide tooling stand to gain a competitive edge, ensuring their companies remain at the forefront of innovation and efficiency in the global electronics market.
Quick and easy: Enter your specifications and get a quote in one business day