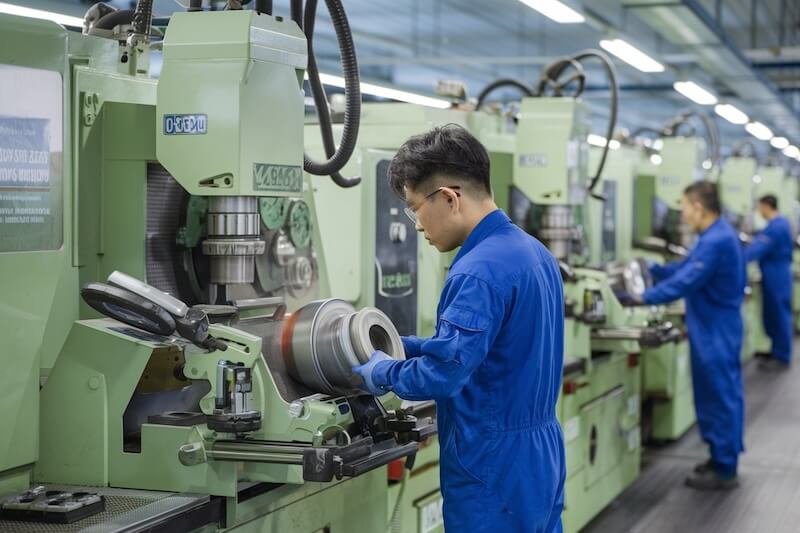
Grinding, Machining and Polishing Capabilities
Retop shares expertise in professional grinding, machining, and polishing of tungsten carbide by highlighting key principles, advanced techniques, and quality benchmarks. Our goal is to support and uplift fellow tungsten carbide manufacturers, fostering shared growth and helping them enhance their skills and understanding in these processes.
Quick and easy: Enter your specifications and get a quote in one business day
Table of Contents
Expertise in grinding, machining and polishing
Retop Carbide is renowned for its high-quality grinding, machining, and polishing of tungsten carbide, ceramic, and tool steels.
Capabilities
- O.D. Grinding to 12” in Diameter- CNC and Conventional
- I.D. Grinding to 10” in Diameter- CNC and Conventional
- Surface Grinding to 24” Long x 12” Wide
- Thread Grinding of Tungsten Carbide, Ceramic and Tool Steels
- Honing – Horizontal and Vertical
- Polishing / Finishing to 2 Micro Inches
- Lathes – CNC and Conventional
- Milling – CNC and Conventional
- Centerless Grinding
- Single-Sided Lapping
- Induction Coil and Silver Solder Brazing
Understanding Tungsten Carbide’s Material Characteristics
A deep knowledge of tungsten carbide’s microstructure, hardness, and brittleness underpins every decision in the grinding, machining, and polishing process.
Details:
- Composition and Microstructure: Tungsten carbide is a ceramic-metal composite (cermet) with hard WC grains embedded in a metallic binder. Grasping this structure helps operators anticipate how it reacts during machining.
- Hardness and Fracture Resistance: Its high hardness enables exceptional wear resistance, but also challenges traditional cutting tools. Recognizing these properties ensures careful selection of abrasives, tool geometries, and speeds.
- Thermal Conductivity and Stability: Adequate cooling and temperature control during machining are essential because tungsten carbide can tolerate high heat but may experience stress and micro-cracking if improperly handled.
