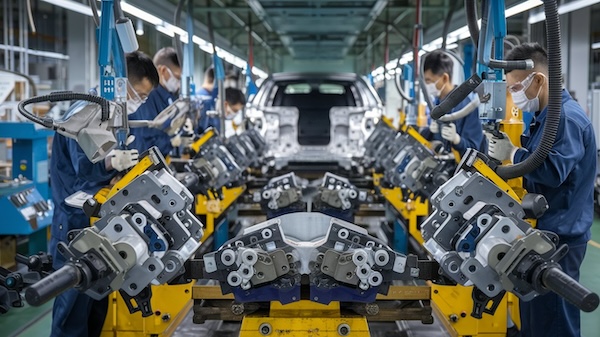
Automotive Carbide tooling
We highlighting how tungsten carbide tools enhance automotive manufacturing. It targets both machine operators who benefit from smoother production workflows and CEOs who are considering strategic investments. The ultimate goal is to demonstrate how switching to tungsten carbide tools—particularly those provided by Retop—leads to better outcomes in quality, cost savings, and overall competitiveness in the automotive industry.
Quick and easy: Enter your specifications and get a quote in one business day
Table of Contents
Expertise in Automotive Tungsten Carbide Cutting Tooling
Retop Carbide specializes in quality automotive carbide tooling for manufacturers making products to be assembled into automobiles across the World.
Types of Automotive Tungsten Carbide Cutting Tools
- Tungsten Carbide Engine and Transmission Cutting Tools
- Large Automotive Die Blanks
- Punch Blanks for the Automotive Industry
- Tungsten Carbide Cutting Tools For Automotive Parts
- High Performance Tungsten Carbide Automotive Parts
Introduction: The Critical Role of Advanced Materials in Automotive Manufacturing
As automotive components grow increasingly complex and precision becomes paramount, material quality in tooling takes center stage. Tungsten carbide stands out as a high-performance option.
Details:
- Rising Standards: The automotive industry demands tighter tolerances, higher speeds, and reliable finishes.
- Complex Parts: Sophisticated components like engine parts, transmission assemblies, and injection systems require robust tools to ensure flawless manufacturing.
- Competitive Edge: Investing in cutting-edge tooling materials can reduce defects, accelerate production, and enhance product performance in a crowded marketplace.
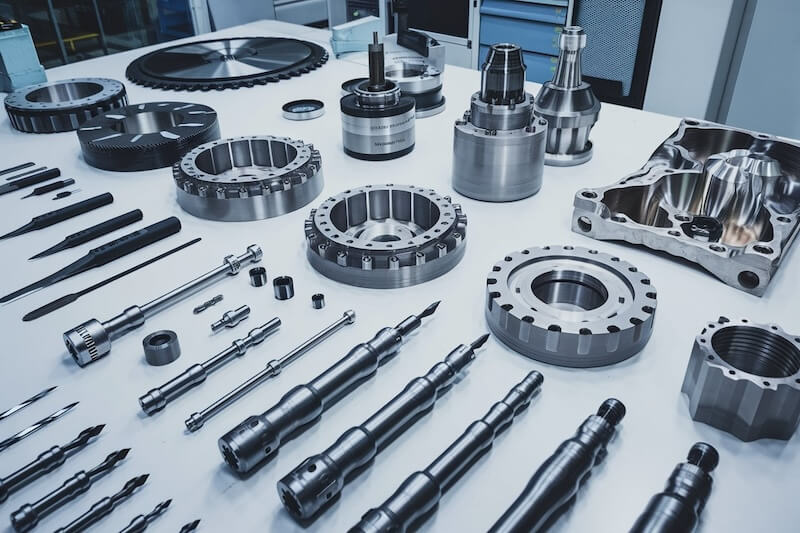
Tungsten Carbide’s Core Properties and Advantages
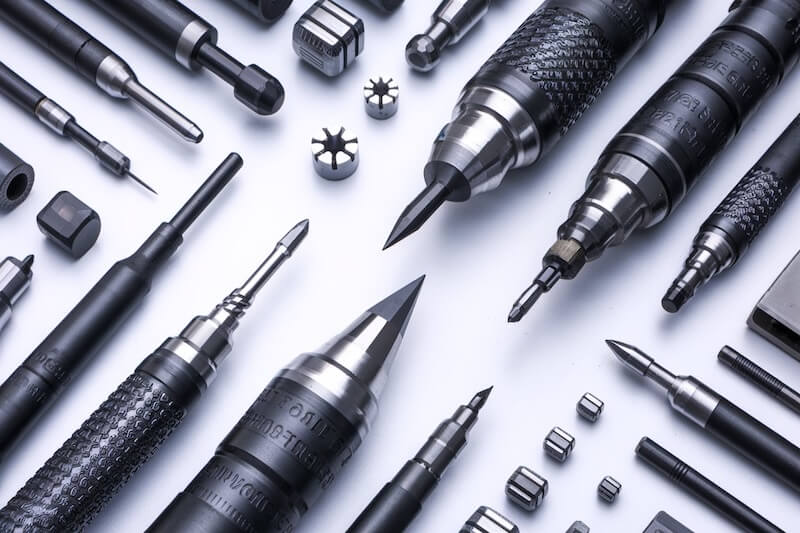
Tungsten carbide’s unique combination of hardness, toughness, and wear resistance makes it ideal for demanding automotive machining operations.
