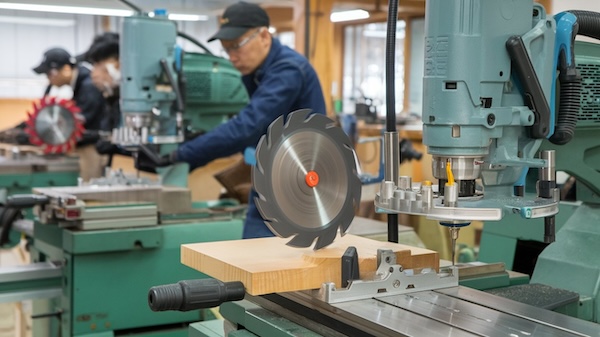
Woodworking Carbide Tooling
Retop is aimed at decision-makers in the woodworking industry. It provides an in-depth understanding of tungsten carbide wear parts, including their advantages, their suitability for various woodworking applications, and why they stand apart from conventional materials. By exploring their properties, comparing alternatives, and highlighting long-term benefits, we will help industry leaders appreciate why investing in tungsten carbide wear parts is a strategic move.
Quick and easy: Enter your specifications and get a quote in one business day
Table of Contents
Expertise in Woodworking Tungsten Carbide Tooling
Retop Carbide’ specialty woodworking tooling is trusted and used by the manufacturing leaders in the industry.
Types of Battery Tooling
- Saw blades and router bits
- Planer and jointer knives
- Drill bits and boring tools
- Tool holders and guides
- Router bits
- Saw teeth
- Planer blades
- Other
Introduction: The Growing Demands of Modern Woodworking
Today’s woodworking operations involve higher production volumes, tighter tolerances, and frequent interaction with abrasive materials. Traditional wear parts often falter under these pressures, leading to shorter tool life, increased downtime, and compromised product quality. Tungsten carbide emerges as a solution that meets modern demands, enhancing both efficiency and end-product consistency.
Details:
- Complex Operations: Intricate designs and diverse wood species require robust and adaptable tooling.
- Continuous Production: Longer production runs necessitate wear parts that endure heavy, sustained workloads.
- Competitive Market: Companies must leverage high-quality wear parts to maintain a competitive edge.
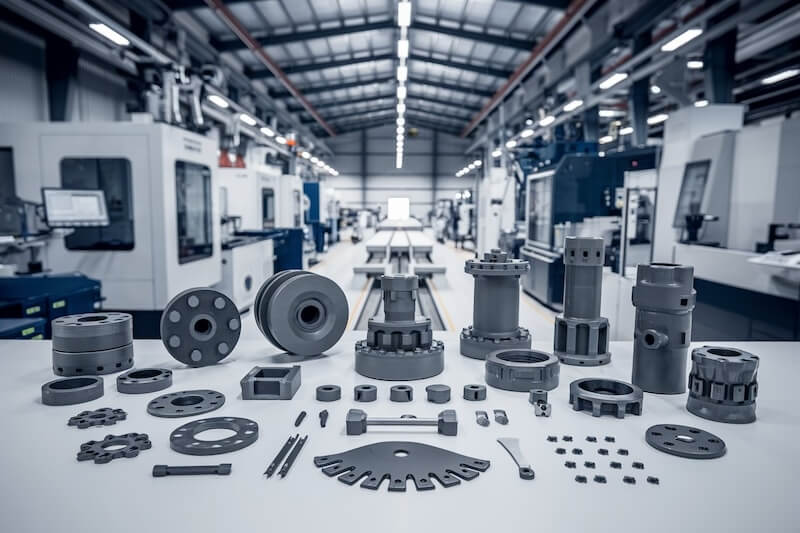
Understanding Tungsten Carbide: Composition and Key Properties
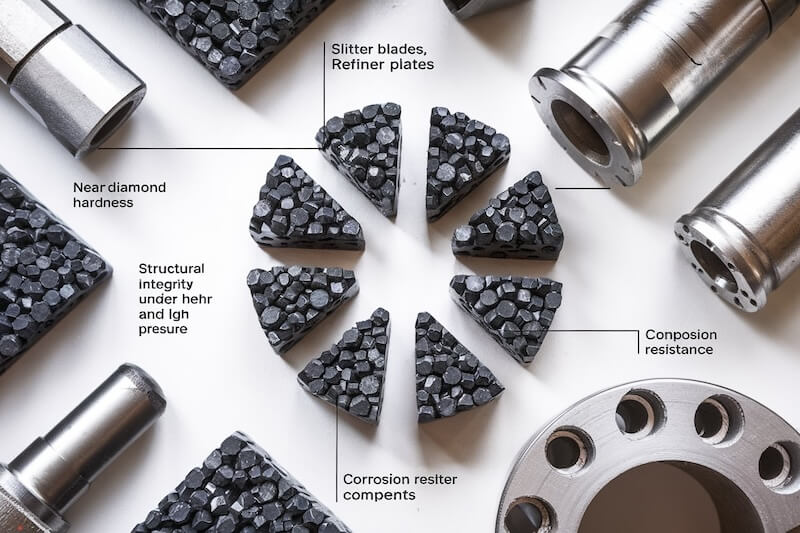
Tungsten carbide is formed by combining tungsten carbide powder with a metallic binder (often cobalt), resulting in a material of near-diamond hardness and exceptional toughness. This composition enables superior performance in challenging woodworking environments.
Details:
- High Hardness: Retains sharp edges longer, ensuring clean, precise cuts.
- Thermal Stability: Withstands heat generated during high-speed cutting without losing integrity.
- Dimensional Stability: Maintains tight tolerances over extended production cycles, improving quality and consistency.
Types of Tungsten Carbide Wear Parts for Woodworking Equipment
Tungsten carbide can be integrated into a wide range of wear components throughout the woodworking production line, each delivering enhanced durability and performance.
Details:
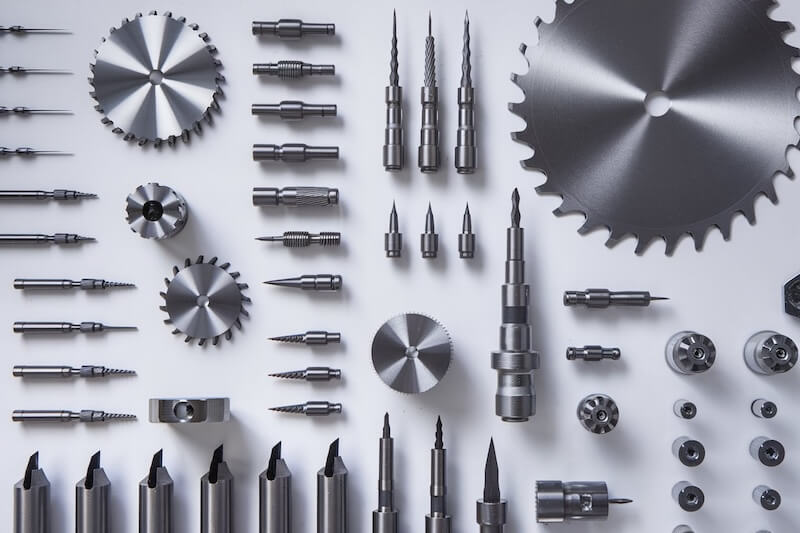
Saw Blades and Router Bits
Carbide-tipped cutting edges produce smoother finishes and require fewer sharpenings.

Planer and Jointer Knives
Longer-lasting carbide knives maintain precision cutting surfaces for a uniform wood finish.