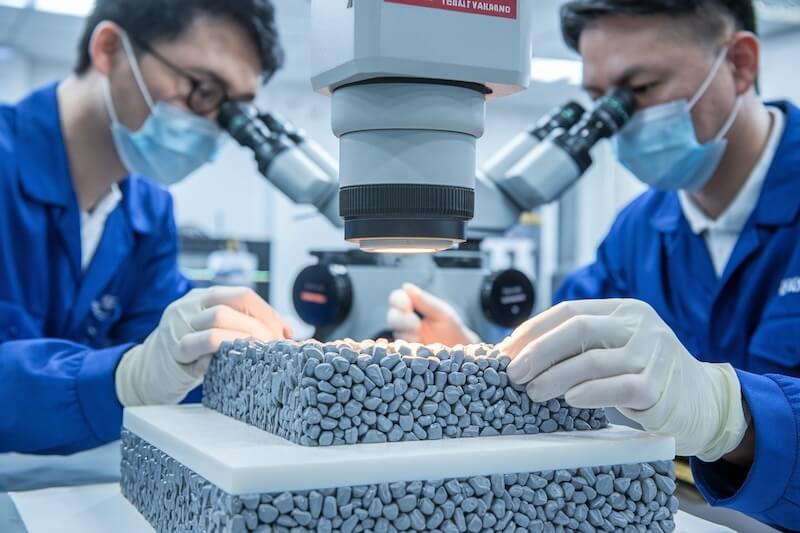
The Role of Proper Machine Selection and Setup
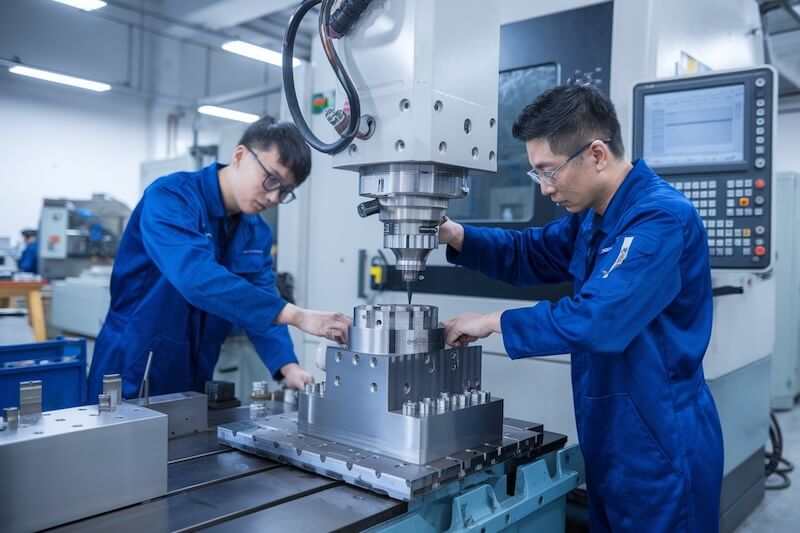
Professional machining of tungsten carbide requires specialized equipment and precise configurations that minimize errors and tool wear.
Details:
- Machine Stiffness and Rigidity: Opt for machines with minimal vibration and robust construction to ensure consistent surface finishes and dimensional accuracy.
- High-Precision CNC Controls: Automated controls and advanced CNC programming enable repeatable results, allowing for complex geometries with tight tolerances.
- Workholding and Fixturing: Secure and stable workholding systems prevent micro-movements that may result in chatter, premature tool wear, and surface defects.
Choosing the Right Grinding Tools and Abrasives
Selecting appropriate grinding wheels and abrasive materials is fundamental to achieving optimal surface quality and productivity in tungsten carbide grinding.
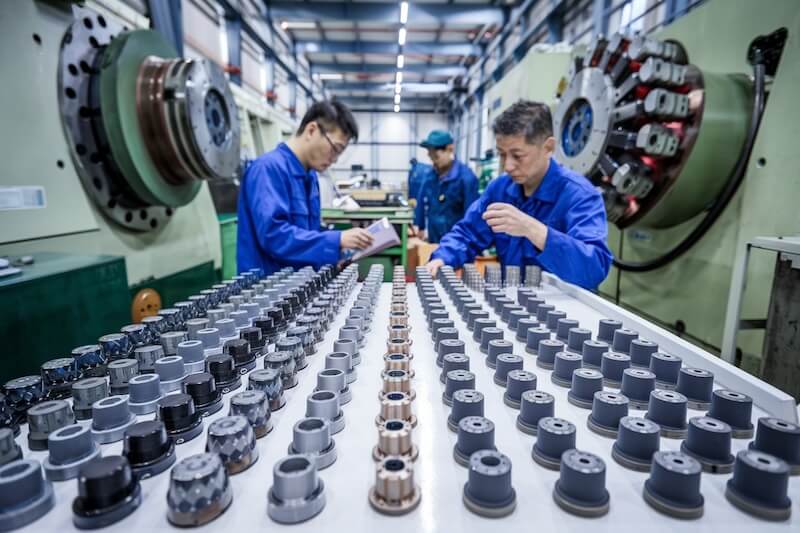
Diamond and CBN Abrasives
Diamond abrasives are typically preferred due to their superior hardness. Cubic boron nitride (CBN) may also be used under certain conditions, especially if specific binder compositions warrant it.
