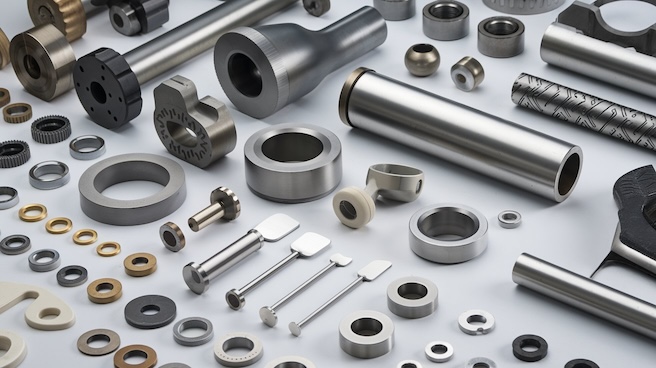
Tungsten Carbide Wear Parts and Specialty Components
In a competitive global market, industry leaders constantly seek materials that can enhance productivity, reduce downtime, and improve cost-effectiveness. Tungsten carbide, a composite material made primarily of tungsten and carbon, has emerged as one of the most reliable and versatile materials available today. From manufacturing and mining to aerospace and electronics, tungsten carbide stands as a game-changer, offering unmatched hardness, durability, and wear resistance.
Quick and easy: Enter your specifications and get a quote in one business day
Table of Contents
Types of Tungsten Carbide Wear Parts And Specialty Components
Retop delivers high-quality tungsten carbide wear parts, as well as specialty tungsten carbide components
Types of Wear Parts And Specialty Components
- Bushings
- Seal Rings
- Plungers
- Valve Seats and Stems
- Oil and Natural Gas Wear Parts and Components
- Nozzles
- Machined Parts
- High Pressure Pump Components
- Plungers
- Nozzles
- Seats & Stems
- Wire Guides and Rolls
Types of Rolls
- Curling
- Flattening
- Seaming
- Turks head
Types of Knives and Blades
- Slitting
- Shear
- Corner
- Chopping
Understanding Tungsten Carbide: Composition, Properties, and Manufacturing
Tungsten carbide’s unique composition fuses the strength of tungsten with carbon’s ability to deliver exceptional hardness and wear resistance.