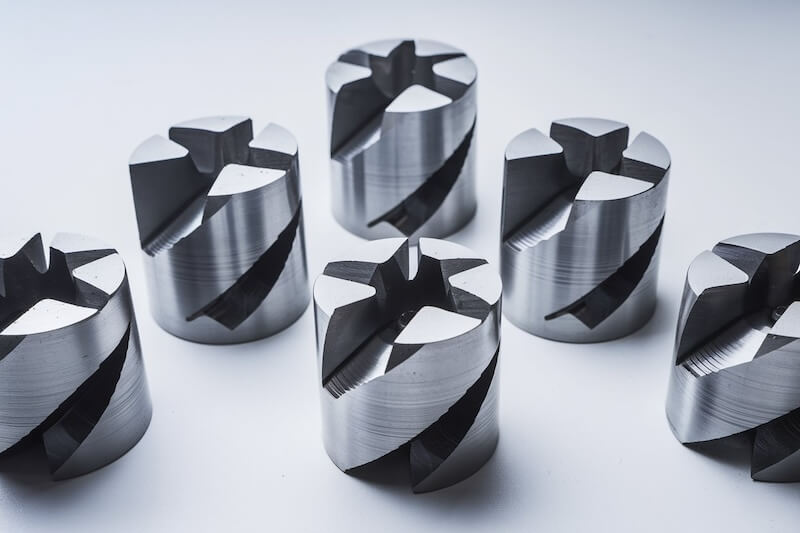
Drill Bits and Boring Tools
Carbide bits withstand dense hardwoods and composite materials without premature dulling.
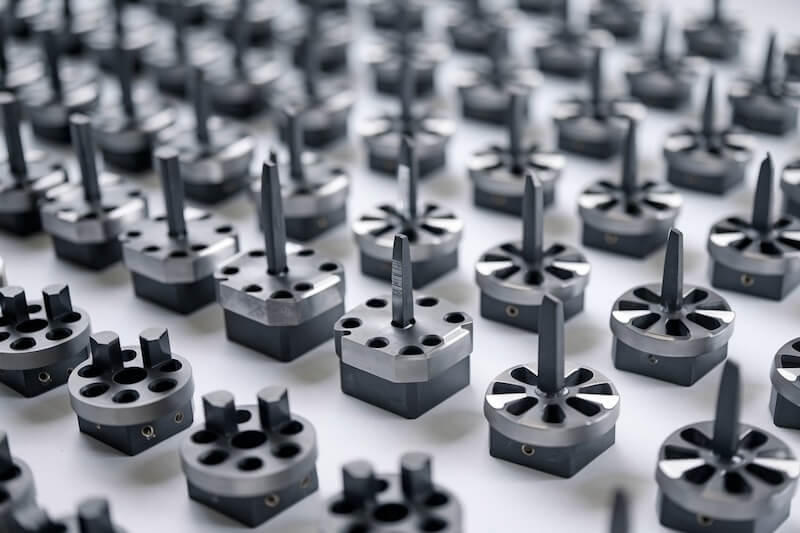
Tool Holders and Guides
Carbide inserts reduce vibration and improve tool stability, ensuring cleaner and more accurate cutting operations.
Quick and easy: Enter your specifications and get a quote in one business day
Comparing Tungsten Carbide to Other Materials
While tool steel, high-speed steel (HSS), and coated alternatives have traditionally been used in woodworking, tungsten carbide often delivers superior longevity, precision, and reliability.
Details:
- Versus Tool Steel: Tungsten carbide’s greater hardness reduces wear, resulting in fewer replacements and less downtime.
- Versus HSS: Higher cutting speeds and feed rates are achievable with carbide tools, boosting productivity without compromising quality.
- Versus Coated Alloys: Tungsten carbide’s properties run throughout its structure, ensuring sustained performance once coatings wear off.