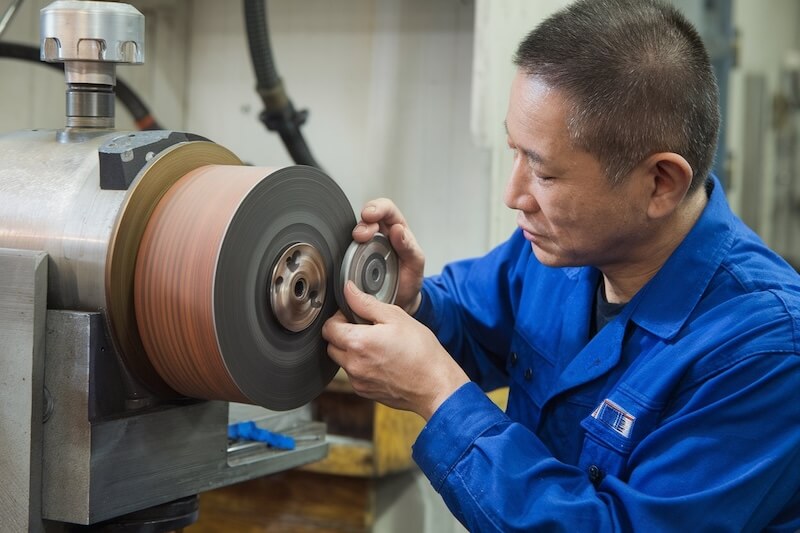
Bond Types and Wheel Profiles
Resin-bonded wheels are common for fine finishes, while metal or vitrified bonds may excel in roughing operations. Matching the wheel’s bond and grit size to the workpiece requirements ensures balanced removal rates and surface integrity.
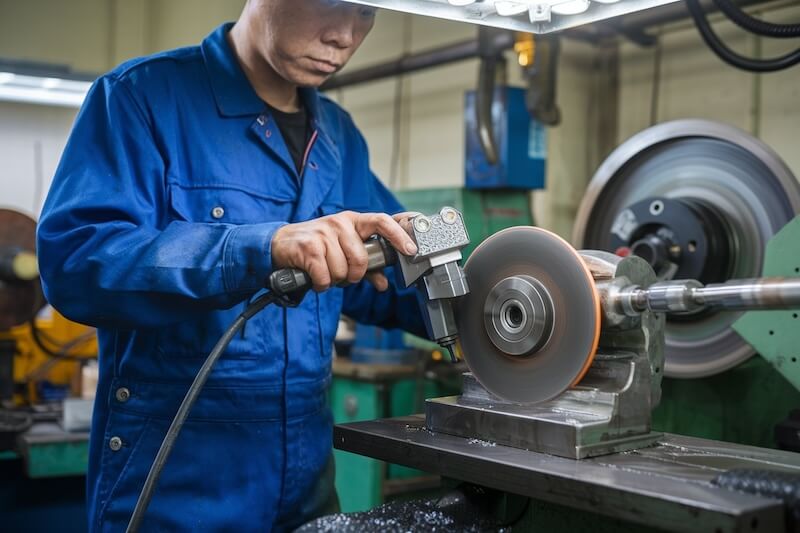
Dressing and Conditioning
Regularly dressing and conditioning the wheel maintains optimal cutting conditions, sharp abrasive edges, and consistent performance.
Quick and easy: Enter your specifications and get a quote in one business day
Optimal Machining Parameters for Efficiency and Quality
Fine-tuning parameters like spindle speed, feed rate, and depth of cut directly influences tool life, surface finish, and production efficiency.
Details:
- Speed and Feed Interplay: Lower cutting speeds often extend tool life, but may reduce productivity. Striking a balance is crucial for both cost-effectiveness and surface quality.
- Depth of Cut Strategy: Gradually reducing the depth of cut in finishing passes produces finer surfaces and tighter tolerances, minimizing residual stresses.
- Coolant and Lubrication: Using high-quality coolants can reduce friction, dissipate heat, and flush away debris, improving tool longevity and part quality.
