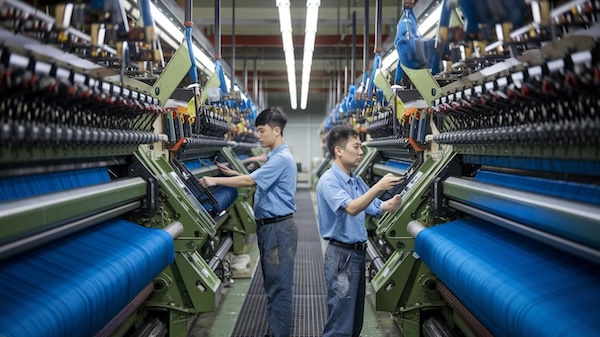
Carbide Textile Wear Parts
Retop designed to provide a comprehensive understanding of tungsten carbide wear parts in the textile industry. We aim to inform equipment operators and decision-makers within textile companies about the benefits of adopting tungsten carbide components, how they compare to other materials, and what strategic advantages they bring in terms of durability, efficiency, and cost-effectiveness.
Quick and easy: Enter your specifications and get a quote in one business day
Table of Contents
Expertise in Tungsten Carbide Textile Wear Parts
Retop Carbide provides a diverse range of products for the textile industry. We specialize in refurbishing worn textile presser feet and feed dogs by re-tipping them with tungsten carbide, increasing their lifespan by at least 5 times.
Types of Tungsten Carbide Textile Wear Parts Tooling
- Carbide Tipped Feed Dogs
- Carbide Tipped Presser Feet
- Textile Presser Feet
- Tungsten Carbide Knives
- Carbide Tipped Knives
- Other
Introduction: Navigating Today’s Textile Industry Challenges
As consumer demand for textiles grows more complex—requiring faster production cycles, intricate patterns, and consistently high quality—textile equipment faces increased strain. Traditional wear parts, such as those made from standard steels or aluminum alloys, often struggle to keep up, leading to inefficiencies and costly downtime. Tungsten carbide wear parts emerge as a solution, engineered to withstand demanding conditions and support high-volume, precision manufacturing.
