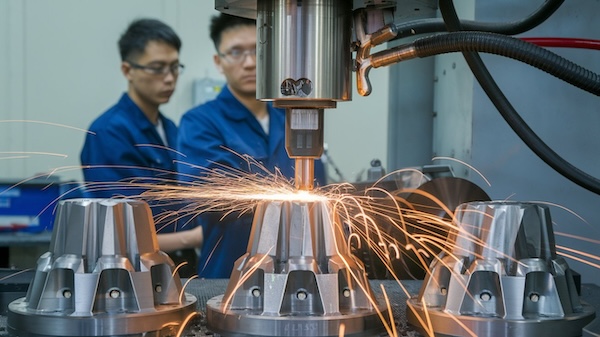
E.D.M. Capabilities
Retop collaborates with tungsten carbide industry partners to enhance electrical discharge machining (EDM) expertise by thoroughly exploring principles, technologies, and quality benchmarks, enabling the production of tungsten carbide tools that meet the highest quality standards..
Quick and easy: Enter your specifications and get a quote in one business day
Table of Contents
Expertise in Electrical Discharge Machining
Retop Carbide has an excellent reputation as a quality source for EDM Capabilities of Tungsten Carbide and Tool Steels.
EDM Capabilities
- Wire EDM
- RAM EDM
Understanding the Fundamentals of EDM on Tungsten Carbide
Mastering EDM begins with a solid grasp of how this non-traditional machining process interacts with tungsten carbide’s properties.
Details:
- EDM Principle: Electrical sparks between an electrode and the tungsten carbide workpiece erode material at a controlled rate, bypassing the need for mechanical cutting forces.
- Material Considerations: Tungsten carbide’s high hardness and unique microstructure influence spark generation and electrode wear, requiring refined parameter settings.
- Thermal and Electrical Conductivity: Understanding tungsten carbide’s relatively high thermal conductivity and how it affects heat dissipation helps prevent damage and ensures optimal removal rates.