Details:
- Exceptional Hardness: Outperforms traditional steels and standard tool alloys, allowing for high-speed cutting without premature wear.
- Prolonged Tool Life: Reduces downtime related to frequent tool changes and sharpening, increasing shop floor productivity.
- Dimensional Stability: Maintains accurate tool geometry under high pressure and temperature conditions common in automotive applications.
Performance Gains in Critical Automotive Components
Tungsten carbide tools are particularly beneficial in machining high-value automotive parts where precision and durability are non-negotiable.
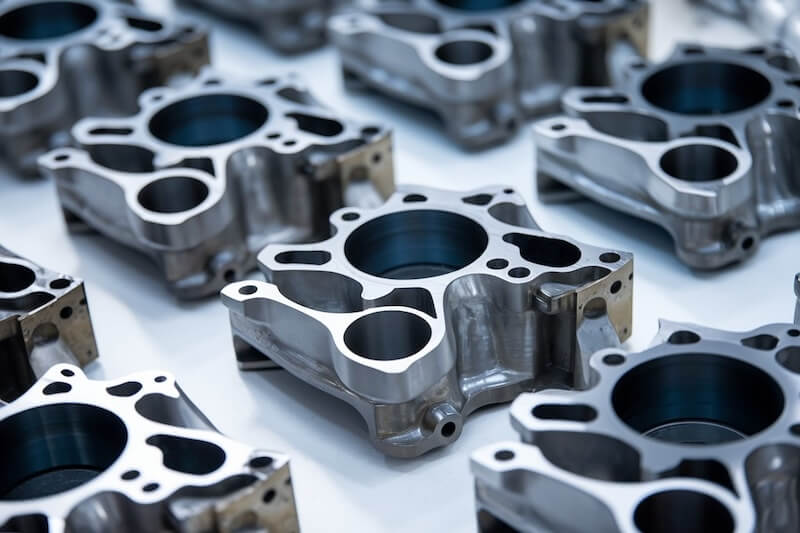
Engine Components
Cylinder heads, crankshafts, and pistons require smooth finishes and consistent dimensional accuracy.
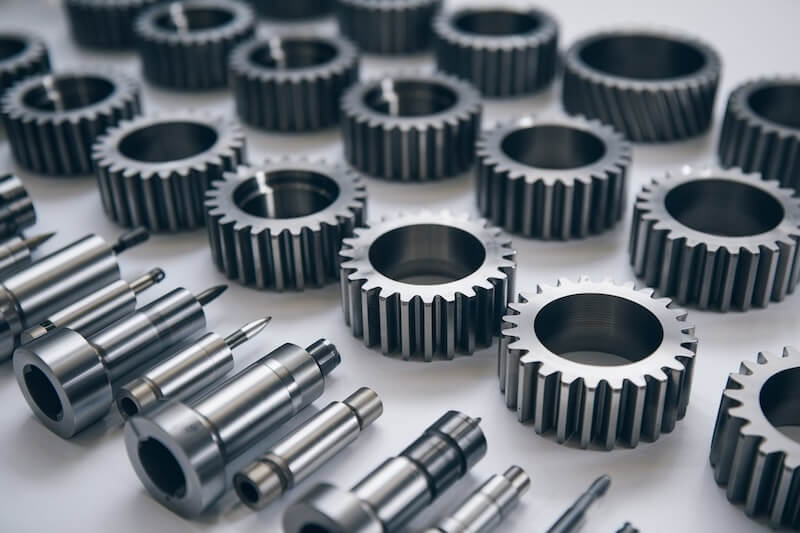
Transmission Systems
Gear machining benefits from sharper, longer-lasting cutting edges that deliver uniform results.