Details:
- Market Pressures: With intense global competition, textile companies must seek out advanced materials that enhance productivity.
- Importance of Reliability: Equipment that fails or requires frequent maintenance hinders output, undermining profitability and customer satisfaction.
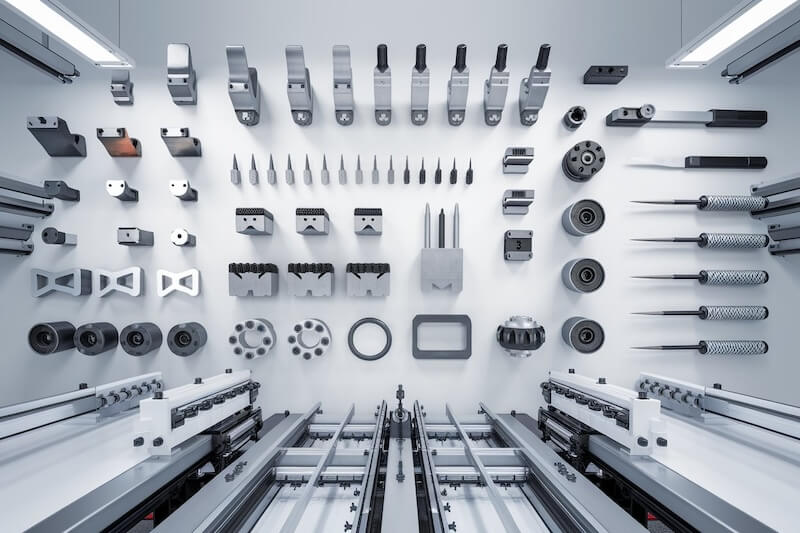
Understanding Tungsten Carbide: What Sets It Apart
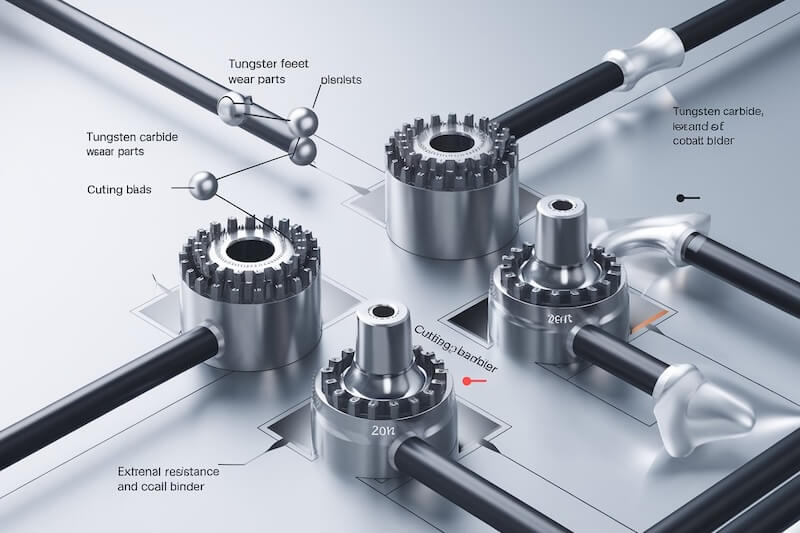
Tungsten carbide is not just another material—it’s a high-performance composite renowned for its exceptional hardness, toughness, and wear resistance, making it ideal for demanding textile applications.
Details:
- Composition: A blend of tungsten carbide particles and a metallic binder (typically cobalt), sintered at high temperatures to form a robust, ultra-hard structure.
- Material Properties: Exceptional hardness places it near diamond on the hardness scale. It resists deformation, stands up to abrasive fibers and yarns, and endures high-speed operation.
- Thermal Stability: Tungsten carbide remains dimensionally stable under elevated temperatures, ensuring consistent performance even in continuous, fast-paced production lines.
Common Tungsten Carbide Wear Parts in Textile Equipment
Tungsten carbide can be integrated into various components of textile machinery, each playing a critical role in the overall efficiency and product quality.
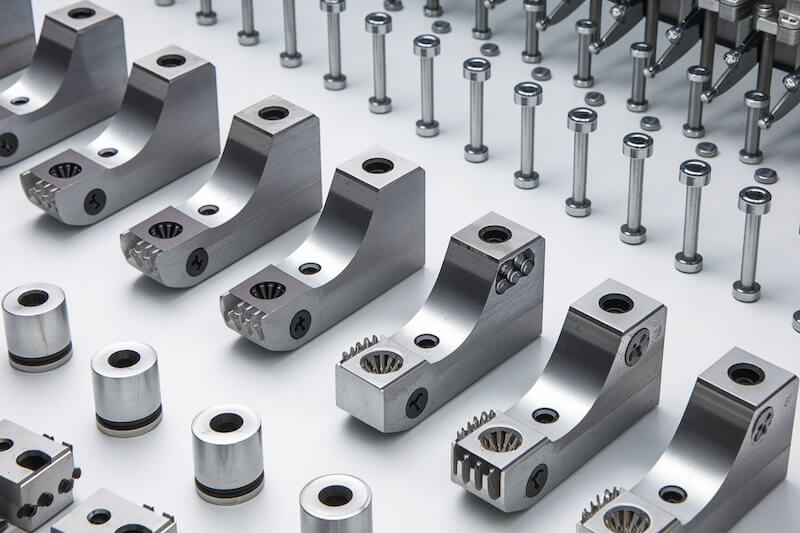
Presser Feet and Feed Dogs
Upgraded with tungsten carbide tips, these components last significantly longer, maintaining feed accuracy and reducing tension issues.