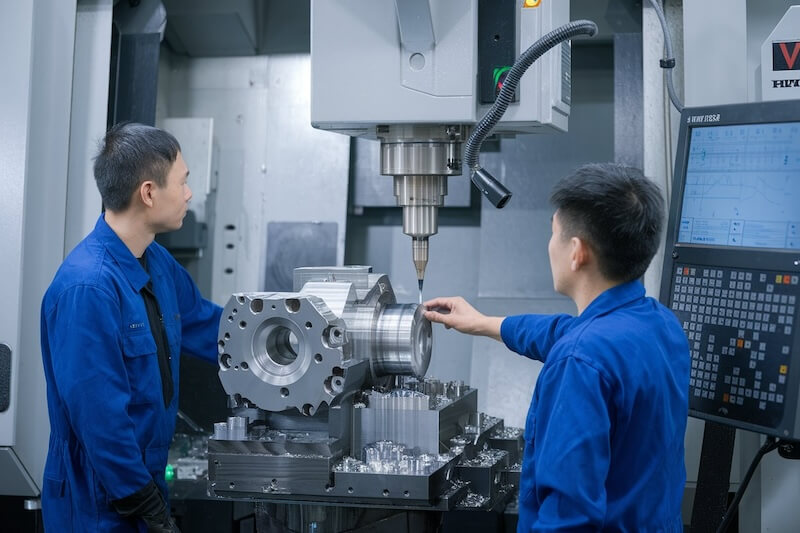
Polishing Techniques for Enhanced Surface Finishes
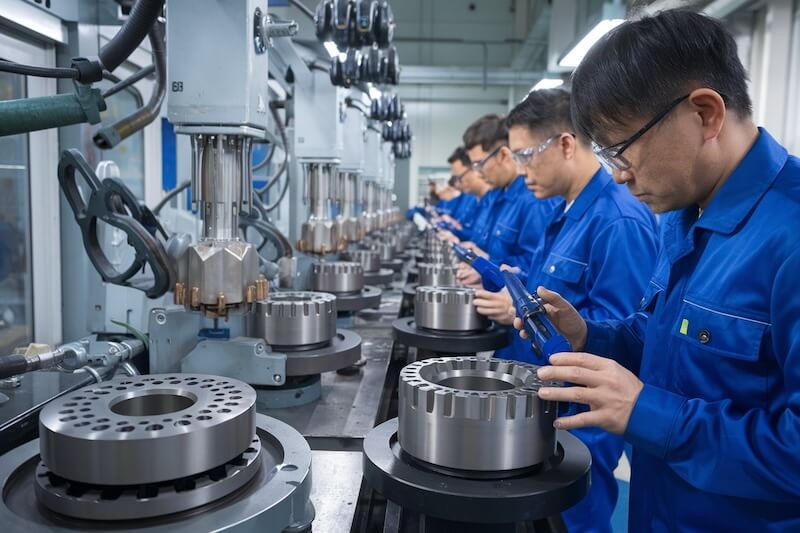
Proper polishing transforms a machined tungsten carbide surface from functional to near-perfect, enhancing performance in wear-intensive applications.
Details:
- Progressive Grit Reduction: Employ a sequence of finer abrasives to gradually refine the surface, starting with a coarser grit and moving to ultra-fine diamond compounds.
- Lapping and Honing: Controlled lapping and honing processes can achieve extremely low surface roughness, essential for components like cutting tools or precision dies.
- Automation and Consistency: Automated polishing equipment maintains uniform pressure and contact patterns, ensuring consistent quality across batches.
Quality Assurance and Inspection Methods
Rigorous testing and inspection validate the success of grinding, machining, and polishing, guaranteeing parts meet or exceed specifications.
Details:
- Metallographic Examination: Microscopic analysis of grain boundaries, binder distribution, and surface integrity ensures no micro-cracks, porosity, or unwanted phase changes have occurred.
- Surface Roughness Measurement: Instruments like profilometers and optical interferometers quantify Ra, Rz, and other metrics, confirming that surfaces meet the target finish.
- Dimensional Metrology: Coordinate measuring machines (CMMs) and laser scanners check tolerances and ensure that components comply with CAD specifications.
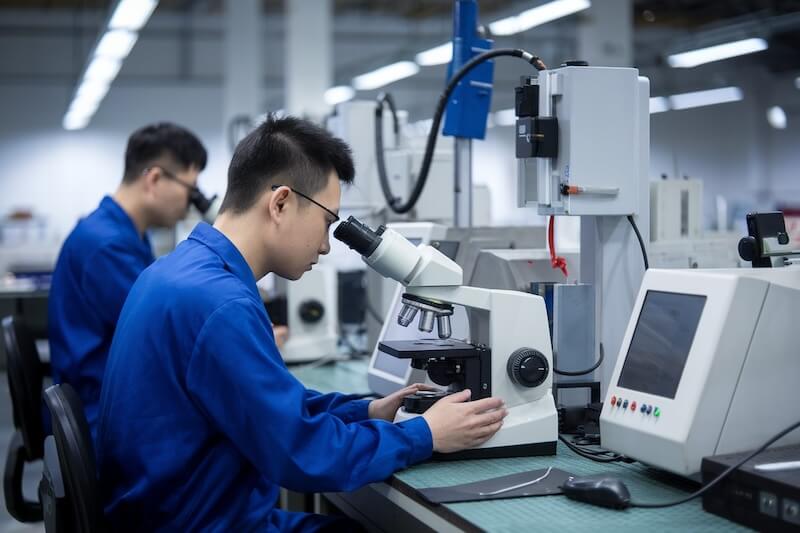
Process Optimization and Continuous Improvement
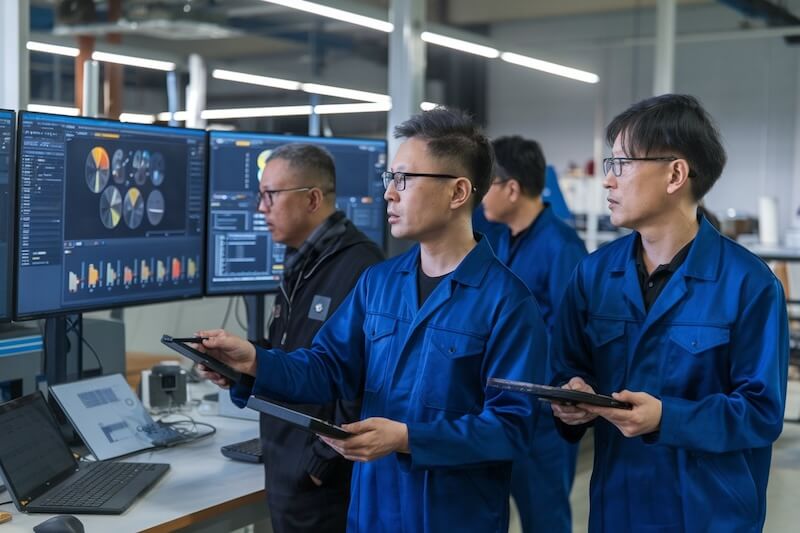
Professional-level manufacturing demands iterative refinements, feedback loops, and R&D efforts aimed at pushing process capabilities forward.
Details:
- Lean Manufacturing Principles: Applying lean and Six Sigma methodologies can help identify inefficiencies, reduce material waste, and shorten cycle times.
