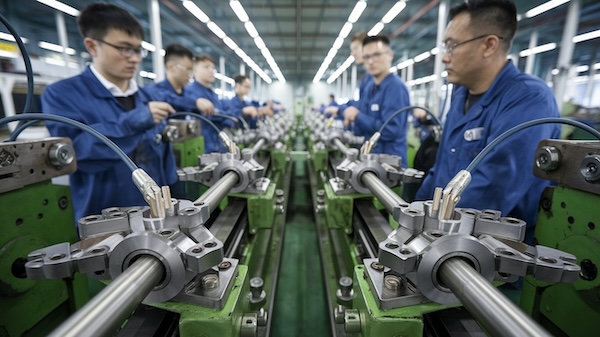
Carbide Wire Forming And Shaping Tooling
Retop Carbide designed to help wire forming and shaping tooling manufacturers understand the advantages of using tungsten carbide. By comparing it to alternative materials, detailing its core properties, and highlighting its cost-saving and quality-improving features, we aim to convince skeptics that tungsten carbide stands as the superior choice.
Quick and easy: Enter your specifications and get a quote in one business day
Table of Contents
Expertise in Wire Forming And Shaping Tooling
Whether you are flattening, shaping or drawing, you can rely on Retop Carbide various Tungsten Carbide Wire Forming Tooling and Carbide Draw Dies to meet your expectations.
Types of Wire Forming And Shaping Tooling
- Turkshead Rolls
- Flattening Rolls
- Curling Rolls
- Shaping Rolls
- Capstan Rolls
- Carbide Draw Dies
- Forming Dies
- Shaving Dies
- Draw Plugs
- Other
Introduction: The Evolving Demands of Wire Forming and Shaping
As wire forming and shaping processes become more sophisticated, driven by rising quality standards and complex geometries, traditional tooling materials often fall short. Tungsten carbide, known for its exceptional hardness and wear resistance, emerges as a solution that meets these modern challenges head-on.
Details:
- Market Pressures: Industries such as automotive, electronics, and medical devices require increasingly intricate and reliable wire forms.
- Enhanced Productivity: Manufacturers need tools that maintain precision and reduce downtime, promoting stable, high-volume production runs.
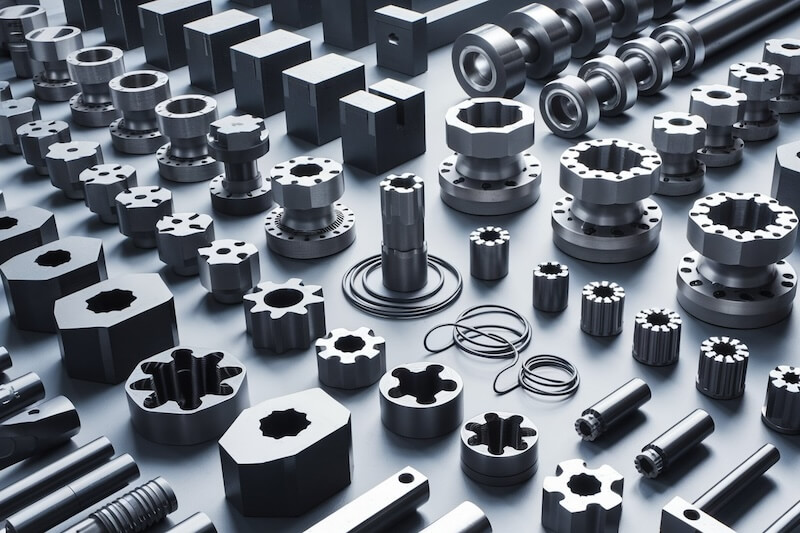
Understanding Tungsten Carbide’s Material Properties
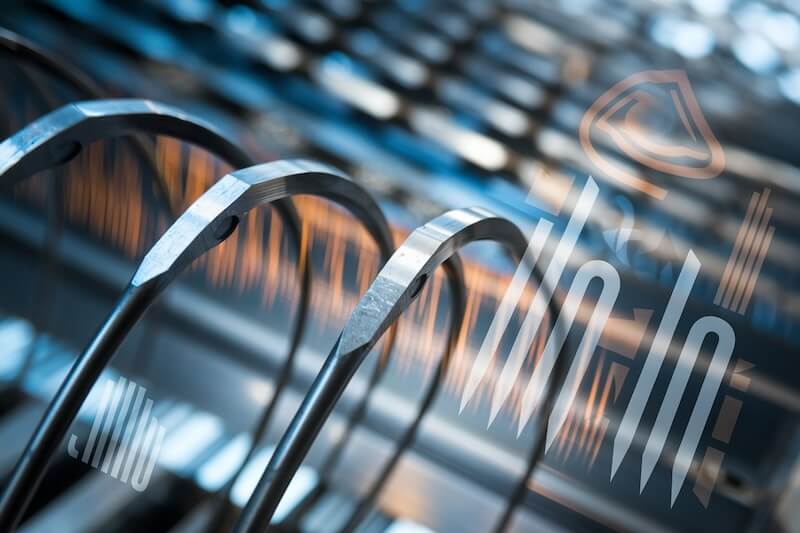
Tungsten carbide’s unique composition—a matrix of tungsten carbide particles bonded by metal binders—offers a balance of hardness, toughness, and dimensional stability beyond what most traditional metals provide.