- Composition: Primarily tungsten (WC) combined with a metallic binder (often cobalt), resulting in a composite that is significantly harder than tool steel.
- Properties: Exceptional hardness, high density, excellent wear resistance, and the ability to maintain structural integrity under high temperatures and pressures.
- Manufacturing: Produced through powder metallurgy techniques, allowing for precise control over composition and microstructure to meet unique industrial specifications.
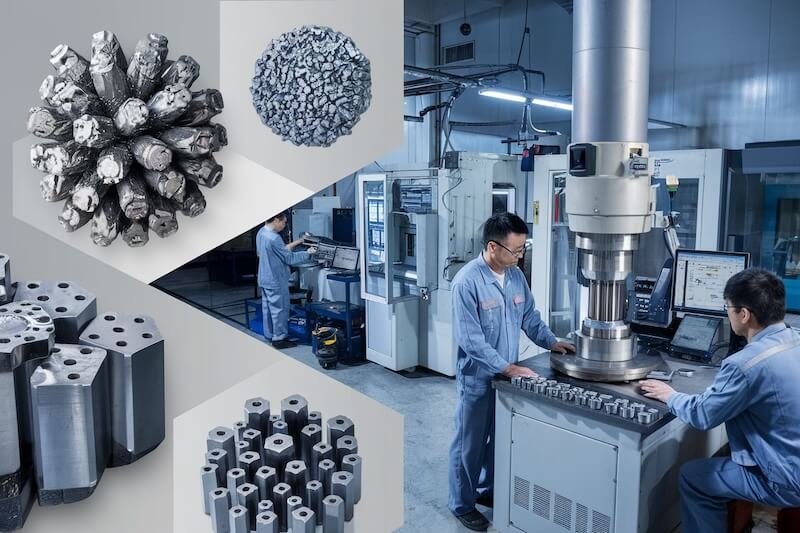
Advantages Over Traditional Materials
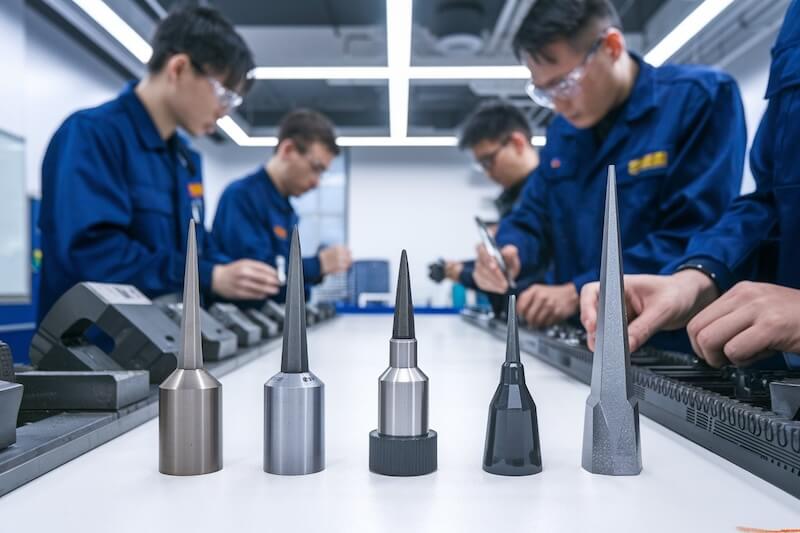
- Extended Component Lifespan: Its superior wear resistance reduces the frequency of replacements and maintenance.
- High Dimensional Stability: Maintains size and shape under extreme conditions, ensuring consistent results.
- Thermal and Corrosion Resistance: Delivers reliable performance in harsh environments, including chemical processing plants and high-temperature manufacturing lines.
Industry Applications: Mining, Oil & Gas, Automotive, Aerospace, and Beyond
Tungsten carbide’s versatility makes it a key player across multiple sectors.
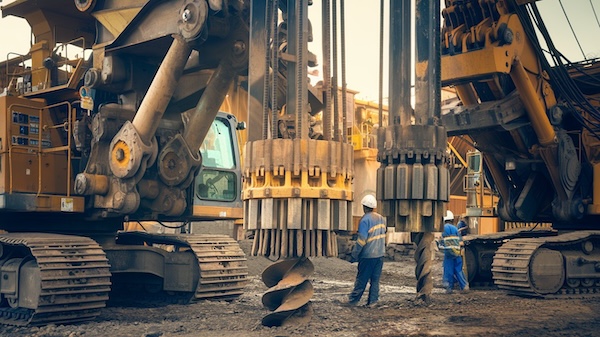
Mining & Oil/Gas
Used in drill bits, wear parts, and flow control components that withstand abrasive downhole conditions.
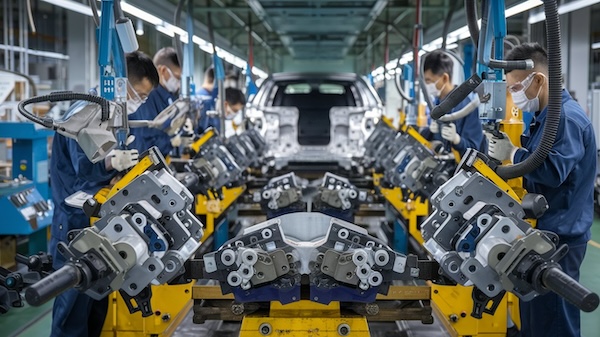
Automotive
Ideal for precision tooling, molds, and engine components that require long-lasting durability.