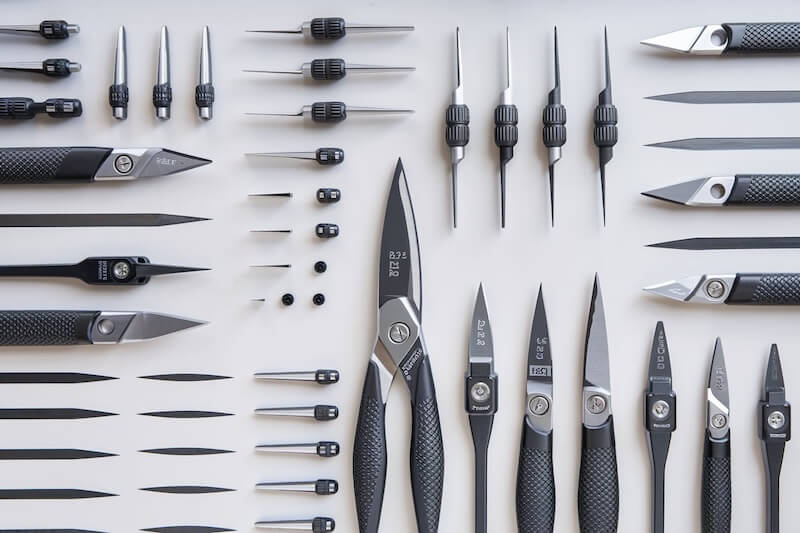
Cutting Blades and Shears
Carbide-tipped cutting tools deliver clean, precise cuts through abrasive materials, prolonging blade life and reducing downtime.
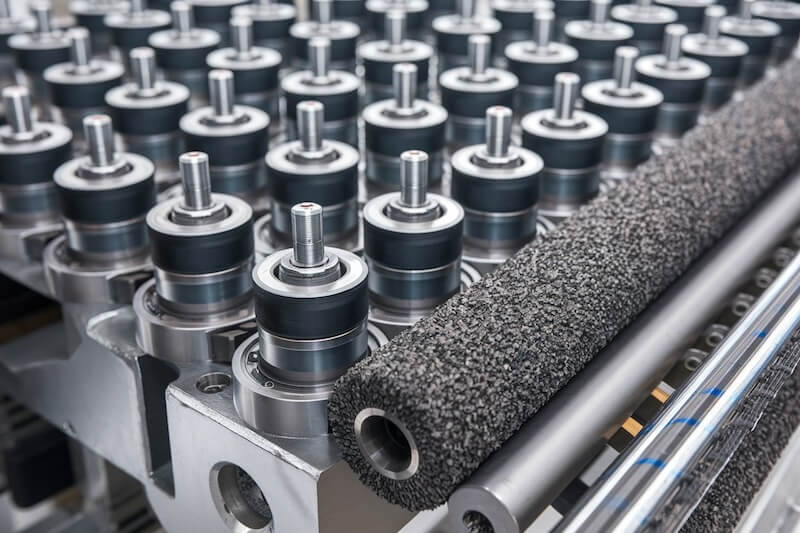
Guides, Bushings, and Rollers
Carbide’s superior wear resistance ensures these guiding components maintain accurate yarn tension and alignment over extended periods.
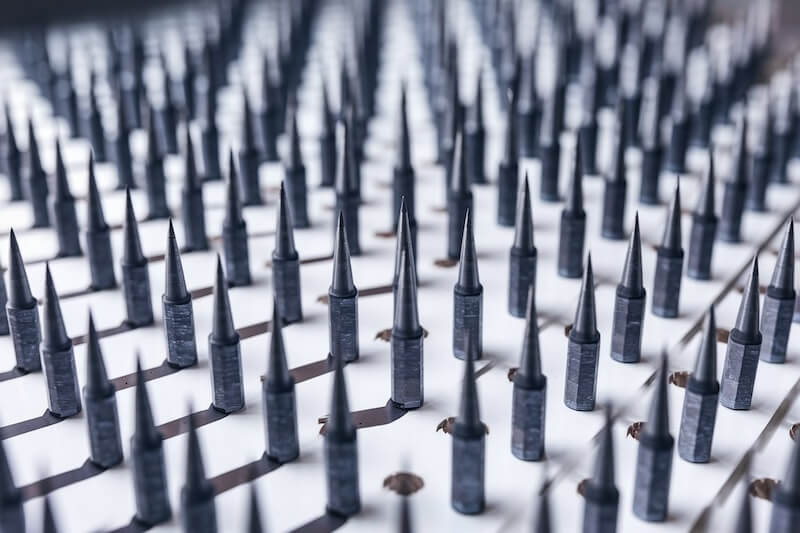
Specialized Inserts and Needles
From tufting to weaving, carbide elements maintain their form and sharpness, improving product consistency and machine reliability.