Operational Advantages: Efficiency, Precision, and Product Quality
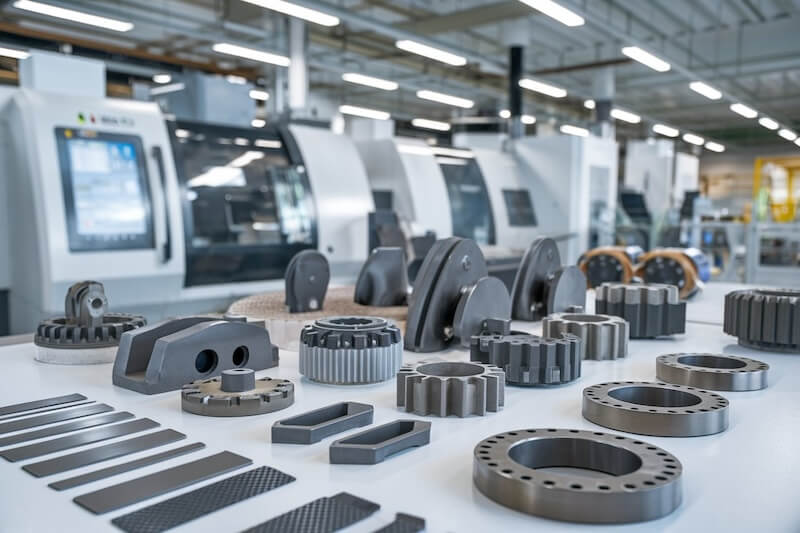
Adopting tungsten carbide wear parts results in tangible operational improvements that directly impact the bottom line and customer satisfaction.
Details:
- Extended Tool Life: Longer intervals between tool changes minimize interruptions, maximizing output and reducing costs.
- Consistent Cutting Edges: Precision edges improve finish quality, reducing sanding, rework, or additional processing steps.
- Higher Throughput: With stable tool geometry and fewer tool adjustments, woodworking lines can run faster and more consistently.
Cost Savings and Return on Investment
Although tungsten carbide wear parts may carry a higher upfront cost, the long-term financial benefits justify the investment through reduced maintenance, lower scrap rates, and improved operational efficiency.
Details:
- Reduced Tool Purchases: Longer tool life means fewer new tools over time, cutting procurement expenses.
- Minimized Labor Costs: Operators spend less time changing tools and making adjustments, raising productivity.
- Decreased Material Waste: Stable, accurate cutting reduces defects and scrap, protecting profit margins.
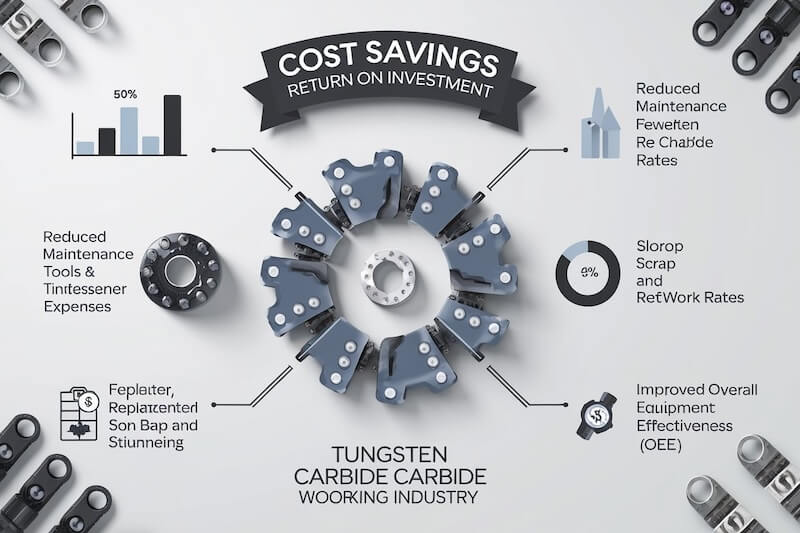
Versatility Across Wood Types and Composites
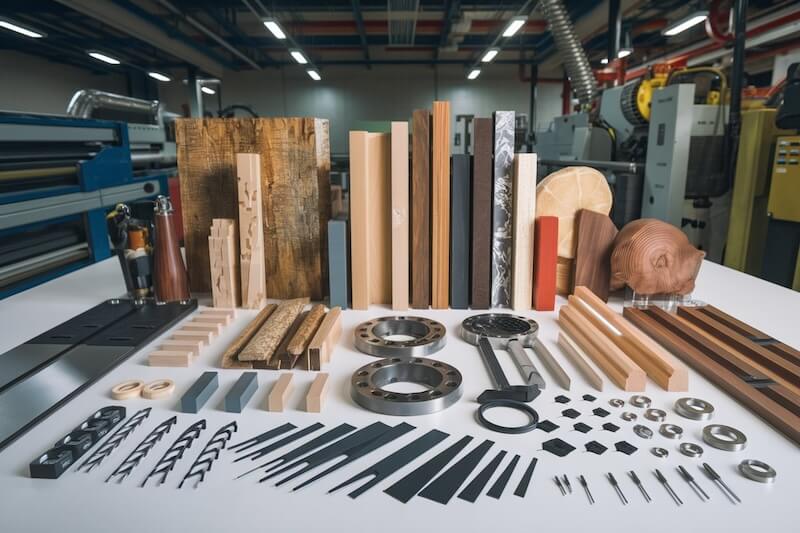
The woodworking industry deals with a range of materials—from softwoods and hardwoods to plywoods, MDF, and exotic species. Tungsten carbide’s versatility ensures it can handle these diverse materials with ease.