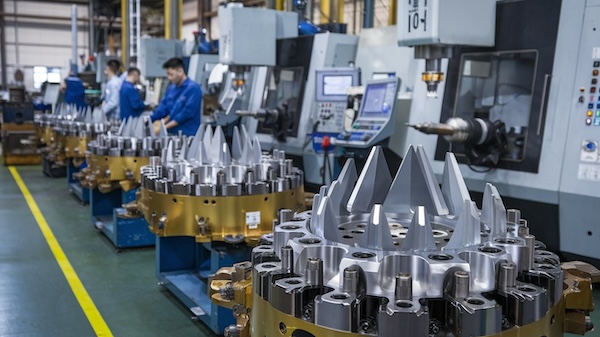
Aerospace
Enables the production of cutting tools and turbine components that endure high-speed operations and extreme temperatures.
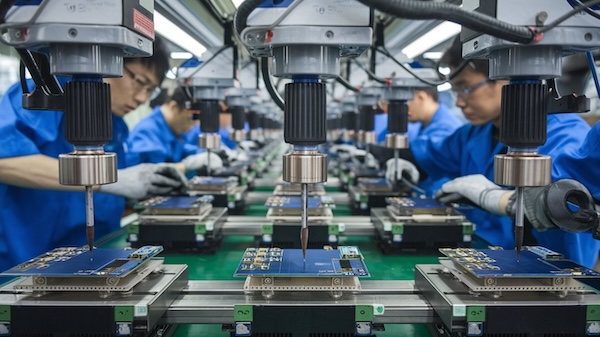
Electronics & Semiconductors
Offers precise, wear-resistant tooling for delicate fabrication processes.
Quick and easy: Enter your specifications and get a quote in one business day
Performance Under Extreme Conditions
Tungsten carbide’s exceptional mechanical properties ensure optimal performance even in the harshest operational environments.
- High-Pressure Endurance: Maintains integrity in deep-sea drilling or complex machining operations where components face immense stresses.
- Thermal Stability: Remains robust under extreme heat, allowing for high-speed machining without compromising accuracy.
- Corrosion Resistance: Prolongs tool life in chemically aggressive environments, reducing downtime and maintenance costs.
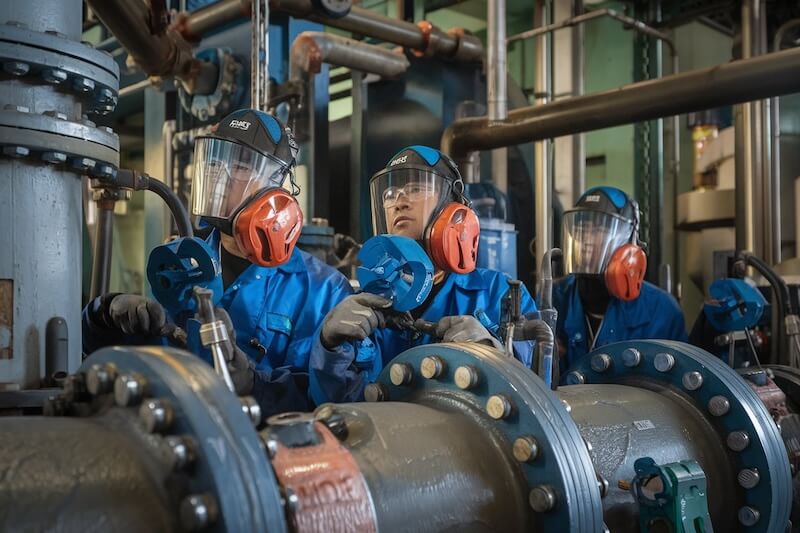
Customization, Flexibility, and Specialized Grades
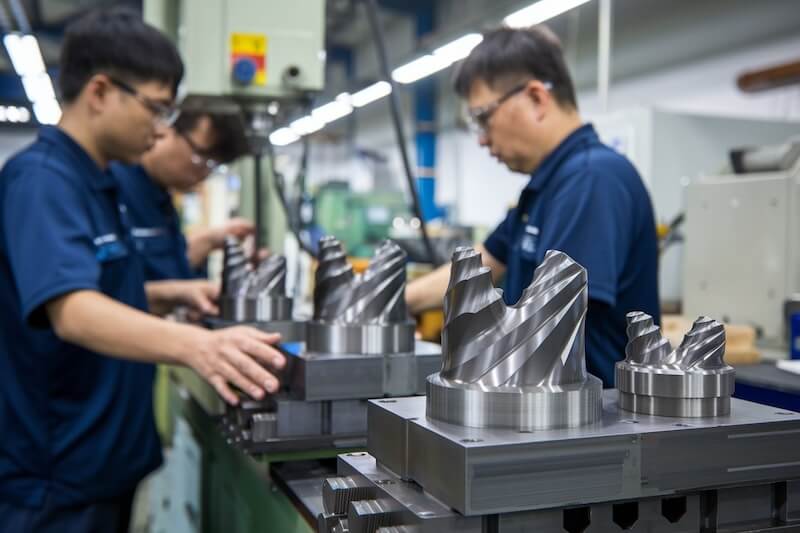
Tungsten carbide can be tailored to meet specific industry needs, ensuring a perfect match between material properties and application demands.