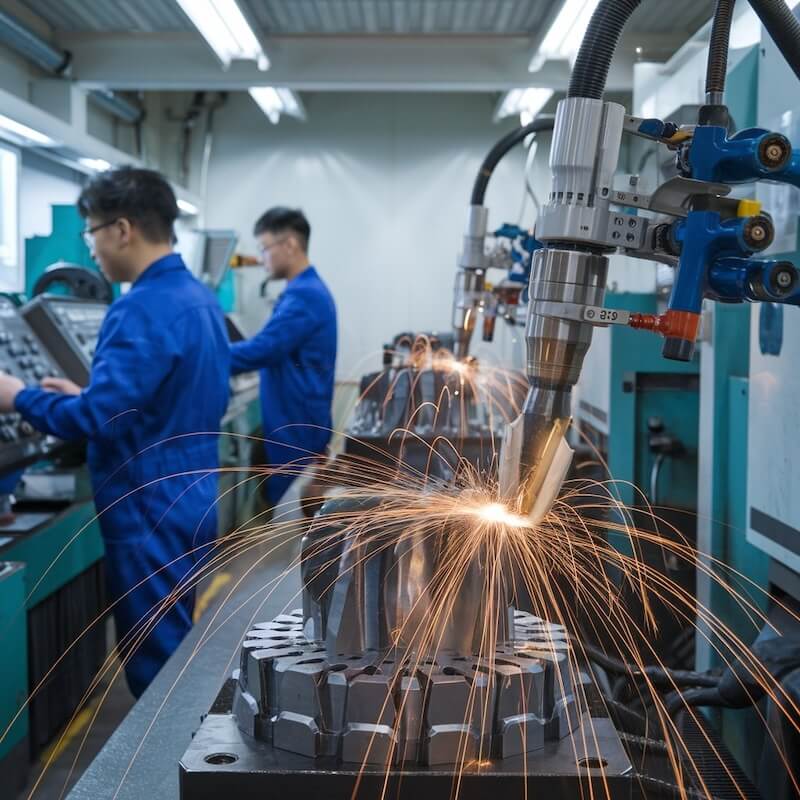
Selecting Suitable EDM Equipment and Electrodes
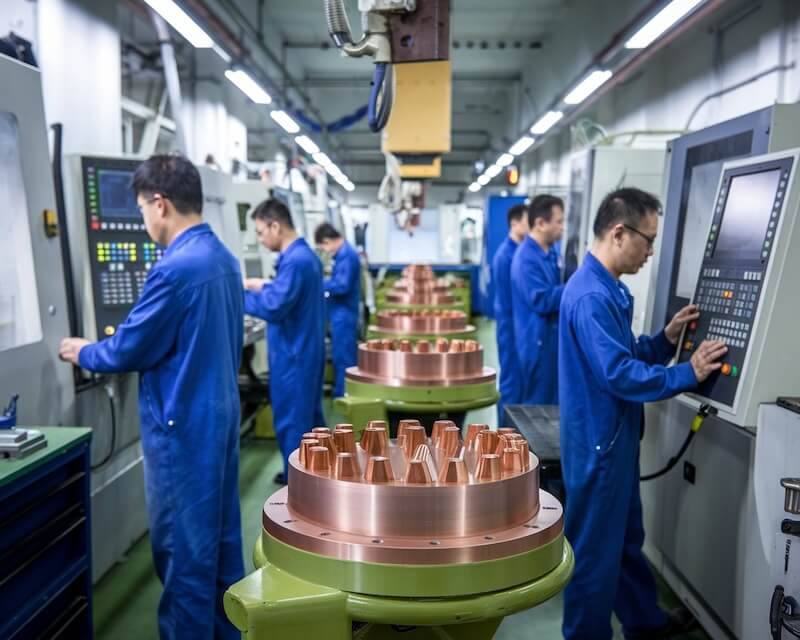
Equipment choice and electrode material significantly impact machining accuracy, surface finish, and productivity.
Details:
- Machine Quality and Rigidity: A stable, high-precision EDM machine with robust CNC controls and fine resolution capabilities ensures repeatable, fine-tolerance results.
- Electrode Materials: While copper and brass are common, switching to copper-tungsten or graphite electrodes may reduce electrode wear and improve accuracy, particularly with tough tungsten carbide grades.
- Tooling and Fixturing: Custom fixtures that securely hold complex shapes and maintain consistent electrode-workpiece gaps are critical to achieving consistent erosion patterns and final dimensions.
Optimizing EDM Parameters for Controlled Material Removal
Professional-level EDM involves skillfully adjusting parameters to achieve a balanced combination of machining speed, accuracy, and surface quality.
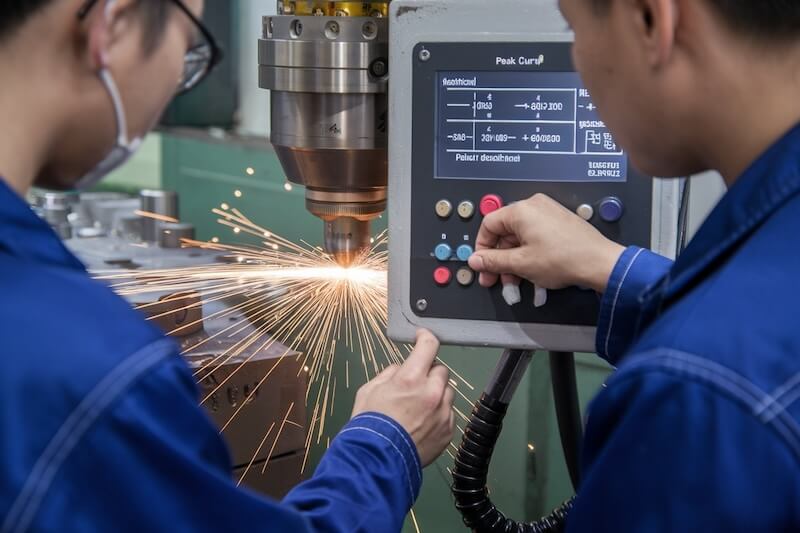
Peak Current and Pulse Duration
Fine-tuning these parameters controls spark energy and penetration depth, influencing removal rates and potential heat-affected zones.