Details:
- Hardwoods and Composites: Carbide tools maintain sharpness and edge retention even in abrasive or resin-filled materials.
- Flexible Production: The same carbide tool setups can process multiple wood varieties without compromising tool life or quality.
- Future-Ready: As new engineered wood products emerge, tungsten carbide’s adaptability ensures a seamless transition without frequent tooling changes.
Selecting a Reputable Supplier and Ensuring Quality Assurance
To fully leverage tungsten carbide wear parts, partner with a supplier that emphasizes quality control, technical expertise, and after-sales support.
Details:
- Material Certifications: Reliable suppliers offer detailed specifications and test reports, assuring buyers of consistent quality.
- Technical Guidance: Expert advice on carbide grades, cutting geometries, and tool maintenance ensures optimal performance.
- Ongoing Support: Services like tool reconditioning, maintenance training, and quick replacements guarantee long-term success.
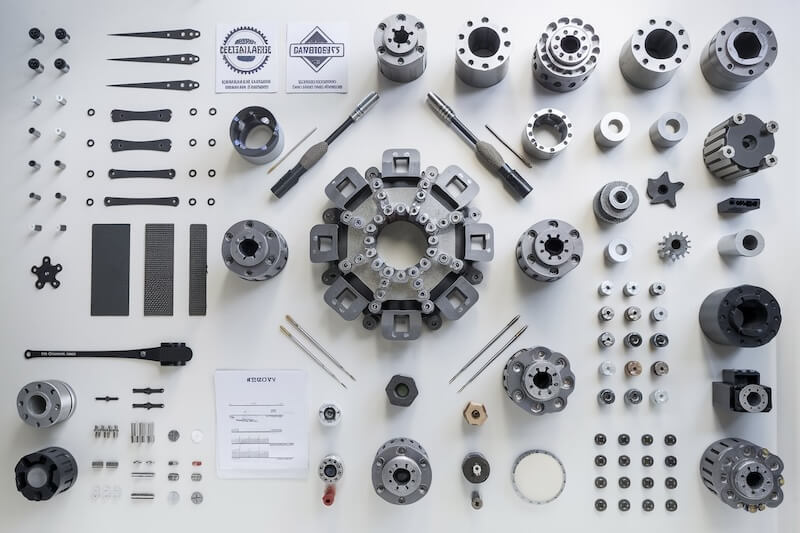
Conclusion
In a woodworking industry where efficiency, quality, and cost management are paramount, tungsten carbide wear parts stand as a strategic upgrade.
By embracing carbide-tipped blades, knives, bits, and tool holders, decision-makers can significantly reduce downtime, improve finished product quality, and lower operational expenses.
Investing in tungsten carbide wear parts is more than a tooling choice—it’s a pathway to sustained productivity, enhanced customer satisfaction, and a competitive position in today’s demanding woodworking market.
Quick and easy: Enter your specifications and get a quote in one business day