- Grade Variations: Different tungsten-to-binder ratios and grain sizes allow for customizable hardness, toughness, and wear resistance profiles.
- Precision Machining: Advanced fabrication methods enable the creation of highly complex shapes, optimizing component design.
- Integration with Coatings and Treatments: Combined with surface treatments, tungsten carbide can achieve even greater performance metrics, extending tool life and efficiency.
Sustainability and Environmental Responsibility
As sustainability becomes a strategic priority, tungsten carbide helps industries reduce their ecological footprint
- Longer Tool Life: Minimizing the frequency of part replacements cuts down on material consumption and waste.
- Recycling Programs: Tungsten carbide is recyclable, allowing for recovery and reuse of valuable tungsten resources.
- Reduced Energy Consumption: More durable tools require fewer production runs and less transportation, lowering overall energy use.
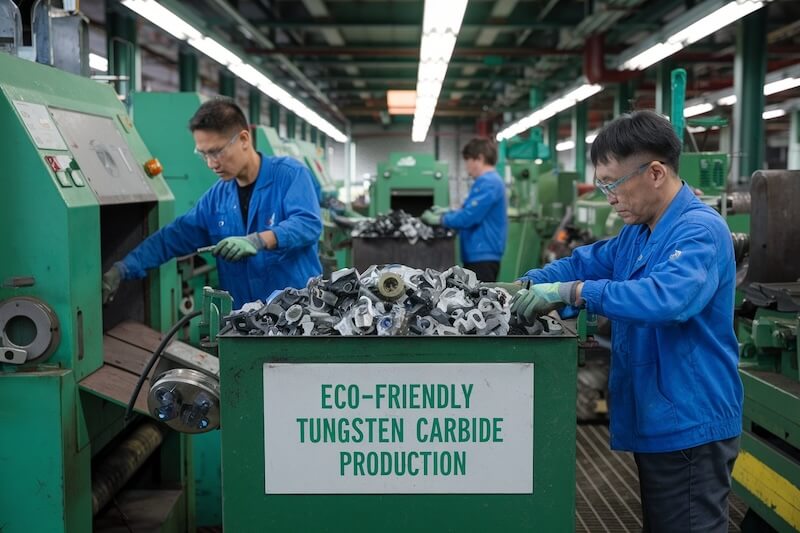
Reliable Supply Chains and Cost Management
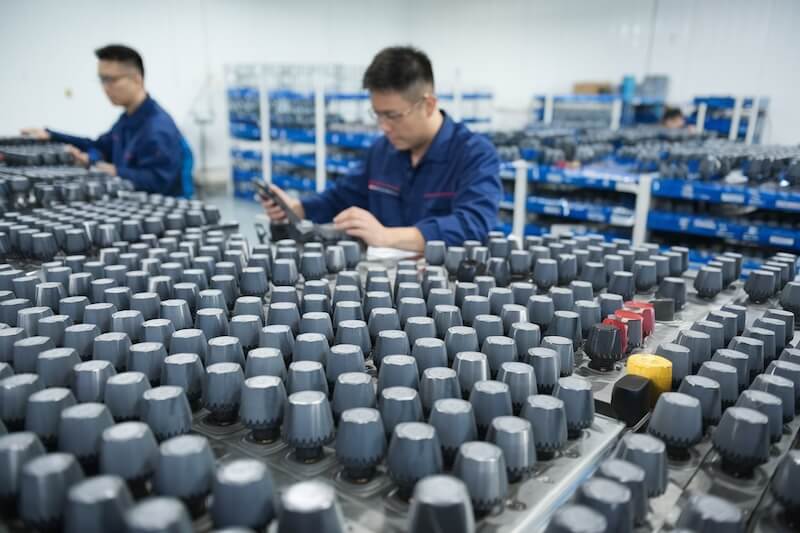
Investing in tungsten carbide products can lead to more predictable operations and better financial outcomes.