Quick and easy: Enter your specifications and get a quote in one business day
Comparing Tungsten Carbide to Other Materials
While traditional metals or coated components have long been used in textile machinery, tungsten carbide often outperforms them on key performance indicators.
Details:
- Steel vs. Tungsten Carbide: Steel tools wear down more quickly, losing their edge and requiring frequent replacements. Tungsten carbide’s hardness translates directly into less downtime and fewer tool changes.
- Ceramics vs. Tungsten Carbide: Though certain ceramics are hard, they can be brittle. Tungsten carbide, on the other hand, balances hardness with toughness, reducing the risk of sudden fractures.
- Coated Alloys vs. Solid Carbide: Surface coatings on cheaper alloys wear away, eventually exposing less durable substrates. Tungsten carbide is robust throughout its structure, ensuring consistent performance.
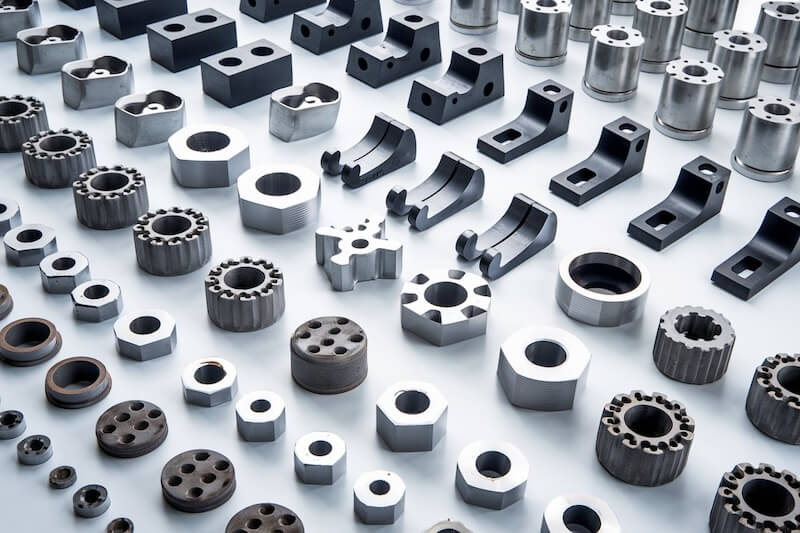
Operational Advantages: Durability, Precision, and Efficiency
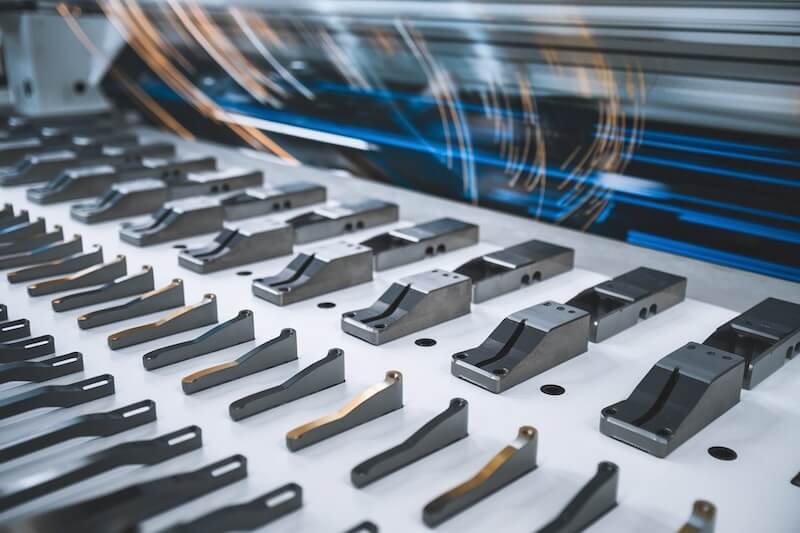
Tungsten carbide wear parts don’t just last longer—they improve the entire production process, leading to a leaner, more effective operation.