Details:
- Near-Diamond Hardness: Ensures exceptional resistance to abrasion and deformation, even under high-stress conditions.
- Thermal Stability: Maintains structural integrity at elevated temperatures, preserving tight tolerances and consistent tool performance.
- Longevity and Reliability: Prolonged tool life reduces changeovers and ensures consistent product quality.
Comparing Tungsten Carbide to Other Tooling Materials
While tool steels, coated alloys, and ceramic composites have their place, tungsten carbide often surpasses them on critical factors like durability, accuracy, and overall cost-effectiveness.
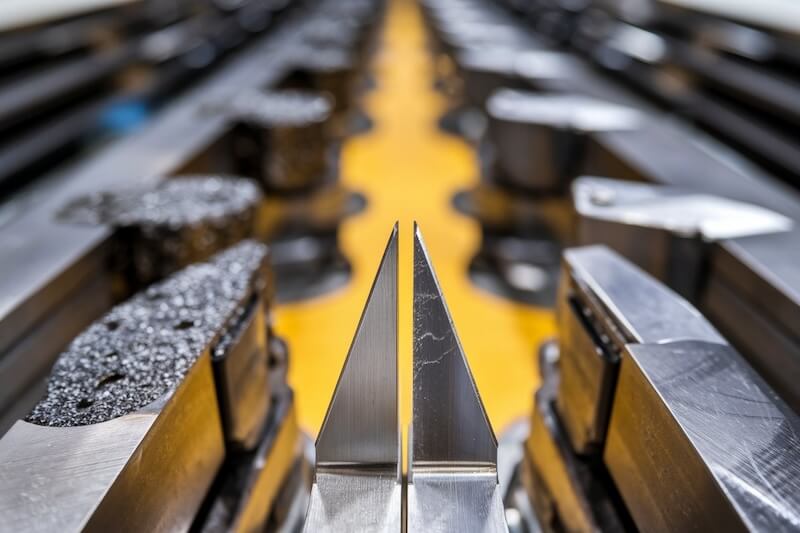
Versus Tool Steel
Tungsten carbide outlasts steel tools by a significant margin, reducing frequent replacements and production interruptions.

Versus Coated Tools
Coatings eventually wear away, exposing weaker substrates. Tungsten carbide’s core strength persists throughout its entire structure.
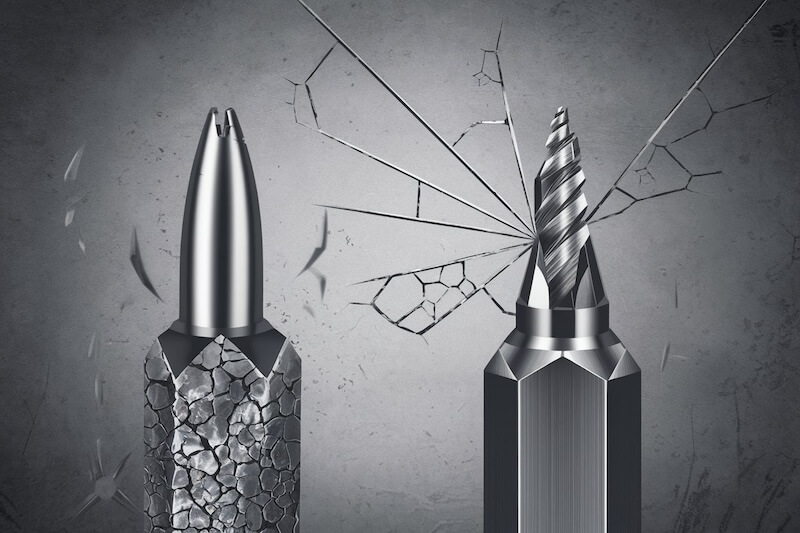
Versus Ceramics
Ceramics can be brittle. Tungsten carbide blends hardness and toughness, minimizing the risk of sudden tool failures.