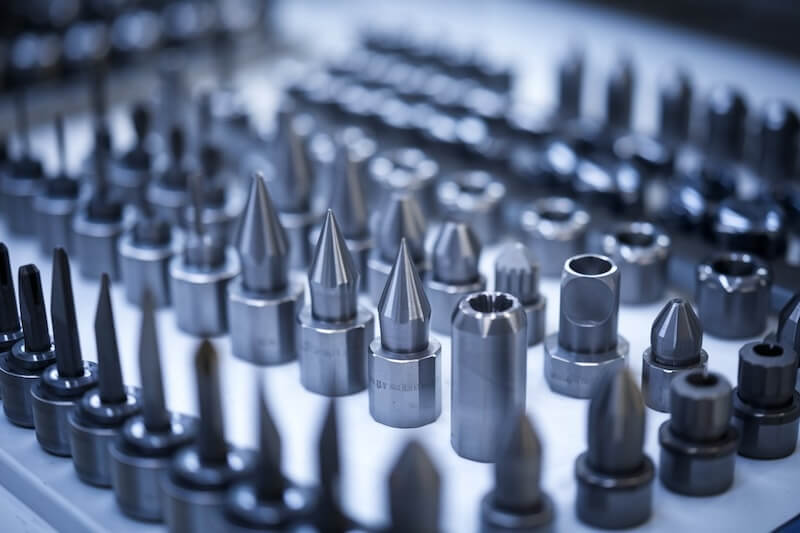
Fuel Injection Systems
High-precision tungsten carbide tools help achieve micron-level tolerances, ensuring efficient fuel delivery and improved vehicle performance.
Quick and easy: Enter your specifications and get a quote in one business day
Operational Efficiency: Lower Downtime and Reduced Maintenance Costs
By extending tool life and maintaining cutting performance over longer production runs, tungsten carbide tools help streamline operations and reduce expenses.
Details:
- Fewer Tool Changes: Minimizes production interruptions and labor costs associated with swapping out worn tools.
- Consistent Performance: Stable cutting geometry reduces rework and scrap rates, enhancing overall efficiency.
- Long-Term Reliability: Durable tools mean less maintenance, fewer emergency repairs, and more predictable production schedules.
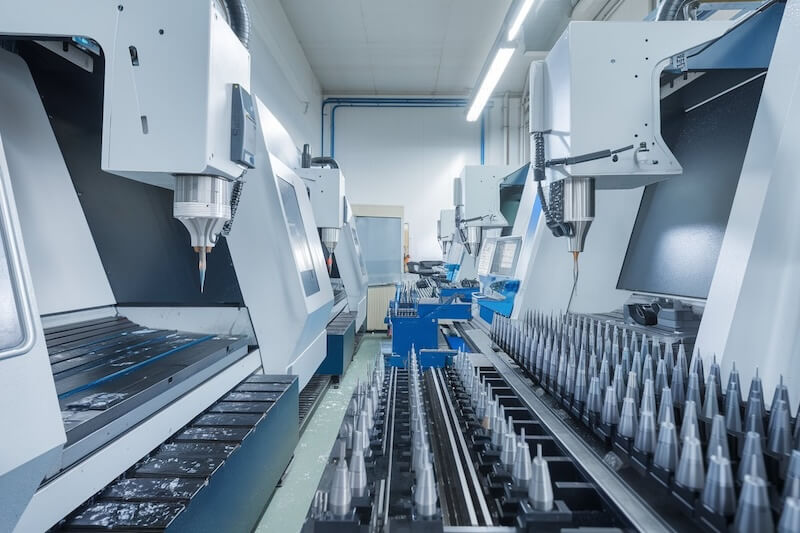
Quality Assurance and Improved Product Reliability
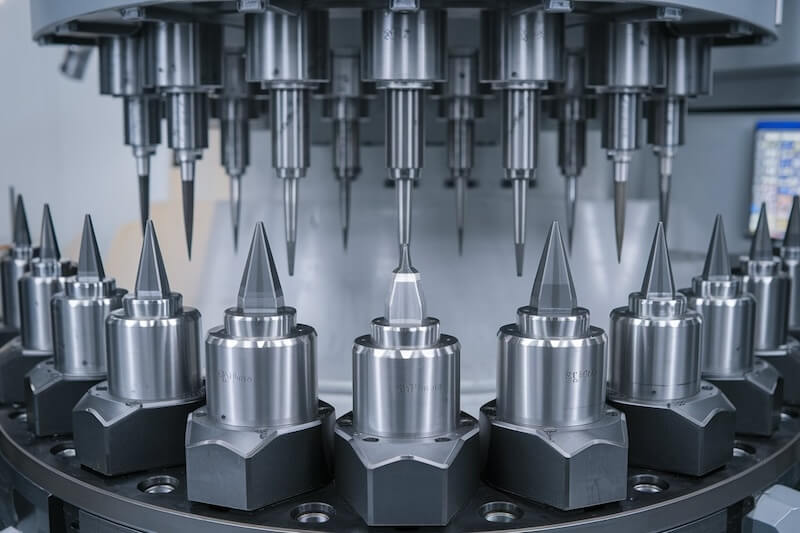
Tungsten carbide ensures that every cut, drill, or grind meets stringent automotive quality benchmarks, resulting in higher-quality end products.
Details:
- Precision Machining: Achieve tight tolerances and consistent part geometry, ensuring components fit and function perfectly.
- Surface Finish Improvement: Superior cutting edges deliver smoother surfaces, enhancing both aesthetic and functional properties of automotive parts.