- Stable Production Schedules: Longer tool life and consistent performance help maintain continuous operation, reducing unplanned downtime.
- Cost Savings Over Time: While the initial investment may be higher, the extended lifespan and reduced maintenance more than offset the upfront costs.
- Quality Assurance: Established tungsten carbide suppliers maintain stringent quality controls, ensuring reliable and uniform product performance.
Strategic Integration: Moving From Concept to Implementation
Adopting tungsten carbide solutions involves thoughtful planning, informed partnerships, and strategic execution.
- Evaluation of Needs: Assess tooling requirements, operational challenges, and performance goals to identify the most suitable tungsten carbide solutions.
- Supplier Selection: Partner with reputable manufacturers who offer customization, technical support, and proven industry expertise.
- Gradual Implementation: Start with high-impact areas and scale up as results become evident, ensuring a smooth transition and maximum ROI.
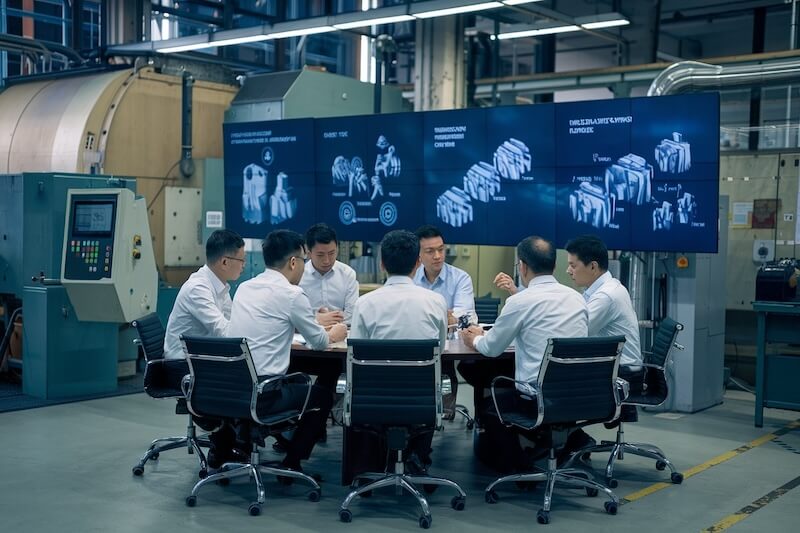
Conclusion
Tungsten carbide represents far more than just a material; it’s a strategic asset for CEOs and decision-makers looking to bolster their industry positions.
By understanding its composition, leveraging its unparalleled properties, and integrating it judiciously into operations, leaders can drive efficiency, ensure product reliability, and reduce environmental impact.
From the toughest downhole drilling conditions to the most intricate aerospace machining challenges, tungsten carbide stands at the forefront of industrial innovation. As global markets evolve and pressures intensify, those who recognize and harness the power of tungsten carbide will be better positioned to excel, innovate, and secure long-term success.
Quick and easy: Enter your specifications and get a quote in one business day