- Tool Wear Monitoring and Predictive Maintenance: Tracking wheel wear, tool life, and equipment health prevents quality decline and supports proactive adjustments to parameters or tools.
- Collaboration with Suppliers: Engaging with abrasive suppliers, machine tool OEMs, and coolant manufacturers fosters innovation and ensures access to the latest technological advancements.
Achieving Competitive Advantage Through Professional Processes
By mastering professional grinding, machining, and polishing practices, tungsten carbide manufacturers differentiate themselves and deliver superior value to their clients.
Details:
- Enhanced Product Performance: Superior finishes and tolerances lead to parts that last longer, perform better, and reduce end-user costs.
- Customer Satisfaction and Trust: Consistent quality builds brand reputation, resulting in repeat business and long-term partnerships.
- Staying Ahead of Competitors: Continually improving manufacturing processes in tungsten carbide handling establishes a competitive edge and positions your company as a leader in the industry.
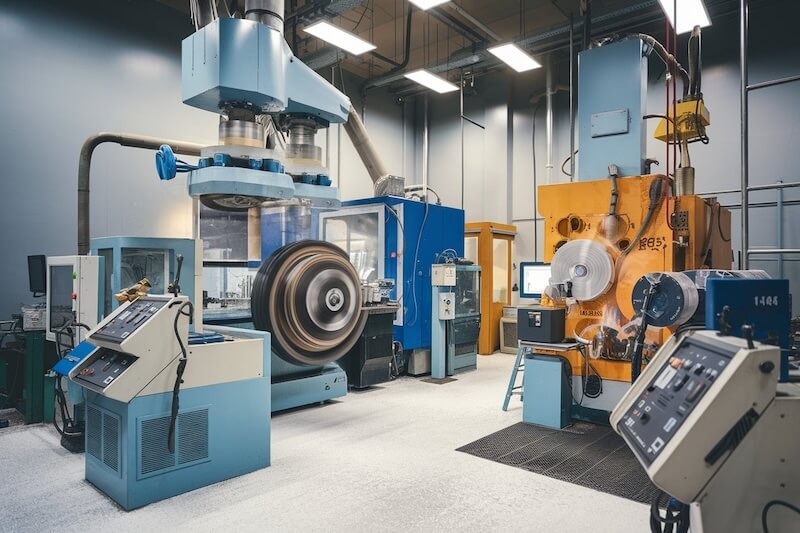
Conclusion
Professional grinding, machining, and polishing of tungsten carbide is not simply a matter of employing the hardest abrasives or the fastest machines.
It’s a holistic approach involving material expertise, machine selection, tool choice, parameter optimization, meticulous polishing techniques, and stringent quality control. By understanding these principles and implementing best practices, manufacturers can elevate their processes to a professional standard.
In doing so, they create tungsten carbide components that are not only dimensionally accurate and long-lasting, but also serve as benchmarks of quality and performance, advancing the industry as a whole.
Quick and easy: Enter your specifications and get a quote in one business day