- Reduced Defects: Fewer dimensional errors and improved repeatability contribute to better overall vehicle reliability and customer satisfaction.
Sustainability and Resource Efficiency
Tungsten carbide tooling supports sustainability efforts by reducing waste, improving tool longevity, and optimizing resource consumption.
Details:
- Less Material Waste: Fewer defective parts mean less raw material is discarded.
- Reduced Energy Use: Efficient machining cycles translate to lower energy consumption on the factory floor.
- Recycling Programs: Many tungsten carbide tools can be reclaimed and reprocessed, further minimizing environmental impact over the product’s lifecycle.
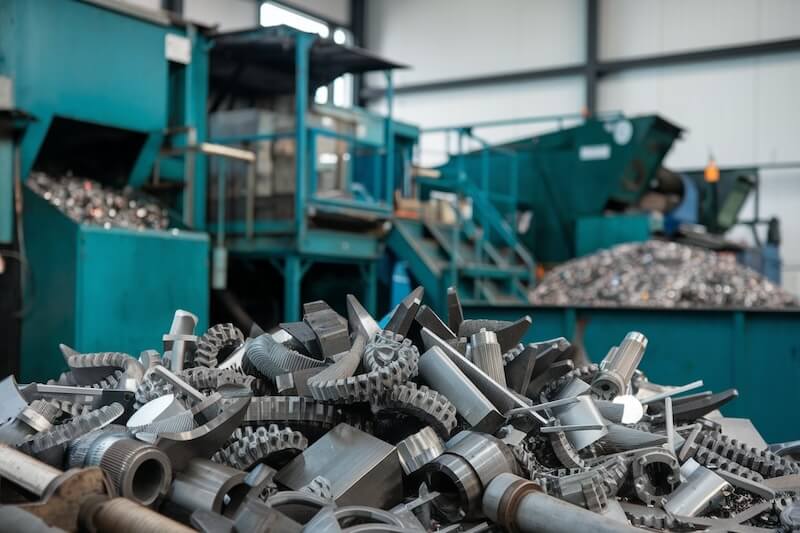
Partnering with Retop: Expertise, Customization, and Support
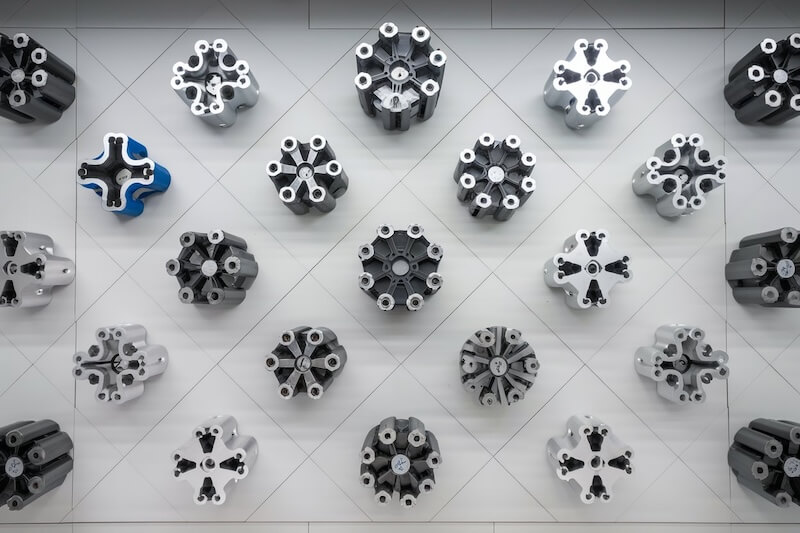
Retop’s specialized knowledge in tungsten carbide manufacturing ensures that automotive clients receive tailored solutions, expert guidance, and reliable partnerships.
Details:
- Engineering Support: Retop’s technical team helps select the right tungsten carbide grade and tool geometry to meet specific automotive applications.
- Custom Solutions: Whether it’s for complex engine parts or intricate transmission gear sets, Retop can design and produce tools that perfectly match production requirements.
- Customer Commitment: Responsive after-sales support, ongoing consultation, and continuous improvement initiatives ensure maximum value over time.