Quick and easy: Enter your specifications and get a quote in one business day
Reduced Downtime and Maintenance
The extended wear life of tungsten carbide tooling means fewer stoppages for regrinding, maintenance, or replacements—directly impacting operational efficiency and profitability.
Details:
- Longer Tool Life: Less frequent maintenance frees operators to focus on meeting production targets.
- Predictable Performance: Consistent tool geometry allows for stable production schedules and reduced scrap rates.
- Inventory Management: Investing in tungsten carbide tools simplifies spare part inventories, decreasing storage costs and complexity.
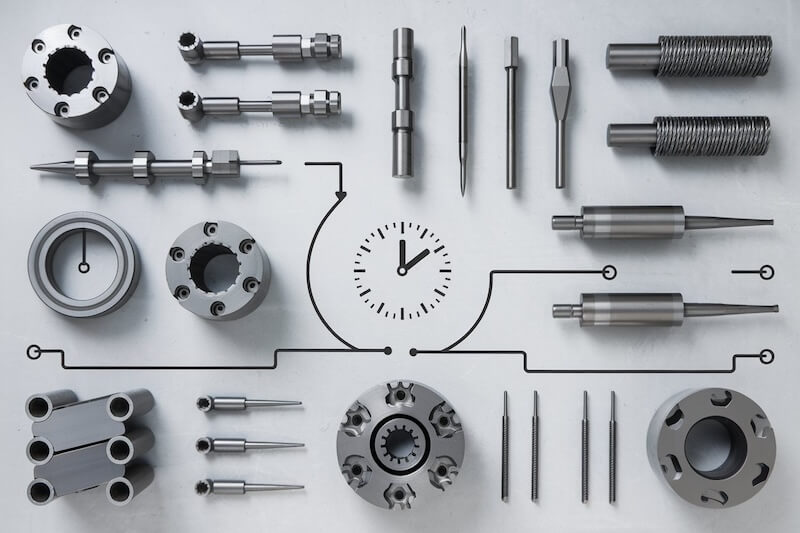
Enhancing Wire Quality, Precision, and Surface Finish

Tungsten carbide tooling doesn’t just last longer; it also contributes to better end-product quality, ensuring that formed or shaped wire meets strict specifications.
Details:
- Tight Tolerances: Consistent edge sharpness and geometry maintain precise wire diameters and shapes.
- Improved Surface Integrity: Cleaner, smoother finishes reduce friction and potential defects, fostering downstream process efficiencies.
- Reduced Defect Rates: With stable performance and minimal wear, carbide tools produce uniform output, minimizing rework and boosting customer satisfaction.
Operational Cost Savings and Long-Term ROI
Although tungsten carbide tools may cost more upfront, their reduced wear, improved efficiency, and enhanced part quality translate into substantial savings over time.
Details:
- Lower Replacement Costs: Fewer replacements mean a smaller tooling budget over the long run.
- Less Labor for Tool Changes: Operators spend less time swapping and adjusting tools, increasing overall workforce productivity.
- Higher Throughput: Enhanced efficiency supports faster cycle times and improved profit margins, justifying the initial investment.
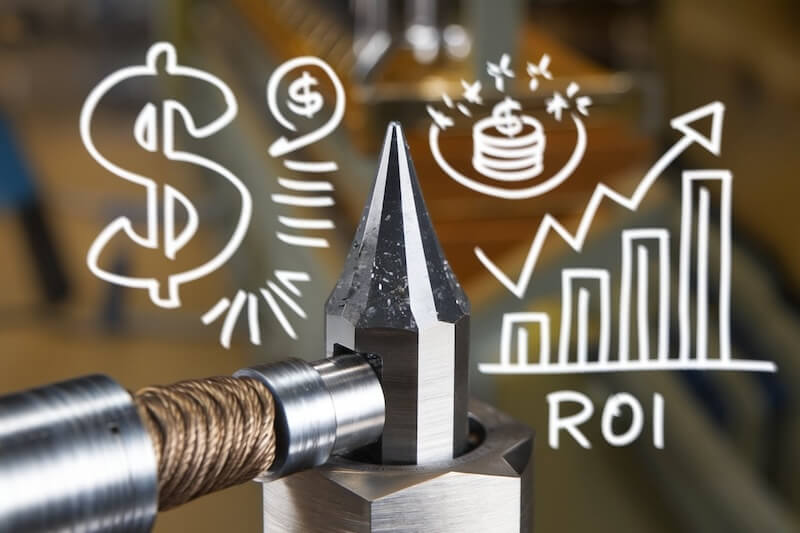
Versatility for Diverse Applications and Complex Designs
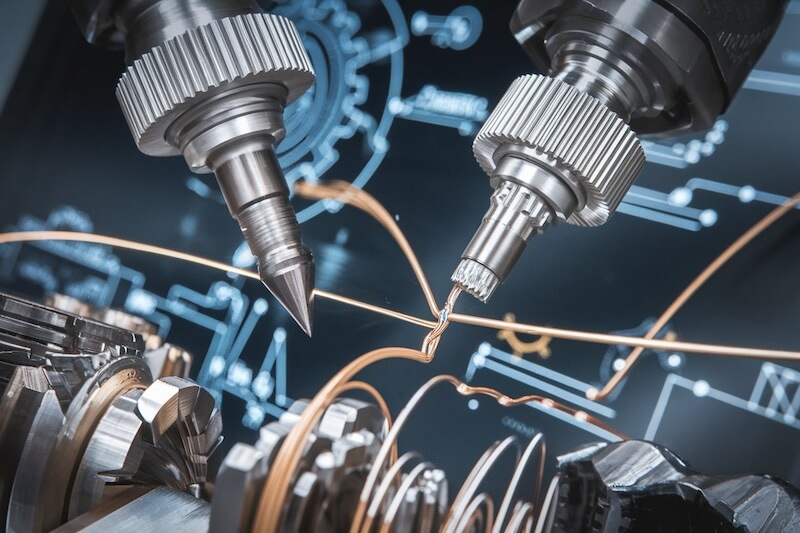