Details:
- Extended Tool Life: Significantly fewer tool changes minimize downtime, lower labor costs, and streamline inventory management.
- Improved Quality Control: Consistent tool geometry and sharpness yield uniform fabric quality, reduced defects, and enhanced finish.
- High-Speed Performance: With components that resist wear and maintain stability at high speeds, manufacturers can push output rates without compromising quality.
Cost Savings and Long-Term Value
Although tungsten carbide parts may require a higher initial investment, their durability and performance lead to notable long-term savings and a stronger ROI.
Details:
- Reduced Maintenance Costs: Longer intervals between replacements and adjustments mean fewer maintenance intervals, cutting both labor and parts expenses.
- Less Scrap and Rework: High-quality production reduces material wastage, saving on raw materials and increasing profitability.
- Predictable Expenditures: Planning production schedules and maintenance around reliable tungsten carbide tools leads to more accurate budgeting and forecasting.
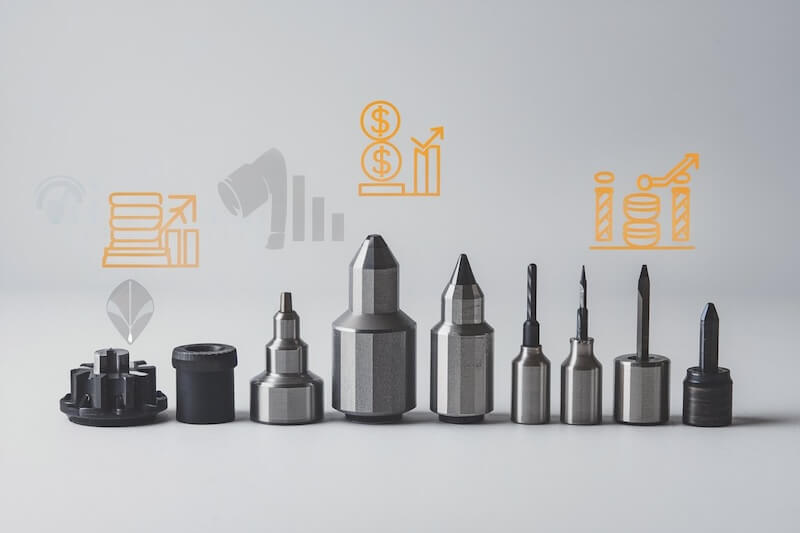
Sustainability and Environmental Responsibility
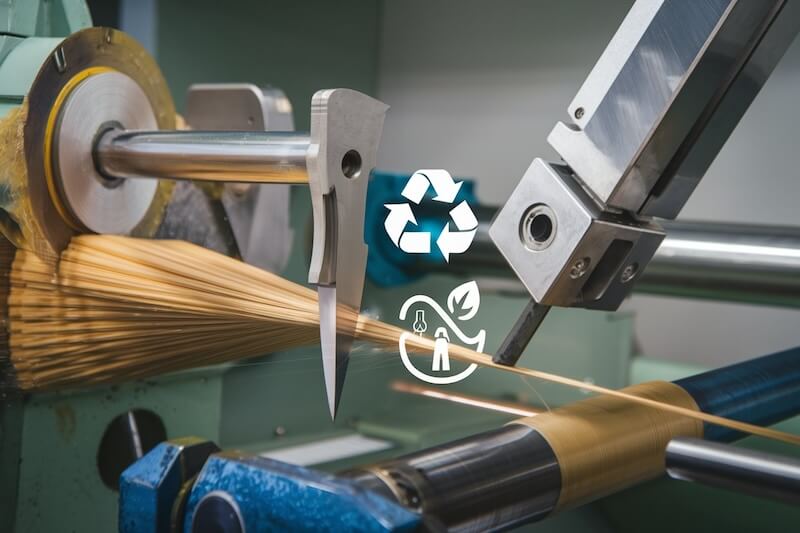
In an era where sustainability is increasingly important, tungsten carbide contributes by extending tool lifecycles and reducing waste.