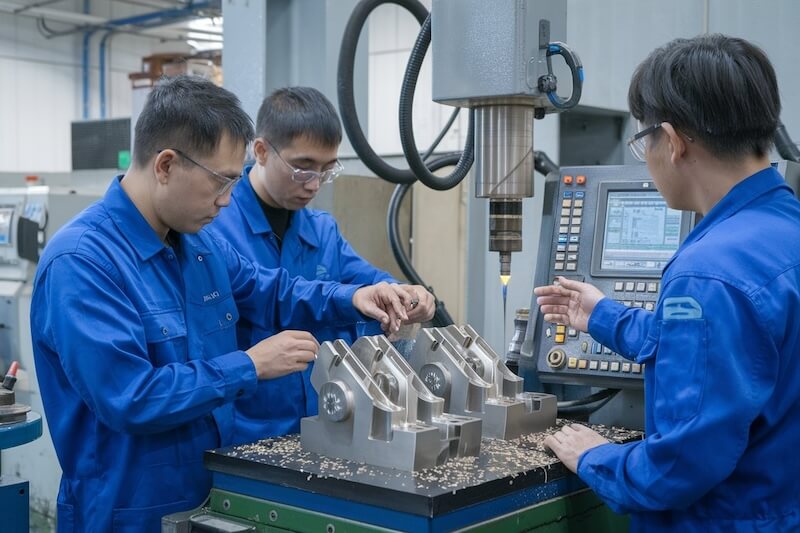
Off-Time and Duty Cycle
Proper off-time settings allow dielectric fluid to flush away debris and cool the workpiece, preventing micro-cracks and uneven erosion.

Adaptive Control Systems
Advanced EDM units feature adaptive controls that automatically adjust parameters in real-time, enhancing consistency and reducing trial-and-error efforts.
Quick and easy: Enter your specifications and get a quote in one business day
Managing Thermal Effects and Minimizing Surface Damage
Professional tungsten carbide EDM demands strategies that address heat build-up, micro-cracking, and residual stresses.
Details:
- Dielectric Fluid Selection: High-quality dielectric fluids with excellent flushing capabilities help remove debris, dissipate heat, and maintain consistent spark conditions.
- Controlled Sparking Zones: By carefully selecting electrode paths and overcuts, manufacturers can distribute thermal loads evenly, mitigating localized overheating.
- Gentle Finishing Stages: Using lower energy sparks in finishing passes refines surface integrity and reduces the risk of micro-cracks or thermal damage.
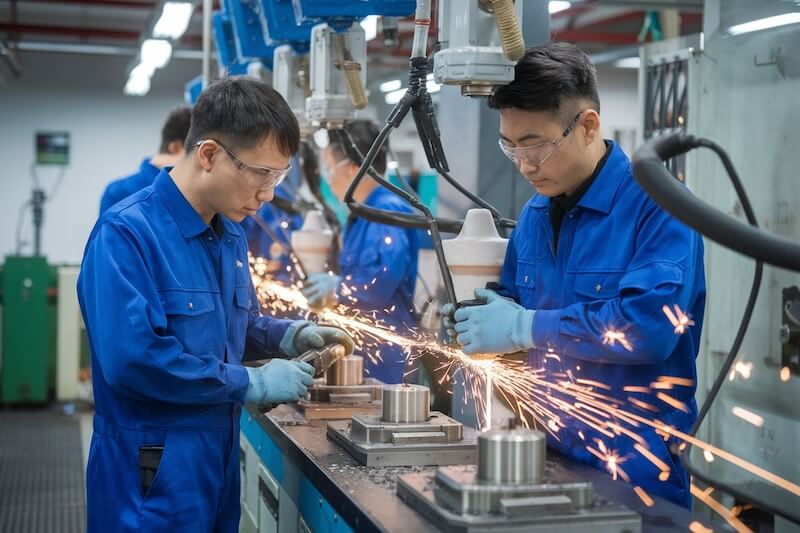
Achieving Tight Tolerances and Intricate Geometries
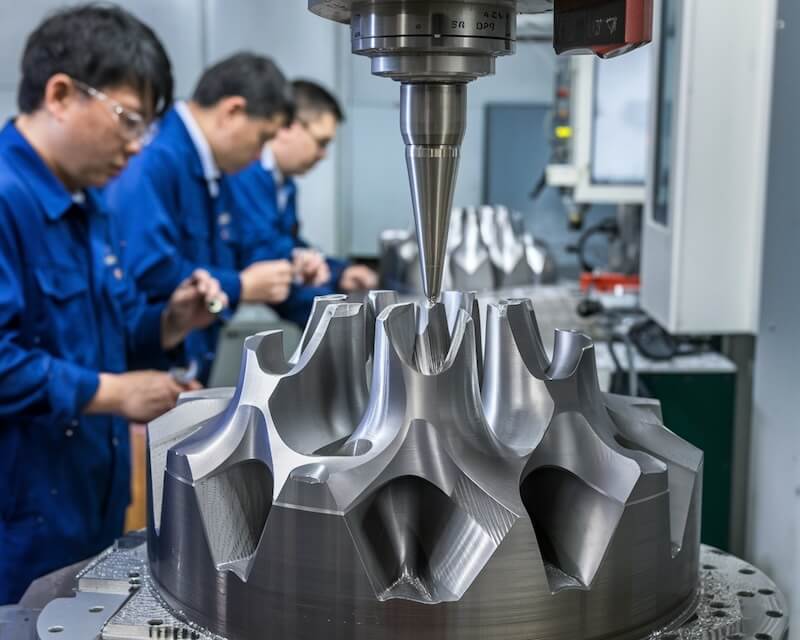
EDM’s strength lies in producing complex shapes, but maintaining precision demands meticulous attention to detail.