Future-Proofing the Automotive Manufacturing Process
As automotive designs evolve and requirements become more stringent, tungsten carbide tools position manufacturers to adapt quickly and stay ahead of industry changes.
Details:
- Advanced Materials Compatibility: New metals, alloys, and composites used in next-generation vehicles can be effectively machined with tungsten carbide solutions.
- Scalability: Whether ramping up for large-volume production or refining niche, high-precision components, tungsten carbide tools offer flexibility and reliability.
- Long-Term Investment: Investing in quality tooling now sets the foundation for sustained productivity, profitability, and innovation as the automotive landscape evolves.
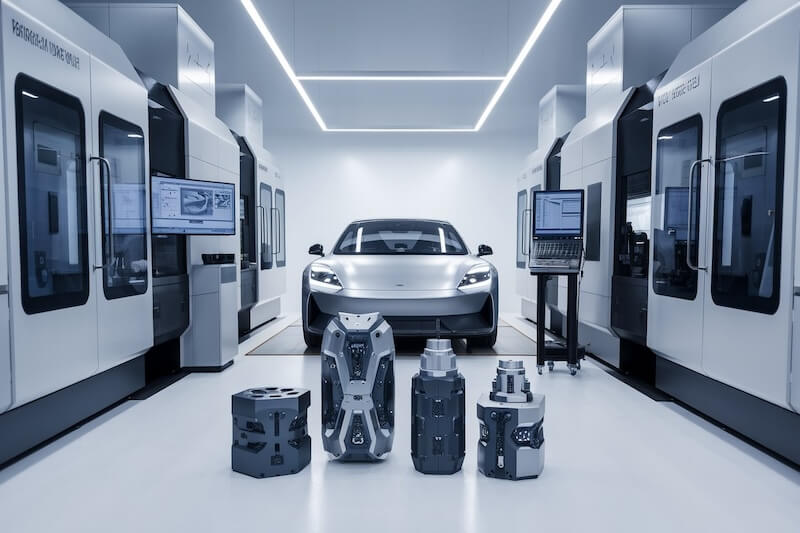
Conclusion
From improved precision and reliability to cost savings and sustainability, tungsten carbide tools transform automotive manufacturing operations.
For CEOs seeking to enhance competitiveness and for machine operators eager to improve day-to-day efficiency, tungsten carbide solutions—especially those provided by Retop—offer a clear pathway to success.
By embracing these high-performance tools, automotive manufacturers can confidently meet the challenges of today’s market and prepare for the demands of tomorrow’s vehicles.
Quick and easy: Enter your specifications and get a quote in one business day