As wire formations become more intricate and materials vary widely—ranging from standard steel wire to specialty alloys—tungsten carbide tooling excels in handling these evolving demands.
Details:
- Challenging Materials: High-strength alloys, corrosion-resistant metals, and exotic wire materials are more manageable with carbide’s superior hardness.
- Complex Geometries: Intricate shapes benefit from carbide’s dimensional stability, enabling consistent manufacturing of custom designs.
- Future-Readiness: As market trends shift, tungsten carbide tooling remains adaptable, ensuring your operation can take on new challenges without compromising performance.
Building Long-Term Partnerships with Reputable Suppliers
To maximize tungsten carbide’s benefits, choose suppliers who understand your processes, provide customized tooling solutions, and offer ongoing technical support.
Details:
- Tailored Grades and Designs: Expert suppliers can adjust carbide grain sizes, binder ratios, and tool geometries to perfectly suit your application.
- Comprehensive Support: From initial consultation to after-sales service, a reliable partner ensures you realize the full potential of carbide tooling.
- Strategic Alliances: Establishing a long-term relationship with a trusted supplier encourages continuous improvement, innovation, and growth.
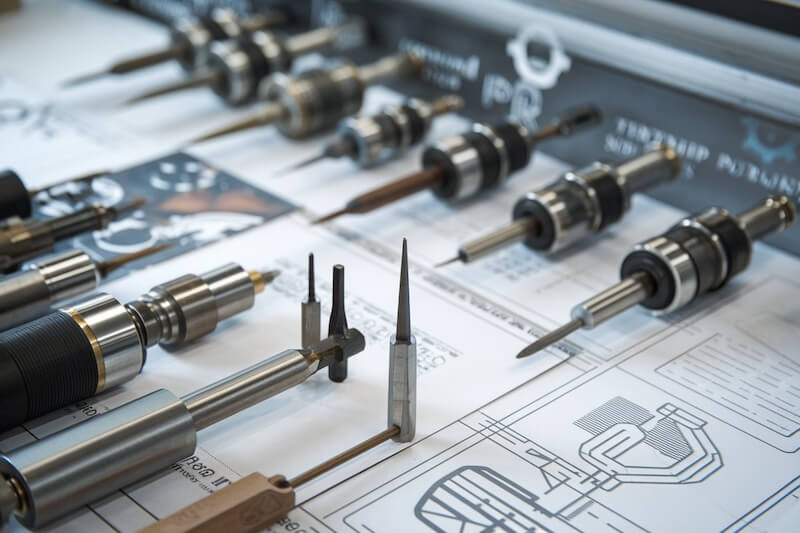
Conclusion
In a world where precision, reliability, and cost-effectiveness define success, tungsten carbide stands as the ideal tooling material for wire forming and shaping applications.
Its exceptional hardness, wear resistance, and dimensional stability translate into longer tool life, better product quality, and streamlined operations.
By understanding these advantages and partnering with reputable suppliers, you can confidently invest in tungsten carbide tooling—positioning your company at the forefront of the industry and paving the way for sustainable, long-term success.
Quick and easy: Enter your specifications and get a quote in one business day