Details:
- Step-by-Step Machining: Employing roughing, semi-finishing, and finishing passes ensures a gradual approach to tight tolerances, reducing errors and electrode wear.
- Complex Geometry Handling: EDM can produce sharp corners, thin walls, and intricate cavities that conventional machining struggles with, provided parameters and electrode designs are carefully optimized.
- Dimensional Stability: Consistent alignment checks and real-time monitoring systems help maintain shape fidelity and dimensional integrity throughout the machining process.
Surface Finish Enhancement and Post-EDM Treatments
A professional approach extends beyond erosion, focusing on finishing techniques that elevate component quality.
Details:
- Surface Refinement: Fine EDM settings reduce surface roughness, but additional lapping, honing, or polishing can achieve mirror finishes vital for high-performance components.
- Stress Relief Treatments: Secondary heat treatments or controlled cooling processes alleviate internal stresses induced by EDM, improving long-term part stability.
- Coating Compatibility: Smooth, stress-free surfaces are often better candidates for subsequent coatings or surface treatments, enhancing wear resistance and overall part performance.
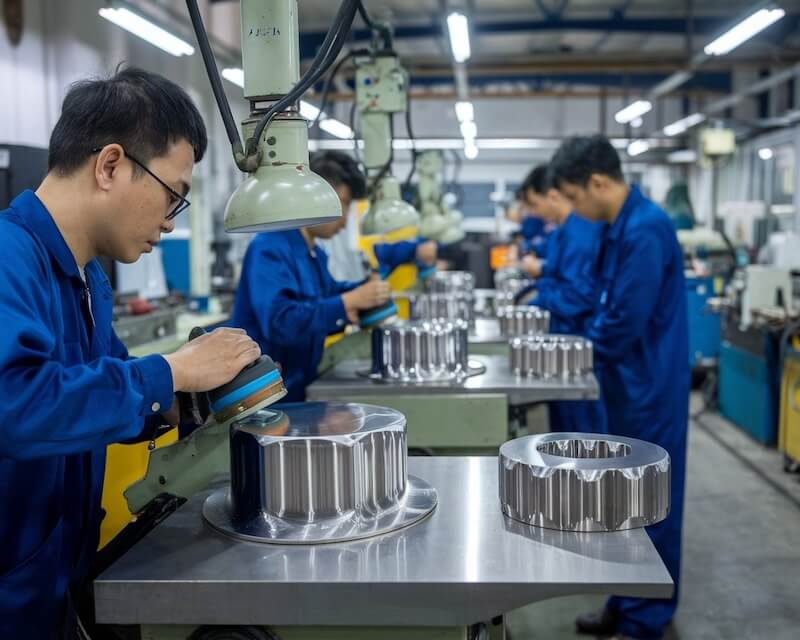
Quality Assurance, Inspection, and Testing
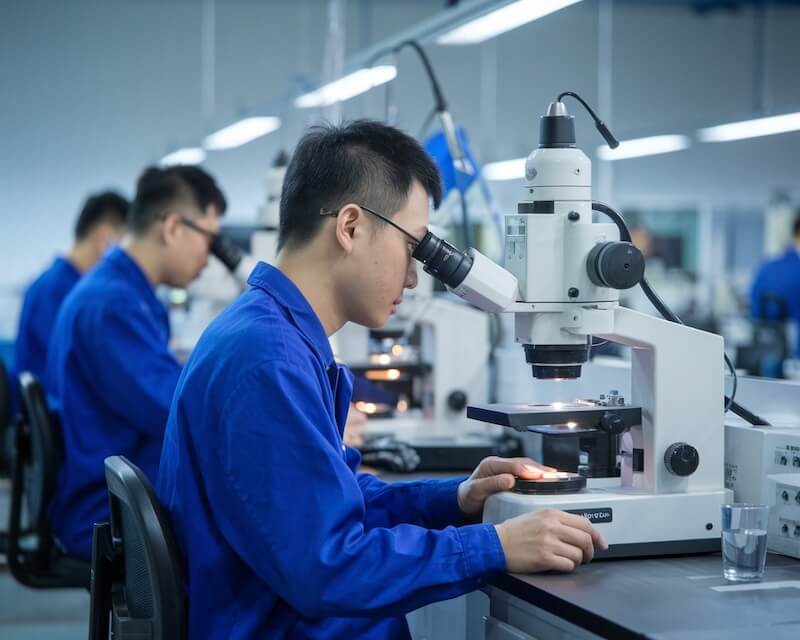
Rigorous quality control confirms that every tungsten carbide component meets professional standards.