Details:
- Fewer Discarded Parts: Long-lasting tools mean fewer worn-out components end up in landfills, minimizing the environmental footprint.
- Energy Efficiency: Efficient cutting and guiding reduce the energy required for reworks or slowdowns, indirectly lowering the carbon footprint of textile operations.
- Brand Image: As consumers become more environmentally conscious, investing in durable tooling demonstrates corporate responsibility, potentially enhancing a company’s brand reputation.
Choosing the Right Tungsten Carbide Supplier and Future-Proofing Operations
Selecting a reputable supplier that can tailor tungsten carbide solutions to your specific textile equipment ensures maximum value and adaptability to future industry demands.
Details:
- Customized Solutions: Expert suppliers can fine-tune carbide grades, tip shapes, and surface finishes to suit specialized textile processes.
- Technical Support and After-Sales Service: Ongoing guidance helps manufacturers optimize their tools for optimal performance and longevity.
- Staying Ahead of the Curve: As textile processes evolve—introducing new fabrics, tighter tolerances, or faster production lines—tungsten carbide’s proven reliability makes it the best foundation for future expansions and improvements.
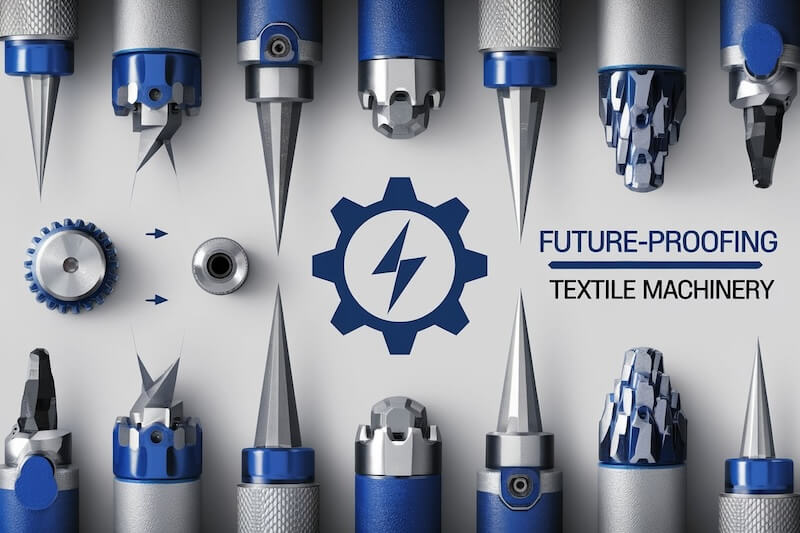
Conclusion
In an industry where precision, efficiency, and cost-effectiveness reign supreme, tungsten carbide wear parts offer textile manufacturers a competitive edge.
From their exceptional hardness and longevity to their impact on quality control, energy efficiency, and sustainability, tungsten carbide components represent a strategic upgrade over conventional materials.
By understanding the material’s properties, exploring different wear part applications, and recognizing the long-term advantages, textile companies can confidently invest in tungsten carbide solutions, ensuring their operations remain competitive, resilient, and future-ready.
Quick and easy: Enter your specifications and get a quote in one business day