Details:
- Metallurgical Analysis: Microscopic inspections ensure the EDM process hasn’t induced unwanted micro-structural changes or porosity.
- Dimensional Verification: High-precision measuring tools like CMMs or optical scanners confirm compliance with CAD specifications.
- Surface Integrity Checks: Profilometers and optical interferometers assess surface roughness, ensuring the desired finish and functional properties are achieved.
Continuous Improvement and Advanced Techniques
Staying ahead in a competitive market requires embracing innovations in EDM technology, techniques, and best practices.
Details:
- Adaptive EDM Control Software: Next-generation EDM systems analyze cutting conditions dynamically, improving efficiency and quality.
- Material Innovations: Ongoing research into new electrode materials, dielectric formulations, and tungsten carbide grades can unlock superior results.
- Collaborative Knowledge Sharing: Engaging with equipment manufacturers, industry forums, and technical workshops ensures continuous learning and mastery of evolving EDM techniques.
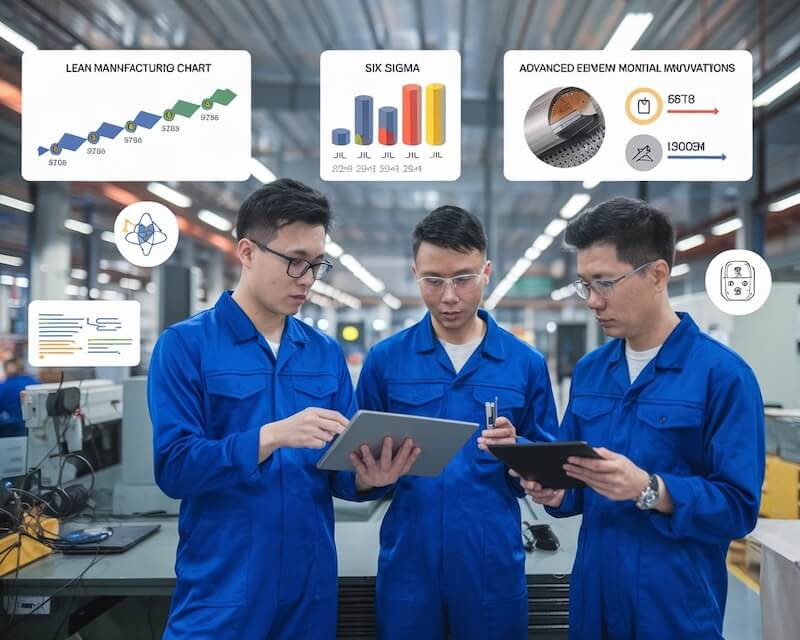
Conclusion
Professional-level electrical discharge machining of tungsten carbide is an intricate interplay of material science, parameter optimization, meticulous setup, and rigorous quality checks.
By fully understanding the fundamental EDM principles, selecting the right equipment and electrodes, fine-tuning process parameters, and embracing continuous improvement, tungsten carbide manufacturers can deliver exceptional results.
As the industry’s expectations evolve and competition grows fiercer, refining EDM expertise not only meets current market demands but also sets a foundation for future innovations.
Quick and easy: Enter your specifications and get a quote in one business day